Créée fin 2020, Mecaware développe un procédé permettant d’extraire, de manière sélective, les métaux et terres rares issus des déchets technologiques. Moins polluante, moins chère et moins énergivore que les procédés actuels, cette solution pourrait bientôt bénéficier aux « giga-fabriques » de batteries pour véhicules électriques. Une unité de production industrielle devrait en effet voir le jour en 2024.
Depuis quelques mois, les annonces de création de gigafactories – ces « gigafabriques » de batteries inspirées du modèle initié par Tesla – se multiplient en France : à Douvrin (Pas-de-Calais) pour le groupe Stellantis, Douai (Nord) pour Renault, ou encore, plus récemment, à Dunkerque (Nord) pour Verkor, entreprise fondée en 2020 avec l’ambition d’atteindre, d’ici 2030, une capacité de production de 50 GWh.
Synonymes de décarbonation du marché automobile, ces grands projets de production de batteries ne vont toutefois pas sans poser un problème de taille, tant sur le plan écologique qu’économique : celui de l’extraction et du recyclage des matériaux nécessaires à la fabrication de ces batteries, métaux critiques en tête. Une start-up lyonnaise pourrait toutefois changer la donne.
Un procédé fruit de travaux de recherche antérieurs
Spin-off de l’Institut de chimie et biochimie moléculaires et supramoléculaires (ICBMS), Mecaware est l’acronyme de « metal capture for waste recycling ». Grâce à un procédé d’extraction innovant breveté, la jeune entreprise créée en décembre 2020 est en effet capable de récupérer, de manière sélective, écologique et économiquement viable, les métaux critiques, issus notamment des batteries lithium-ion usagées, ainsi que les terres rares contenues, par exemple, dans des aimants permanents ou les batteries Ni-MH équipant de nombreux véhicules hybrides. À l’origine de cette technologie de rupture : les travaux du professeur Julien Leclaire, enseignant-chercheur de l’Université Claude Bernard Lyon 1 à l’ICBMS et cofondateur de Mecaware. « La technologie est antérieure à la création de l’entreprise. Historiquement, nous nous sommes d’abord intéressés au captage du CO2 ; l’histoire a véritablement commencé en partenariat avec l’Institut français du pétrole [devenu en 2010 l’IFP Energies Nouvelles, NDLR], qui a sollicité des acteurs académiques pour le développement de solutions innovantes de captage de cette molécule », retrace Julien Leclaire.
Dès la fin des années 2000, le Professeur et son équipe ont alors travaillé autour de systèmes capables, en présence de dioxyde de carbone, de s’auto-assembler et de former des molécules inexistantes en son absence. « En étudiant ces molécules, nous nous sommes rendu compte que les objets formés possédaient de fortes affinités avec les métaux, notamment ceux que l’on retrouve fréquemment dans les dispositifs technologiques », poursuit le Pr. Leclaire. En 2012, le chercheur a alors soumis un projet à l’Agence nationale de la recherche (ANR) consistant à valoriser ces molécules formées lors du captage de CO2, afin de pouvoir les associer sélectivement avec des métaux, les séparer et les recycler.
2012, année charnière
« Cette année 2012 correspond à l’année où la Chine a restreint ses exports de terres rares, avec pour conséquence une flambée des prix », précise Julien Leclaire. Arrivé au moment opportun, le projet a alors été retenu, avec un financement public à la clé. « L’idée s’est révélée être la bonne. Nous avons alors déposé un premier brevet, puis rencontré des industriels spécialistes de la séparation des métaux », se remémore le chercheur lyonnais. Le début d’une aventure qui s’est poursuivie autour du développement de prototypes de procédés, avec un défi : celui d’une chimie triphasique, mêlant phases liquide, solide et gazeuse. « Nous nous sommes associés avec un laboratoire de génie des procédés et nous avons développé un procédé en flux continu, qui fonctionnait à l’échelle du laboratoire », ajoute Julien Leclaire.
Après le dépôt de deux premiers brevets portant sur le procédé, l’équipe de scientifiques a poursuivi son chemin avec une troisième patente, portant cette fois plus particulièrement sur la chimie. « Malgré ce portefeuille de brevets, nous nous sommes aperçus que les industriels restaient frileux vis-à-vis de l’acquisition de la technologie, considérée comme une technologie de rupture », relate le Pr. Leclaire.
