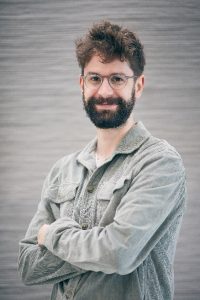
XtreeE a été créée en décembre 2015, suite à un projet de recherche avec l’école d’architecture de Paris-Malaquais.
Ce précurseur de l’impression 3D grande échelle développe et déploie des systèmes industriels d’impression 3D pour la construction à travers le monde.
Romain Duballet en est cofondateur et Directeur Exécutif Produit.
Il est également Directeur du Master Spécialisé Digital Building Design à l’École des Ponts ParisTech.
Techniques de l’ingénieur : Dans un communiqué de presse[1], vous évoquez un partenariat d’innovation concernant l’utilisation de fibres dans le béton. De quoi s’agit-il ?
Romain Duballet : Nous travaillons en effet au développement d’un nouveau type de matériau renforcé par des fibres longues, en partenariat avec le CNRS et l’École des Ponts ParisTech. Les essais sont actuellement menés au sein du Laboratoire Navier (CNRS/École des Ponts ParisTech/Université Gustave Eiffel). L’étude fait l’objet d’une thèse[2] co-financée par XtreeE et le CNRS ; elle est dirigée par Jean-François Caron, Directeur de Recherche à l’École des Ponts ParisTech.
Plus qu’un matériau, il s’agit en fait d’un nouveau procédé : la coextrusion d’un matériau à matrice cimentaire et de fibres. Pour obtenir un béton renforcé par des fibres longues, nous déroulons une bobine contenant des fibres lors de l’impression. Ces fibres peuvent être de natures diverses, mais doivent respecter un certain cahier des charges pour atteindre la résistance souhaitée.
Parmi la multitude de matériaux testés (carbone, basalte, verre, acier…), les fibres de carbone semblent être la solution la plus viable et la plus rapide à industrialiser, car c’est le matériau le plus avancé en termes de normalisation et de reconnaissance.
Le béton composite fibre de carbone obtenu est anisotrope. Il possède une résistance à la traction et une durabilité intrinsèques, sans qu’il y ait besoin de le combiner à d’autres matériaux comme l’acier. Car il faut savoir que le problème numéro 1 de la durabilité des bétons est lié à la corrosion des aciers, elle-même causée par la carbonatation du béton[3]. Le fait de ne plus utiliser d’armatures en acier évite donc tout problème de corrosion.
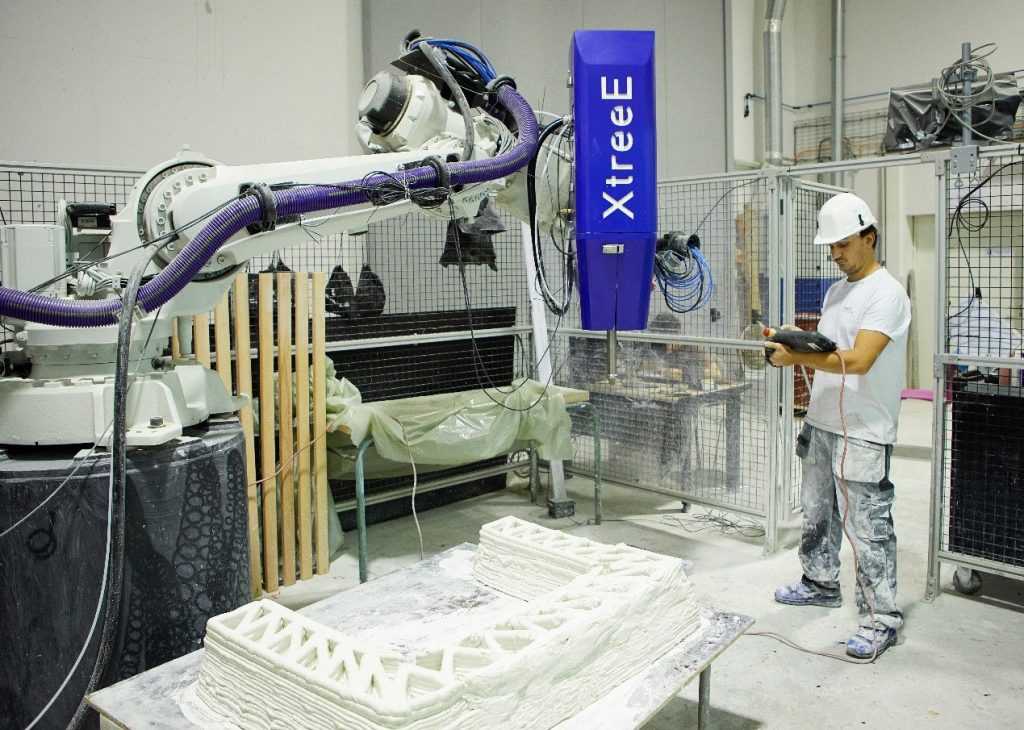
Que permet de faire l’impression de béton fibré ?
