Overview

ABSTRACT
The PIM process combines the advantages of plastic injection moulding and powder metallurgy. This technique is particularly suitable for the production of small complex parts. Another advantage, the materials can be difficult to machine, since the finishing and polishing procedures are considerably reduced, or even eliminated, due to the surface state and the precision of the parts of excellent quality. The various steps of PIM technology, as well as specific issues such as the composition of the feedstock and the moulding conditions, are exposed. Sintering is the final step; the piece is heated for consolidation and densification. The theoretical aspects of this phenomenon and new sintering techniques currently under development are discussed.
Read this article from a comprehensive knowledge base, updated and supplemented with articles reviewed by scientific committees.
Read the articleAUTHORS
-
Delphine MOINARD: Teacher-Researcher - Materials Science Laboratory, École Catholique d'Arts et Métiers ECAM, Lyon - Arts et Métiers ParisTech, LaBoMaP, Cluny
-
Claire RIGOLLET: Lecturer-researcher, materials science laboratory; ECAM Lyon
INTRODUCTION
The powder injection molding (PIM) process was first adopted by the ceramics industry in the 1970s. The process then spread more widely to the field of metal powders. Although the PIM industry has experienced strong growth since its inception, the number of parts produced by this process remains on the order of a few percent compared with the total number of parts produced by conventional powder metallurgy and technical ceramics techniques.
The PIM process combines the advantages of plastic injection molding and powder metallurgy to produce complex parts in small, medium or large production runs, in materials that can be very difficult to machine. What's more, this process is particularly well suited to small parts. It is therefore virtually indispensable in the field of microtechnology.
Parts with highly complex shapes can be produced directly, or with only minor machining operations. Since the surface finish and precision of the resulting parts are excellent, finishing and polishing operations are greatly reduced, or even eliminated. Significant reductions in production costs are thus possible compared with sintering pressed parts, for example.
In this dossier, after comparing PIM technology with conventional processes, we describe the basic principles and typical problems encountered during the various stages (feedstock constituents and composition, molding and debinding conditions). We will then focus on sintering in the specific case of this process:
theory of the sintering phenomenon ;
details of equipment used in the industrial sector;
difficulties commonly encountered when sintering various materials (metallic and ceramic);
new techniques currently under development.
Exclusive to subscribers. 97% yet to be discovered!
You do not have access to this resource.
Click here to request your free trial access!
Already subscribed? Log in!
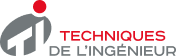
The Ultimate Scientific and Technical Reference
CAN BE ALSO FOUND IN:
This article is included in
Glasses and ceramics
This offer includes:
Knowledge Base
Updated and enriched with articles validated by our scientific committees
Services
A set of exclusive tools to complement the resources
Practical Path
Operational and didactic, to guarantee the acquisition of transversal skills
Doc & Quiz
Interactive articles with quizzes, for constructive reading
PIM sintering processes
Bibliography
Events
-
Congress organized by EPMA: EuroPM, held every year in Europe
-
Congress organized by the Metal Powder Industries Federation: PowderMet takes place every year in the USA
...
Patents
SCHWARTZWALDER (K.), Refractory body and method of making same, US Patent 2122960 (1938).
SMITH (D.J.), SHAPPIE (T.B.), SANFORD (R.A.), LIESZ (R.J.), Tungsten-carbide articles made by metal injection molding and method, US Patent 6790252 (2004).
MIYASHITA (T.), UENO (Y.), NISHIO (H.), KUBODERA (S.), Method for removing the dispersion medium from a molded pulverulent material, US...
Directories
Manufacturers – Suppliers – Distributors (non-exhaustive list)
-
Feedstocks
BASF
Polymer Chemie
...
Statistical and economic data
Exclusive to subscribers. 97% yet to be discovered!
You do not have access to this resource.
Click here to request your free trial access!
Already subscribed? Log in!
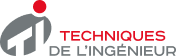
The Ultimate Scientific and Technical Reference