Avec l’aide de l’incubateur spécialiste de la deep tech Pulsalys, Julien Leclaire s’est ainsi lancé dans l’aventure de la start-up aux côtés d’Arnaud Villers d’Arbouet, aujourd’hui président de l’entreprise. « Nous avons formé un binôme avec Arnaud afin d’associer progressivement des investisseurs, du personnel et créer la société », conclut le chercheur, qui cite également deux autres membres de l’aventure, co-inventeurs de la technologie : Claude de Bellefon, expert en génie des procédés et directeur scientifique de l’école d’ingénieurs CPE Lyon, et Frédéric Fotiadu, collaborateur de la première heure du Pr. Leclaire et actuel directeur de l’Institut national des sciences appliquées (Insa) de Lyon.
Un an après sa création, l’entreprise est ainsi parvenue à mettre en service un premier démonstrateur. « Nous avons un petit démonstrateur qui fonctionne, cela a été l’objectif de l’année dernière : il a été mis en service en novembre 2021 », indique Julien Leclaire. Une ligne pilote qui tient, pour l’heure, dans un atelier d’une soixantaine de mètres carrés, et qui met en œuvre le procédé particulièrement vertueux développé au fil des ans par le chercheur et ses collègues.
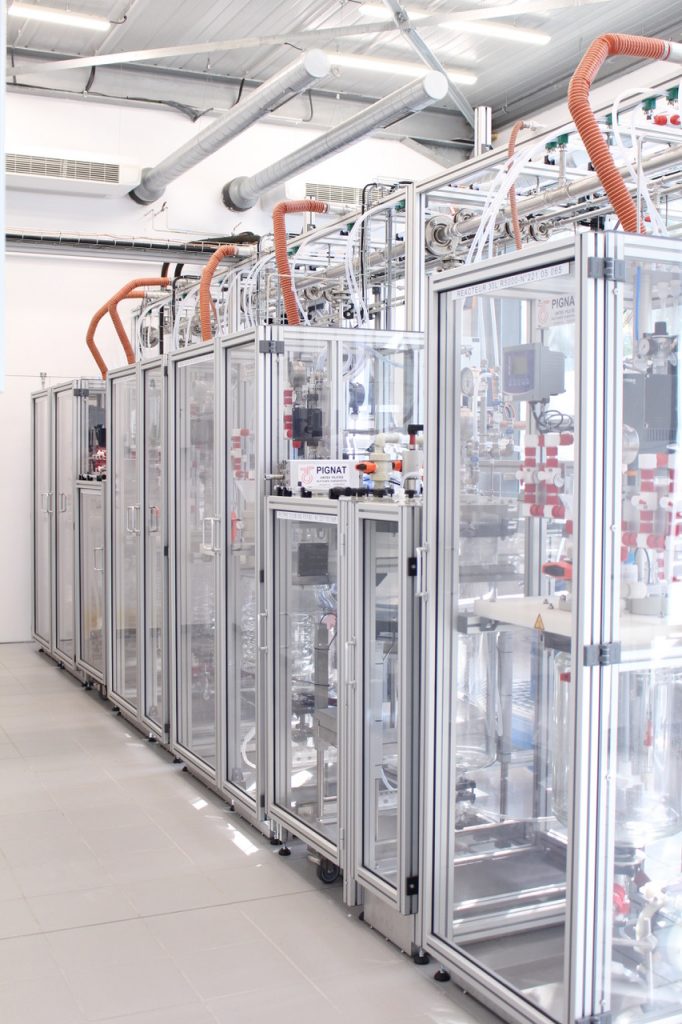
Une technologie de rupture
À la base de la technologie : le CO2, un ingrédient issu notamment de fumées de combustion, qui sont mises en contact avec des amines. « La mise en contact est réalisée dans des unités d’absorption qui existent au Texas ou en Arabie Saoudite et qui servent à capter du CO2 avant son enfouissement », explique le chercheur lyonnais. Ainsi mises en contact avec le dioxyde de carbone, les amines permettent de donner naissance à des molécules chargées électrostatiquement. Des charges qui permettent ensuite, lors de leur mise en contact avec un gisement solide ou liquide contenant des métaux, de provoquer leur association avec ces molécules.
« La particularité de la technologie est que, lors de la mise en contact des amines avec le CO2, se forme une collection de molécules en équilibre, ce qui signifie que l’on a affaire à un mélange “vivant” », souligne Julien Leclaire. La composition du mélange peut ainsi s’ajuster aux métaux avec lesquels il est mis en contact. Contrairement aux technologies conventionnelles, associant généralement un extractant à un métal donné, le mélange adaptatif que Mecaware est capable de former peut donc s’adapter aux spécificités du gisement de métaux à traiter. « C’est une grande force de la technologie. Nous proposons une solution à un verrou de la filière qui est la variabilité du gisement, due aux changements de composition des batteries », assure le Pr. Leclaire.
