Née en décembre 2019, Touch Sensity s’attelle depuis lors au développement d’une technologie novatrice de monitoring embarqué permettant de suivre, en temps réel et sans capteur spécifique, les différentes interactions physiques subies par le matériau constitutif d’une pièce structurelle. Une approche particulièrement prometteuse dans le domaine des moyens de transport, au sens large. À l’aube de la commercialisation d’une première solution destinée aux réservoirs d’hydrogène, la start-up travaille également à d’autres cas d’usage complexes, aux côtés des quelque 25 clients européens qui lui font déjà confiance.
Forte d’une équipe composée aujourd’hui de seize personnes, la jeune pousse dispose désormais de ses propres locaux au sein de la Cité de la Photonique à Pessac, près de Bordeaux, dans lesquels elle a implanté ses bureaux, mais aussi un laboratoire.
Après avoir mené à bien le développement de plusieurs prototypes préindustriels, Touch Sensity[1] s’attelle ainsi, désormais, à la réalisation de tests en environnements représentatifs, en jouant sur des paramètres tels que la pression, la température, ou encore l’ambiance saline du milieu.
Quand nous avions rencontré sa présidente et directrice technique Anna Pugach, en 2021, la start-up avait amené sa technologie à un niveau de maturité de 3, environ, sur l’échelle TRL. Elle en est aujourd’hui à un stade 6 à 7, et pourrait atteindre le niveau 7-8 d’ici peu, comme nous l’explique Mehdi El Hafed, co-fondateur et directeur commercial et financier de Touch Sensity. Un dirigeant qui lève également le voile sur les perspectives ouvertes par la levée de fonds de 3 M€ réalisée en mai dernier par la jeune entreprise.
Techniques de l’Ingénieur : Commençons, si vous le voulez bien, par quelques rappels. Quel est, dans ses grandes lignes, le principe de base de la technologie sur laquelle vous travaillez ?
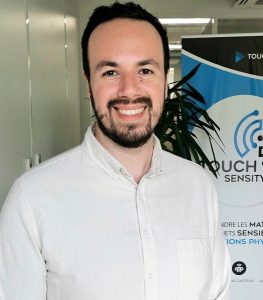
Mehdi El Hafed : Nous développons un système de monitoring qui permet de générer le modèle 3D d’une pièce structurelle et d’indiquer – en temps réel et à distance – tout ce qu’elle peut subir sur le plan des interactions physiques mécaniques : déformation, impact, endommagement, porosité, délaminage, torsion, dégradation thermique…
Concrètement, cette technologie se présente sous la forme d’un système électronique que l’on branche à la pièce, directement ou éventuellement via un câble d’une certaine longueur. En envoyant un signal au travers de la pièce, ce système va permettre de donner vie à un jumeau numérique en temps réel, comme on pourrait le faire avec un scanner portable.
Exclusive et brevetée, notre technologie n’utilise pas de capteur à proprement parler : c’est la pièce elle-même qui devient un capteur. Cela fonctionne avec de nombreux matériaux, les métaux, composites en fibres de verre et de carbone notamment. Nous faisons pour cela appel à un signal électrique, mais nous n’en exploitons pas directement les propriétés. Nous utilisons en effet des modèles mathématiques comparatifs – et non pas des modèles d’IA – qui nous permettent de comparer, à partir du signal émis, le signal reçu en temps normal et le signal reçu en cas d’interaction physique avec la pièce. Nous pouvons ainsi en déduire le type d’évènement subi par la pièce, sa localisation, ainsi que ses caractéristiques. Ces informations sont ensuite transformées en données numériques adaptées aux besoins du client, d’une cartographie 3D précise au millimètre à une simple caractérisation de la pièce indiquant si elle est à changer ou non.
Votre technologie se limite-t-elle justement à une « simple » évaluation qualitative des interactions subies par une pièce, ou permet-elle au contraire de quantifier le niveau, « l’intensité » de ces modifications physiques ?
Notre technologie permet effectivement de chiffrer ces modifications. Dans le cas d’une déformation, nous sommes par exemple en mesure d’évaluer cet aspect en pourcentage, avec une précision de l’ordre de 0,05 %. Nous pouvons aussi mesurer une fissure, localiser un impact… Certains évènements sont toutefois plus complexes que d’autres : dans le cas d’une oxydation par exemple, notre technologie permet uniquement de donner un ordre d’idée du niveau de cette dégradation par rapport à l’état normal de la pièce. Dans un cas comme celui-ci, notre solution ne remplace donc pas un capteur dédié, ou une analyse en laboratoire, mais permet en tout cas de fournir une première indication, une première vision sur l’état de la pièce, et ce, en temps réel et à l’aide d’une technologie embarquée.
Sur quels types de véhicules votre solution peut-elle être intégrée ? Comment l’accès à l’information se fait-il ?
Cette technologie peut être intégrée aussi bien à des avions qu’à des trains, des bateaux, des fusées ou encore des voitures, pour monitorer des pièces structurelles : le radôme ou les bords d’attaque pour un avion, le nez d’un train, le réservoir à hydrogène ou le pare-chocs de n’importe quel type de véhicule… Nous travaillons ainsi main dans la main avec nos clients pour intégrer ce système à l’électronique du véhicule en question.
L’accès aux informations se fait alors selon plusieurs niveaux de lecture : un simple voyant sur le tableau de bord d’une voiture, par exemple, indiquant à son conducteur que le réservoir d’hydrogène présente un défaut, mais aussi tout un ensemble de données bien plus précises auxquelles son garagiste pourra accéder via un dispositif mobile. Ces informations lui permettront ainsi de caractériser les dommages et d’en avoir un historique pour, in fine, le guider vers la meilleure solution de dépannage : réparation ou changement.
