Safran va implanter une nouvelle usine sur la métropole de Rennes dédiée à la production d’aubages de turbines. Ce site industriel bénéficiera des dernières innovations technologiques du groupe et devrait atteindre la neutralité carbone lorsque tous les procédés innovants seront déployés.
Safran va construire un nouveau site de fonderie sur le territoire de la métropole de Rennes dédié à la production d’aubages de turbines. Ces aubes serviront à la fabrication de deux types de moteurs : dans le domaine militaire, le M88, qui équipe les Rafales, et dans le domaine civil, le moteur LEAP1 destiné aux Airbus A320neo et Boeing 737 MAX. Ce site devrait être opérationnel en 2027 et emploiera près de 200 personnes. Il sera la vitrine des innovations du groupe Safran et bénéficiera des meilleurs standards en termes de performance énergétique.
Cette nouvelle usine devrait produire 500 000 aubes par an. En comparaison, le site de Gennevilliers que possède Safran, fabriquant entre autres ces pièces, en produit 80 000, avec la particularité qu’il fabrique une grande diversité de modèles (80 références différentes). « Nous possédons déjà une usine en Chine qui produit des aubes à grande cadence, mais avec des technologies métallurgiques plus simples, déclare Emmanuel Vivier, directeur du centre d’excellence industrielle des aubes de turbines chez Safran Aircraft Engines. Sur ce nouveau site, l’objectif est de mettre en place des technologies plus avancées, tout en produisant en grande série, et pour l’instant nous ne possédons pas ce type d’usines dans le groupe. »
Le procédé mis en œuvre est celui de la fonderie à cire perdue. Les aubes sont d’abord produites en cire puis assemblées en grappes. Elles sont ensuite trempées dans de la céramique liquide, pour constituer des moules en céramique autour de cette cire. L’étape suivante consiste à cuire ces moules, ce qui a pour effet de faire fondre la cire, puis à couler du métal dans les moules afin de fabriquer les pièces finales.
Pour atteindre de grands volumes de production, toutes les étapes du procédé de fabrication seront automatisées, à l’image de ce que l’on peut rencontrer dans l’industrie automobile. Des bras de robots viendront positionner les pièces lors de chaque étape et les moules s’ouvriront, se rempliront et se fermeront automatiquement. Le système logistique sera lui aussi automatisé à l’aide de véhicules à guidage automatique (VGA ou AGV pour Automatic guided vehicle) qui déplaceront les pièces d’un poste à un autre.
250 paramètres du procédé de production analysés en temps réel
Une autre brique technologique concernera l’aspect digital et manufacturing 4.0 de cette usine. Environ 250 paramètres du procédé de production vont être collectés et suivis en temps réel grâce notamment au développement d’algorithmes d’intelligence artificielle. « Dans une fonderie traditionnelle, nous parvenons à en suivre une quarantaine, confie Emmanuel Vivier. Grâce au suivi de l’ensemble de ces paramètres, nous allons pouvoir être au plus proche de ce qui se passe et comparer les résultats avec nos outils de simulation numérique. L’analyse de toutes ces données va nous permettre d’optimiser le process, d’améliorer le niveau de qualité et baisser le taux de rebut. Cela contribuera aussi à baisser nos coûts de fabrication, tout en réduisant notre impact environnemental et énergétique. »
Un jumeau numérique de l’usine et de l’ensemble du système sera également créé. Il permettra de suivre en temps réel et d’optimiser le pilotage des flux, en analysant entre autres la manière dont les pièces se déplacent et à quels endroits elles attendent plus que d’autres. « Ce type de système apporte une meilleure compréhension du fonctionnement global en considérant l’usine comme un ensemble à part entière, analyse Emmanuel Vivier. Nous avons déjà en interne des jumeaux numériques à l’échelle d’un atelier, mais pas encore à l’échelle de tout un site, ce qui représente un niveau de complexité beaucoup plus élevé. »
Pour réduire l’impact carbone du site, le procédé de fabrication sera intégralement électrique et ne consommera aucune énergie fossile. Environ 20 % de la consommation électrique sera alimentée par l’énergie produite sur place grâce à des panneaux solaires installés sur les toits de l’usine et une partie des parkings. Pour les 80 % restants, Safran espère nouer des partenariats pour trouver de l’électricité renouvelable. Un système de récupération de la chaleur latente des fours sera également installé et branché sur le circuit de refroidissement des fours. L’entreprise envisage d’alimenter un réseau de chaleur urbaine en cours de construction sur le site de la Janais, là où sera implantée l’usine.
Un système de management de l’énergie (SME) pour lisser la consommation
Comme sur tous les sites du groupe Safran, un système de management de l’énergie (SME) sera déployé. Il procédera à des mesures et au suivi de la consommation énergétique, machine par machine, et un pilotage en temps réel de cette consommation dans le but de lisser la consommation et écrêter les pics. « La mise en route des fours ne sera pas réalisée au même moment, car le SME mettra en place une logique de séquençage pour récupérer la chaleur d’un premier four en phase de refroidissement pour préchauffer un autre par exemple », complète Emmanuel Vivier.
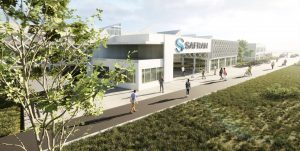
La construction de l’usine sera réalisée à l’aide de matériaux respectant les derniers standards relatifs aux normes environnementales. Une attention particulière sera portée à l’isolation, car le procédé de fabrication à cire perdue nécessite une maîtrise de l’hygrométrie et des températures, celles-ci ne devant pas dépasser 24 à 25 degrés. Un bon niveau d’isolation devrait permettre d’éviter des dépenses énergétiques liées à l’utilisation d’appareils de climatisation.
Tous les procédés innovants ne seront pas opérationnels dès l’ouverture de ce site, car certains nécessitent une plus grande maturation technologique pour atteindre le stade industriel. À terme, Safran souhaite que l’usine atteigne la neutralité carbone. « Comparé à une usine traditionnelle, notre objectif est de diviser au moins par trois la consommation énergétique, ramenée à la pièce produite, poursuit Emmanuel Vivier. Cette forte réduction s’explique en partie par le volume de production, car en introduisant deux fois plus de pièces dans un four de plus grande taille, il n’est pas nécessaire de le chauffer deux fois plus. Lorsque l’usine aura atteint son régime de croisière, je pense qu’il sera possible de diviser par cinq la consommation énergétique. »
[1] Le moteur LEAP est produit par CFM International, une coentreprise détenue à part égale par Safran Aircraft Engines et General Electric Aerospace
Réagissez à cet article
Vous avez déjà un compte ? Connectez-vous et retrouvez plus tard tous vos commentaires dans votre espace personnel.
Inscrivez-vous !
Vous n'avez pas encore de compte ?
CRÉER UN COMPTE