VoltR existe depuis un peu plus de deux ans et a développé une activité s’articulant principalement autour de deux axes.
D’abord, VoltR propose des services de collecte de batteries usagées, soit aux industriels qui en disposent et souhaitent s’en débarrasser, soit aux éco-organismes en charge de la coordination de la filière des batteries, Screlec-Batribox et Corepile.
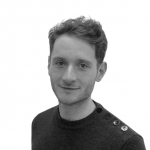
Dans les deux cas, il s’agit de mettre à disposition des détenteurs de batterie des contenants homologués destinés à stocker dans des conditions sécurisées les batteries, jusqu’à leur enlèvement et leur rapatriement jusqu’au centre de traitement de VoltR à Angers.
Le second axe d’activité de VoltR consiste à revaloriser les batteries usagées rapatriées sur le site de traitement selon un processus de réaffectation ou de remanufacture.
Maxime Bleskine, CEO de VoltR[1], a détaillé pour Techniques de l’Ingénieur les technologies mises en place pour revaloriser les batteries collectées, notamment en ce qui concerne la caractérisation de l’état des cellules lithium récupérées, étape nécessaire pour préparer leur seconde vie.
Techniques de l’Ingénieur : Une fois les batteries collectées, quelles sont les étapes successives mises en place par VoltR pour les revaloriser ?
Maxime Bleskine : En tout premier lieu, nous démantelons les packs batteries usagés, pour en dissocier les composants, en particulier les cellules lithium.
Nous avons développé une technologie innovante qui nous permet de tester ces cellules pour déterminer leur performance résiduelle et pronostiquer comment cette dernière va se comporter dans la durée. Cela va nous permettre in fine de pouvoir les rediriger vers des applications de seconde vie compatibles avec leur performance résiduelle. Une fois que cette évolution est pronostiquée, nous assemblons les cellules pour réaliser de nouvelles batteries, que l’on commercialise à des industriels intégrateurs, ou en tant que batteries de remplacement, à destination des industriels distributeurs.
Qu’est ce qui différencie la remanufacture et la réaffectation du reconditionnement classique ?
Deux éléments permettent de faire la distinction. Une batterie réaffectée ou remanufacturée fait l’objet d’une mise sur le marché, ce qui n’est pas le cas pour une batterie réparée par exemple. En cela, elle est soumise au paiement d’une éco contribution, et aux normes de certification en vigueur appliquées aux batteries issues de l’économie linéaire. Elles ont donc les mêmes niveaux de performance.
La deuxième différence, stipulée dans le règlement européen 1542 adopté en juillet 2023 par la Commission Européenne, est qu’une batterie réaffectée ou remanufacturée a une obligation de performance, ce qui n’est pas le cas pour le reconditionné.
Quels sont les segments de marché sur lesquels VoltR se positionne aujourd’hui ?
Les deux segments de marché sur lesquels nous opérons sont la micromobilité et les applications portables électroniques, que ce soit sur l’amont ou sur l’aval.
Nous développons aujourd’hui un troisième segment, avec la collecte de batteries de véhicules électriques en tant que flux entrant, pour produire des outils de stockage d’énergie en flux sortant, soit pour de l’autoconsommation, soit pour la redistribuer sur le réseau. C’est un marché complètement différent, sur lequel nous voulons mettre en place les solutions que nous développons d’ici la fin de l’année 2025.
Quels sont les challenges inhérents à l’évaluation des performances des batteries usagées collectées ?
Une batterie se dégrade de par l’utilisation qui en est faite, mais aussi avec le temps. Il y a donc de nombreux paramètres à prendre en compte pour voir comment une batterie évolue dans le temps en termes de performances. Quand nous récupérons une batterie, nous n’avons évidemment pas un historique de cette dernière, il nous faut donc dans un premier temps évaluer sa capacité résiduelle et sa résistance interne.
