Overview

ABSTRACT
Mechanical or thermal surface treatments, thermomechanical treatments, thin coatings obtained by dry or liquid process and thick coatings obtained by hardfacing or hot isostatic compaction constitute the different categories of surface treatments of tool steels. They help to improve the properties of friction and wear resistance, mechanical or thermal fatigue resistance, oxidation or corrosion resistance. This article describes the functionalities provided by each category of processing previously described.
Read this article from a comprehensive knowledge base, updated and supplemented with articles reviewed by scientific committees.
Read the articleAUTHOR
-
Robert LÉVÊQUE: Mining engineer - Honorary Chairman of the Cercle d'études des métaux at the École nationale supérieure - des Mines de Saint-Étienne, Saint-Étienne, France
INTRODUCTION
The main aim of surface treatments for tool steels is to create a structure with gradient mechanical properties that improve resistance to friction and wear without compromising resistance to oxidation and corrosion, and resistance to mechanical, thermal and surface fatigue without compromising resistance to crack propagation and spalling. The processes commonly used to achieve these property gradients are mechanical (surface nanostructuring by mechanical attrition), thermal (surface quenching treatment) or thermochemical. The tribological characteristics of the surface can also be enhanced by thin coatings a few micrometers thick, providing protection against oxidation, corrosion or overheating in service. These coatings are produced by conventional liquid deposition techniques (notably electroplating), as well as by dry deposition techniques using chemical (CVD) and physical (PVD) methods. The combination of the property gradient obtained by thermal or thermochemical surface treatment and the hard coating obtained by one of the aforementioned techniques enables the surface properties of the tool steel to be optimized for its conditions of use. For certain applications, notably in the field of hot or cold forming tooling and certain wear parts, it is possible to use hot isostatic hardfacing or compaction, to obtain thick coatings, which can even reach several millimeters in thickness in the latter case. The last family of processes substantially enhances resistance to thermal fatigue and deformation, thanks to the use of nickel- or cobalt-based alloys with high hot mechanical properties.
The first part of this article covers mechanical, thermal and thermochemical structural transformation treatments. The second part covers thin coatings obtained by the liquid or dry process, and the last part covers thick coatings obtained by hot isostatic reloading or compaction.
At the end of the article, readers will find a glossary and a table of the notations used.
Exclusive to subscribers. 97% yet to be discovered!
You do not have access to this resource.
Click here to request your free trial access!
Already subscribed? Log in!
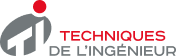
The Ultimate Scientific and Technical Reference
KEYWORDS
properties | surface treatment | tool steels
This article is included in
Metal treatments
This offer includes:
Knowledge Base
Updated and enriched with articles validated by our scientific committees
Services
A set of exclusive tools to complement the resources
Practical Path
Operational and didactic, to guarantee the acquisition of transversal skills
Doc & Quiz
Interactive articles with quizzes, for constructive reading
Surface treatment of tool steels
Bibliography
Standards
- Steel designation systems – Part 1: symbolic designation. - NF EN 10027-1 - 2-2017
- Steel designation systems – Part 2: digital systems. - NF EN 10027-2 - 6-2015
- Aciers à outils. - NF EN ISO 4957 - 6-2018
- Nitriding steels – Technical delivery conditions. - NF EN 10085 - 3-2002
Appendices
Organizations – Federations – Associations (non-exhaustive list)
Center technique des industries mécaniques (CETIM), BP 67, 60304 Senlis Cedex
Association de Traitement Thermique et de Traitement de Surface (A3TS), 71 rue Lafayette, 75009 Paris, France
Exclusive to subscribers. 97% yet to be discovered!
You do not have access to this resource.
Click here to request your free trial access!
Already subscribed? Log in!
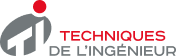
The Ultimate Scientific and Technical Reference