Une fois métal et extractant associés, reste alors à les séparer. Une opération habituellement réalisée en milieu très acide, ou au contraire à un pH très élevé. Pour Mecaware, la solution est tout autre : elle consiste à chauffer la solution à moins de 100°C, afin d’éliminer le CO2. « On a un interrupteur physique pour pouvoir restituer le métal et l’agent d’extraction, là où la filière utilise d’habitude des interrupteurs chimiques générateurs d’effluents, consommateurs d’acides et de bases, avec à la clé des conséquences importantes pour l’environnement », compare le chercheur.
Quant au devenir du CO2, deux options sont alors possibles : la formation de carbonates associés aux métaux, ou l’éjection de ce dioxyde de carbone sous la forme d’un flux gazeux pur qui peut ensuite être enfoui ou valorisé. Le métal est alors, dans ce cas, restitué sous forme métallique, et non pas sous forme de sel.
Un procédé aux multiples vertus
Outre une génération d’effluents largement inférieure aux procédés conventionnels d’hydrométallurgie, la technologie développée par Mecaware se révèle très largement moins énergivore et émettrice de gaz à effet de serre. Elle est aussi 30 à 50 % moins chère, le tout avec un très haut niveau de pureté. Autant d’avantages qui permettent à l’entreprise d’envisager sa mise en œuvre à l’échelle industrielle très prochainement.
« Le démarrage d’une première ligne industrielle devrait avoir lieu fin 2024 », prévoit en effet le président de Mecaware, Arnaud Villers d’Arbouet ; une installation destinée à la production en flux continu de 5 000 à 10 000 tonnes de métaux par an. « Nous avons plusieurs pistes de site en discussion aujourd’hui », glisse Arnaud Villers d’Arbouet. Un site qui devrait occuper quelque dix mille mètres carrés, soit environ dix fois moins que la surface nécessaire aux usines mettant en œuvre les technologies actuelles d’hydro ou de pyrometallurgie.
D’autres applications en vue
Alors que les premières batteries fabriquées à partir de ces métaux recyclés pourraient équiper des véhicules dès 2025, la start-up planche également aujourd’hui sur d’autres applications de sa technologie. « Nous avons conclu un partenariat avec un industriel du ciment, qui nous a confié des terres polluées aux métaux. Dans ce cas, le procédé permet de fixer le CO2 dans la terre et d’en lixivier les métaux contaminants, ce qui fait que l’on a une terre décontaminée qui peut retourner dans le cycle de production de granulats. Ceci avec un double service : fabriquer du ciment avec une matière première recyclée, et décontaminer le sol », explique Julien Leclaire, qui indique également avoir envisagé le traitement de gisements d’aimants permanents, pour en extraire les terres rares. « Cela fonctionne mais les performances ne permettent pas encore d’envisager l’industrialisation », constate le chercheur.
Autre perspective pour Mecaware : étendre l’utilisation de son procédé à des ressources primaires ; autrement dit : le mettre en œuvre afin d’extraire des métaux directement à partir de minerais. « Actuellement, les techniques qui permettent de le faire ont de lourdes conséquences au niveau environnemental, notamment les opérations d’injection d’acide sulfurique dans le sous-sol qui sont réalisées », souligne en effet le chercheur. Avant d’en arriver là, ce sont avant tout les futures gigafactories qui pourraient bien bénéficier de la technologie de rupture proposée par Mecaware.
Bonjour,
Merci pour votre remarque. Il y a bien certaines batteries qui contiennent des terres rares : les batteries Ni-Mh.
Bonne journée,
Techniques de l’Ingénieur
Bravo ! Une technologie de rupture impressionne toujours, elle prend du temps pour se déployer mais celle-ci a l’air bien partie !
AllEnvi Solutions a établi un panorama des technologies (concurrentes) développées aussi par la recherche française en 2016 ; pour en savoir plus : https://allenvi-solutions.fr/thematique/recyclage-des-metaux-critiques/
Combien de fois faudra-t-il répéter qu’il n’y a pas de terres rares dans les batterie ?
Réagissez à cet article
Vous avez déjà un compte ? Connectez-vous et retrouvez plus tard tous vos commentaires dans votre espace personnel.
Inscrivez-vous !
Vous n'avez pas encore de compte ?
CRÉER UN COMPTE