Overview

ABSTRACT
Aluminium alloys are widely used for their specific characteristics: light-weight, good corrosion resistance, thermal or electrical conductivity, etc. The anodizing treatments add several characteristics to the material such as corrosion resistance, hardness, thermal or electrical insulation, etc. They are used applications from transportation to the building sector and including leisure activities, decoration, mechanical or culinary parts. This article deals with these anodizing processes, their fundamentals mechanisms and their industrial implementation. Surface pre and post-treatments are presented as well as the properties of the anodic layers.
Read this article from a comprehensive knowledge base, updated and supplemented with articles reviewed by scientific committees.
Read the articleAUTHOR
-
Jean-Sylvestre SAFRANY: R&D engineer, surface treatments - Constellium C-TEC, Voreppe, France
INTRODUCTION
In principle, the discovery of the anodic oxidation of aluminum and its alloys closely follows that of the metal itself.
As early as 1857, Buff discovered that aluminum formed an oxide when placed as an anode in an electrolytic cell. In 1911, De Saint-Martin proposed the basic principles of sulfuric anodizing. In 1923, Bengough and Stuart developed chromic anodizing.
Subsequently, numerous refinements to anodic treatment processes were introduced, taking advantage of the great diversity available in this field. By modifying electrolytes, operating conditions and treated alloys, a wide variety of surface properties can be achieved.
While aluminum and its alloys are widely used for their intrinsic properties (lightness, good corrosion resistance, thermal or electrical conductivity, etc.), it should be stressed that anodizing treatments can be used to add very specific properties, depending on the application:
significantly improved corrosion resistance ;
improved hardness and abrasion resistance ;
reduced coefficient of friction ;
thermal insulation ;
electrical insulation ;
possibility of coloring ;
bonding base before organic coating or galvanic deposition, etc.
This is why anodizing processes are so widely used in industry today, for a wide variety of applications ranging from transport and construction to leisure, decoration, electronics, mechanical parts and cookware...
This article presents the various anodizing processes, their basic aspects and, for the most common ones, their industrial applications. The anodizing range must be considered in its entirety, which is why preliminary and subsequent treatments to anodic oxidation are also covered.
A glossary of terms is provided at the end of the article.
Exclusive to subscribers. 97% yet to be discovered!
You do not have access to this resource.
Click here to request your free trial access!
Already subscribed? Log in!
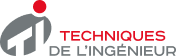
The Ultimate Scientific and Technical Reference
KEYWORDS
surface | aluminium | anodizing | oxide
CAN BE ALSO FOUND IN:
This article is included in
Metal treatments
This offer includes:
Knowledge Base
Updated and enriched with articles validated by our scientific committees
Services
A set of exclusive tools to complement the resources
Practical Path
Operational and didactic, to guarantee the acquisition of transversal skills
Doc & Quiz
Interactive articles with quizzes, for constructive reading
Anodizing aluminum and its alloys
Bibliography
Standards
- Anodizing aluminum and its alloys – Determination of mass per unit area (mass per unit area) of anodic layers – Gravimetric method. - • NF EN ISO 2106 - Avril 2011
- Anodizing aluminum and its alloys – Determining the thickness of anodic layers – Non-destructive method using an optical sectioning microscope. - • NF EN ISO 2128 - Octobre 2010
- Non-conductive coatings on non-magnetic base metal – Thickness measurement...
Appendices
Manufacturers – Suppliers – Distributors
(This list is not exhaustive)
Amet anodizing (70).
AB decometal (77).
Aloxan (67)....
Exclusive to subscribers. 97% yet to be discovered!
You do not have access to this resource.
Click here to request your free trial access!
Already subscribed? Log in!
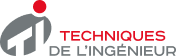
The Ultimate Scientific and Technical Reference