Overview

ABSTRACT
It is very difficult to give numerical values for the use of a tool in a material. These can be strongly influenced by the ma-chining environment, e.g. an inclined plane, a big length / diameter ratio, etc.
Therefore, the numerical values collected in this article are basic drilling data when the tool operation is not disturbed by the environment. Wherever possible, a range of data is given. The proposed minimum value must be respected absolutely (do not go below it); the maximum value can be reduced, for example to increase the tool life.
Read this article from a comprehensive knowledge base, updated and supplemented with articles reviewed by scientific committees.
Read the articleAUTHOR
-
François BAGUR: Self-employed – Consultant and trainer in machining engineering since 1987, Aulnay (17), France
INTRODUCTION
The first step to be taken by the machinist is to check the tool's qualification with regard to the material and the machining case. All the following numerical data apply to qualified tools.
These data are available for the main materials used by machinists. There are many other materials for which cutting parameters are available.
Materials on offer include non-alloyed multi-R m steels, low-alloyed multi-R m steels, ferritic, martensitic and austenitic stainless steels, GG and GGG cast irons, 2000, 6000 and 7000 series aluminum alloys, Inconel 718 nickel-based refractory alloys, grade 5 titanium alloys (TiAl6V).
Note: for some tool technologies, it is impossible to give default values for tool use. Each tool is a special case that needs to be studied individually. Only those technologies for which it is possible to specify values are covered.
For drilling technology, and more specifically for drilling with carbide monoblock drills, we differentiate between so-called standard drills and micro drills (diameters less than or equal to 3 mm). In fact, these two families of drills have their own specific characteristics, making it impossible to draw a behavioural law for diameters from 0.2 to 20 mm.
For one-piece drills, cutting parameters are arranged according to the tool's length/diameter (L/D) ratio.
The cutting parameters shown in the following tables for drilling are basic data. Unfortunately, they can vary considerably from one manufacturer to another, depending on the type of drill sharpening, especially for solid carbide twist drills. In the case of insert drills, these are also average values, as each manufacturer decides to change insert sizes to specific diameters.
Exclusive to subscribers. 97% yet to be discovered!
You do not have access to this resource.
Click here to request your free trial access!
Already subscribed? Log in!
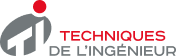
The Ultimate Scientific and Technical Reference
KEYWORDS
Cutting materials | High speed steel | Carbide | Ceramic | Diamond | Cutting speed | Federate per revolution | Chip thickness
This article is included in
Material processing - Assembly
This offer includes:
Knowledge Base
Updated and enriched with articles validated by our scientific committees
Services
A set of exclusive tools to complement the resources
Practical Path
Operational and didactic, to guarantee the acquisition of transversal skills
Doc & Quiz
Interactive articles with quizzes, for constructive reading
Materials for cutting tools
Bibliography
Standards and norms
- Cutting tool operating range – Tool-material pairing – Part 1: General presentation. - NF E66-520-1 - Septembre 1997
- Cutting tool operating range – Tool-material pairing – Part 2: General description. - NF E66-520-2 - Septembre 1997
- Cutting tool operating range – Tool-material pairing – Part 7: Application to solid drilling technology. - NF E66-520-7 - Novembre 2000
- Cutting tool operating range...
Exclusive to subscribers. 97% yet to be discovered!
You do not have access to this resource.
Click here to request your free trial access!
Already subscribed? Log in!
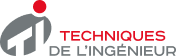
The Ultimate Scientific and Technical Reference