Dans le milieu aéronautique, ce seront cette fois des techniciens qui pourront directement récupérer les données une fois l’appareil au sol, alors que dans le ferroviaire, le transfert des données se fera en temps réel, au travers du même flux de données que celui déjà généré par tous les autres capteurs qui équipent déjà n’importe quel train.
Vous avez annoncé en mai dernier avoir réalisé une levée de fonds d’un montant de 3 M€. Quels étaient les objectifs de cette opération ?
Nous souhaitions tout d’abord pouvoir disposer d’un fonds de roulement nous permettant de lancer nos essais. Les environnements que nous visons, tels que l’aéronautique, impliquent en effet pour nous d’investir dans des ateliers spécifiques et de nouer des partenariats avec des sous-traitants. Notre objectif est aussi de poursuivre la montée en échelle de notre technologie et d’atteindre prochainement un TRL de 7-8, afin de pouvoir lancer l’industrialisation de notre solution en collaboration avec les quelque 25 clients européens – basés en France, en Allemagne et en Italie – qui nous font déjà confiance aujourd’hui. Pour certains cas d’usage très complexes, nous ne pouvons en effet pas avancer seuls. Notre objectif est de faire aboutir ces projets aux alentours de 2026-2027. Nous menons d’ailleurs aussi des discussions actuellement avec d’autres clients potentiels en Asie et aux États-Unis…
Nous allons toutefois aussi pouvoir nous lancer de manière autonome et proposer une première solution à destination des réservoirs d’hydrogène, avec un haut niveau de maturité. Il s’agit en effet d’un cas d’usage qui nous permet de nous lancer de manière indépendante, et dont les perspectives de développement se révèlent, en outre, en adéquation avec notre propre montée en maturité.

Enfin, cette levée de fonds avait aussi pour objectif de renforcer notre force commerciale ; elle nous a notamment permis de recruter un directeur commercial très expérimenté.
Ce cas d’usage précis du monitoring de réservoirs d’hydrogène que vous évoquiez se cantonne-t-il exclusivement à des réservoirs embarqués à bord de véhicules, ou pourrait-il également s’agir de réservoirs de stockage sur des installations de production ou de distribution ?
Nous visons tous types de réservoirs. Le monitoring est effectivement très demandé dans le cas des véhicules, mais nous avons aussi des demandes dans le domaine du stockage. Les cas d’usages sont cependant un peu différents : dans le cas du stockage, il s’agit plutôt de surveiller le « cyclage » des réservoirs, de monitorer leur vieillissement. Cela s’inscrit donc dans un temps plus long, avec une mesure moins fréquente, uniquement au moment du remplissage de ces réservoirs.
Quel modèle économique comptez-vous adopter pour commercialiser votre technologie et les différentes solutions qu’elle permettra de faire naître ?
Nous misons sur un modèle de licence technologique : nos clients seront complètement indépendants sur le plan de la fabrication de l’électronique, et pourront pour cela s’appuyer sur leurs propres fournisseurs et prestataires. Nous vendrons donc uniquement la possibilité d’utiliser notre technologie, mais aussi tout un ensemble de services d’accompagnement à la mise en place de la solution pour chaque cas d’usage. Cette approche permettra à nos clients d’être totalement indépendants de nous, ce qui, de mon point de vue, constitue un argument important pour une petite start-up telle que la nôtre, face, notamment, à des clients qui sont pour certains de très grands groupes.
En matière de coûts, où se situe votre approche par rapport à des technologies concurrentes actuellement disponibles sur le marché ? Quels seront, en outre, ses principaux avantages concurrentiels ?
Les principales technologies concurrentes à la nôtre sont des solutions basées sur l’utilisation de capteurs d’ondes sonores, de capteurs infrarouges, ou encore la tomographie par rayons X. Ces technologies restent encore assez chères, et nécessitent surtout, pour être mises en œuvre, d’extraire la pièce à monitorer. Ces technologies n’offrent, de plus, qu’une vision ponctuelle, à l’endroit où est positionné le capteur, là où notre technologie embarquée offre quant à elle une vision globale du matériau constitutif d’une pièce, tant en surface qu’en volume.
Une autre approche repose sur l’utilisation de fibre optique. L’inconvénient, outre sa fragilité, est que cette technologie n’offre qu’une vision binaire « on/off » en fonction de l’orientation de la fibre. Notre technologie permet quant à elle d’obtenir une véritable cartographie 3D et ce, pour un coût dix fois inférieur.
Enfin, notre technologie a aussi pour avantage de permettre d’établir un « passeport digital » d’une pièce, en la monitorant de sa fabrication à sa destruction, en passant par toutes les étapes de son cycle de vie.
Vous revendiquez pour l’heure l’usage de « modèles mathématiques », et non d’IA… Des algorithmes d’intelligence artificielle pourraient-ils toutefois, un jour, bénéficier à votre solution ?
L’IA est effectivement un champ de technologies très intéressant, susceptible de nous faire gagner beaucoup de temps. Le fait que nous visions le secteur industriel implique toutefois que nous respections des normes très strictes. Pour l’heure, il n’est pas possible de faire certifier un système de monitoring reposant sur des modèles d’IA, notamment pour des questions de transparence des algorithmes et d’explicabilité. Le jour où ce sera le cas, nous n’hésiterons pas, en tout cas, à franchir le pas !
[1] Touch Sensity
Réagissez à cet article
Vous avez déjà un compte ? Connectez-vous et retrouvez plus tard tous vos commentaires dans votre espace personnel.
Inscrivez-vous !
Vous n'avez pas encore de compte ?
CRÉER UN COMPTE