Nous utilisons des protocoles de détermination pour accéder à ces deux grandeurs. La problématique, c’est que deux cellules issues de la même usine, avec le même numéro de série, fabriquées le même jour pour la même application, et qui présentent les mêmes grandeurs à l’instant t, ne vont pas forcément évoluer ou se comporter de la même manière sur une même application de seconde vie.
Comment adressez-vous cette problématique ?
Nous construisons des bases de données grâce à des modèles de vieillissement reproduits en laboratoire. Ces bases de données vont permettre d’extrapoler, à partir des grandeurs récupérées lors de l’étape de caractérisation, le comportement des cellules dans la durée.
Nous associons à la fois de la modélisation électrochimique qui permet de comprendre les modes de vieillissement qui interviennent au sein des cellules, avec de la modélisation statistique – des algorithmes en réseaux de neurones avec des bases de données d’entraînement que nous avons construites nous-mêmes en laboratoire – qui nous permettent de mener les évaluations.
La revalorisation des batteries de véhicules électriques renferme-t-elle des challenges semblables à celle des batteries des outils de micromobilité ou des applications portables électroniques ?
La problématique est très différente du point de vue du flux entrant : la filière n’est pas organisée de la même façon que celles de nos autres flux entrants, les constructeurs automobiles sont aussi beaucoup plus intéressés pour mettre la main sur le gisement des batteries en fin de vie.
Que ce soit au niveau de l’opérationnel, de la partie aval, ce sont deux métiers différents, notamment car les puissances embarquées sont beaucoup plus importantes pour le stockage de l’énergie. Il y a d’ailleurs très peu d’acteurs qui travaillent à la fois sur les batteries embarquées et le stockage d’énergie.
Après, le stockage d’énergie est un débouché naturel pour les packs de batteries des véhicules électriques car ce sont des conditions d’utilisation qui sont assez peu stressantes. Aussi, il y a moins de variabilité sur les cellules de batteries des véhicules électriques que sur les outils portatifs, ce qui constitue un avantage pour caractériser leurs performances une fois collectées.
Propos recueillis par Pierre Thouverez
[1] VoltR
Cet article se trouve dans le dossier :
Le recyclage, maillon essentiel de la performance industrielle de la filière batteries
- « Si les gigafactories produisent moins de batteries, le modèle économique des usines de recyclage ne fonctionne plus »
- « Il faut que tous les acteurs de la filière des véhicules électriques soient à la fois présents sur le territoire et performants »
- « Nous associons modélisations électrochimique et statistique pour évaluer les performances des batteries usagées, à l'instant t et dans leur seconde vie »
- Le recyclage des batteries, thermomètre de la santé de la filière mobilité électrique
- Les débuts difficiles de la filière des batteries électriques européenne
- Bientôt de premières usines de recyclage de batteries en France
- Le recyclage des batteries a le vent en poupe
- Recyclage des batteries lithium-ion, un enjeu de taille pour l’avenir
- Les thèses du mois : "Le recyclage, maillon essentiel de la performance industrielle de la filière batteries"
- Vers des batteries plus durables construites en Europe
- Création d'une nouvelle filière de recyclage des batteries de véhicules électriques
- Batteries lithium-ion : de nombreux défis pour la transition
- Optimiser le recyclage des batteries de véhicules électriques
- Les ressources en matériaux, talon d'Achille de l'Europe des batteries ?
- L’extraction de lithium dans l’Allier en bonne voie
Dans l'actualité
- L’intelligence artificielle permettrait de prédire l’emballement thermique des batteries
- Les débuts difficiles de la filière des batteries électriques européenne
- Où seront produites les batteries du futur ?
- Les thèses du mois : « Le recyclage, maillon essentiel de la performance industrielle de la filière batteries »
- « Il faut que tous les acteurs de la filière des véhicules électriques soient à la fois présents sur le territoire et performants »
- Connaissez-vous le défi URGENSEA ?
- Valorisation des batteries usagées : recycler ou réutiliser ?
- Une nouvelle théorie sur l’origine de l’apparition de la vie sur Terre