Overview

ABSTRACT
The welding of metal materials for assembly can result in modification of the isostatic lines and the local mechanical behavior of the material through the ties made. This article specifies the methodologies applicable to the calculation of assemblies subjected to variable loading, and the verification of the harmfulness of the defects outside the usual manufacturing tolerances. This presentation, which particularly concerns steels and aluminum alloys, and which makes extensive use of normative documents from the field of construction, endeavors to be complete, explanatory and up-to-date.
Read this article from a comprehensive knowledge base, updated and supplemented with articles reviewed by scientific committees.
Read the articleAUTHORS
-
Alain MICHEL: CNAM and ESSA engineer - Expert, lecturer - Institut de Soudure Industrie, Villepinte France - École Supérieure du Soudage et de ses Applications, Yutz, France
-
Alain MICHEL: CNAM and ESSA engineer - Expert, lecturer - Institut de Soudure Industrie, Villepinte France - École Supérieure du Soudage et de ses Applications, Yutz, France
INTRODUCTION
A large proportion of mechanical parts, including those whose function is to transmit motion, are subjected to variable stresses in service, exposing welded assemblies to failure by progressive fatigue cracking.
The dimensioning of a welded assembly under variable load is the final phase in the design of a mechanical part. This often neglected check is frequently the source of premature in-service damage, with far-reaching consequences for production units.
In the following sections, we discuss the dimensioning of welded joints subject to variable loads, and the verification of the suitability for use of welded joints with identified and characterized defects.
It is essential to note that this article is not a substitute for a design code; its main objective is to specify the methodologies to be used for fatigue analysis on the one hand, and the harmfulness of defects on the other, in the context of the construction of welded structures for mechanical purposes.
A table of acronyms and symbols is provided at the end of the article.
Exclusive to subscribers. 97% yet to be discovered!
You do not have access to this resource.
Click here to request your free trial access!
Already subscribed? Log in!
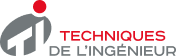
The Ultimate Scientific and Technical Reference
KEYWORDS
fatigue | mechanical engineering | welding | defect | welded joints
This article is included in
Mechanical functions and components
This offer includes:
Knowledge Base
Updated and enriched with articles validated by our scientific committees
Services
A set of exclusive tools to complement the resources
Practical Path
Operational and didactic, to guarantee the acquisition of transversal skills
Doc & Quiz
Interactive articles with quizzes, for constructive reading
Welded mechanical parts
Bibliography
Bibliography
Exclusive to subscribers. 97% yet to be discovered!
You do not have access to this resource.
Click here to request your free trial access!
Already subscribed? Log in!
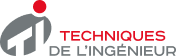
The Ultimate Scientific and Technical Reference