Overview

Read this article from a comprehensive knowledge base, updated and supplemented with articles reviewed by scientific committees.
Read the articleAUTHOR
-
Yves DESALOS: Ingénieur civil des Mines, Doctor of Science - Expert Métallurgie – Treatments RENAULT SA
INTRODUCTION
The introductory article has shown that, for the manufacture of a given part, the performance of the material used is obviously an initial dimensioning factor, but that the cost of the production range, which depends in particular on the judicious design of the functional parts, their ease of shaping and their connection modes, is often a decisive factor in industrial choice.
Heat treatments play a part in the choice of materials, either by broadening the possibilities for shaping the part, or by improving the material's properties of use, during or after shaping.
From a metallurgical point of view, heat treatment of metal alloys is based on structural changes in the solid phase, which have often been the first to be studied on special steels likely to undergo allotropic transformations. Of course, not all types of steel can be treated by means of allotropic transformation, either because their composition does not thermodynamically permit it, or because the metallurgy of the treatment in question does not require it. The objectives of steel treatments can be as varied as hot compositional homogenization, recrystallization after work-hardening at low temperatures, softening by slow allotropic transformation on cooling or by tempering, hardening by quenching and tempering, "structural" hardening, surface hardening by enrichment with interstitial elements...
For most alloy families, such as aluminum, allotropic transformations are not available, and hardening possibilities are limited to work-hardening or structural hardening.
This is the case for nickel-based superalloys, whose heat resistance (over 1,000 ˚C) is based on the simultaneous mastery of solid solution hardening of the matrix, optimum sequential precipitation morphology of several judicious phases, and grain boundary control.
In rarer cases, the possibilities of spinodal decomposition hardening can be used to obtain relatively interesting characteristics (e.g. Cu-15 Ni-8 Sn alloy), or to take advantage of shape memory effects when passing from one phase to another (e.g. brass with 20% Zn and 5% Al).
In all cases, – at least semi-quantitatively – can be associated with each type of post-treatment metallurgical structure, a set of properties characterizing either the shaping or the final state of use.
In this article, we summarize the main metallurgical aspects of heat treatment discussed in the introductory article. , the metallurgical basis for their development will be explained in greater detail in the following article. . In other words, as a reminder of the metallurgical fundamentals of heat treatment of metal alloys, the...
Exclusive to subscribers. 97% yet to be discovered!
You do not have access to this resource.
Click here to request your free trial access!
Already subscribed? Log in!
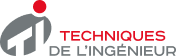
The Ultimate Scientific and Technical Reference
This article is included in
Metal treatments
This offer includes:
Knowledge Base
Updated and enriched with articles validated by our scientific committees
Services
A set of exclusive tools to complement the resources
Practical Path
Operational and didactic, to guarantee the acquisition of transversal skills
Doc & Quiz
Interactive articles with quizzes, for constructive reading
Metallurgical overview of heat treatments
Exclusive to subscribers. 97% yet to be discovered!
You do not have access to this resource.
Click here to request your free trial access!
Already subscribed? Log in!
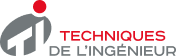
The Ultimate Scientific and Technical Reference