L’utilisation de fibres longues permet d’imprimer des pièces que nous ne pouvions obtenir jusqu’ici, de multiplier le panel de formes possibles et donc d’accéder à d’autres marchés.
Comme le mortier est frais lors de l’impression, la difficulté est d’arriver à imprimer sans que la structure s’effondre avant la prise. Le fait d’ajouter des fibres renforce la résistance à l’état frais et multiplie donc les possibilités en termes de formes.
D’autre part, comme le fibrage augmente la résistance à la traction, il devient également possible d’imprimer des coques fines qui sont structurelles en elles-mêmes.
C’est donc une nouvelle manière de concevoir des bétons qui vient en complément de nos activités actuelles, mais qui n’est pas destinée à les remplacer.
Quelles sont ces autres activités ?
XtreeE propose une technologie d’impression 3D grande échelle. Si le procédé en lui-même est multimatériaux, jusqu’à présent, nous avons essentiellement concentré nos efforts sur les matériaux du type béton et mortiers. Des bétons haute performance au départ, nous avons progressivement étendu le champ de nos recherches à d’autres compositions, notamment les bétons bas carbone.
L’une des applications de la technologie d’impression est ce qu’on appelle le coffrage perdu, une méthode qui consiste à imprimer une peau fine en béton qui sera ensuite remplie par un autre matériau, par exemple un béton obtenu par coulage traditionnel. Il faut savoir que lorsqu’on a besoin d’un produit massif, il n’est pas du tout intéressant, en termes de coût et de temps, de le produire intégralement par impression.
Cette application de coffrage perdu est dorénavant passée au stade de l’industrialisation, puisque des usines de préfabrication sont déjà opérationnelles en France. C’est notamment le cas de Spie Batignolles, qui est équipé de deux machines XtreeE et alimente ses chantiers en coffrages perdus imprimés. Les réalisations sont d’envergure : coffrages de poteaux pour la Piscine d’Aubervilliers et coffrages de linteaux pour la réhabilitation de la résidence Schuman à Poitiers, par exemple.
Vous avez évoqué les bétons bas carbone. Dans quelle mesure la technologie d’impression XtreeE permet-elle de réduire l’impact CO2 des ouvrages ?
Premièrement, nos machines permettent non seulement de travailler avec des matériaux à faible impact environnemental mais aussi de créer des structures allégées. Un troisième axe très important de réduction des impacts est la localisation des ressources. En ce sens nous travaillons à développer des matériaux imprimables à partir de matières premières sourcées localement. Par ailleurs, il faut savoir que la mise en œuvre avec les méthodes traditionnelles de bétons bas carbone pose beaucoup de problèmes techniques. Nos machines, de leur côté, permettent un contrôle inédit du pompage, de l’adjuvantation et de la prise, ce qui en fait des outils particulièrement aptes à travailler avec ces matériaux innovants.
En ce qui concerne le fibrage, le fait de renforcer les bétons avec des fibres de carbone évite les problèmes de corrosion des aciers et autorise donc à terme de réduire considérablement les quantités de clinker dans les mortiers.
On se dirige donc petit à petit vers l’obtention d’un matériau fibré bas carbone, même si nos efforts sont pour le moment essentiellement concentrés sur la robustesse du procédé, car l’industrialisation de la solution « fibres longues » est prévue pour 2024 !
[1] Disponible à cette adresse
[2] Dans la continuité des travaux réalisés dans le cadre de deux autres thèses concernant le renfort par fibres
[3] La capture naturelle du CO2 avec le temps
Crédit image de une : XtreeE – Charlène Yves
Cet article se trouve dans le dossier :
Matériaux : comment penser l'innovation ?
- Écoutez notre podcast Cogitons Sciences : Guide pour bien choisir ses matériaux [Matériaux, histoire d’une vie #2]
- Quand la recherche fait appel à l’IA pour élaborer de nouveaux matériaux
- Ecoutez notre podcast Cogitons Sciences : Matériaux, durée de vie et fatigue [Matériaux, histoire d’une vie #3]
- Quels matériaux pour les batteries du futur ?
- Écoutez notre podcast Cogitons Sciences : Une industrie accro aux minerais de conflit [Matériaux, histoire d'une vie #1]
- Quels matériaux composent nos smartphones ?
- Le tantale, un élément exceptionnel mais controversé
- Quels matériaux pour l'impression composite 3D ?
- « Valoriser la liberté de conception offerte par la fabrication additive »
- « La fabrication additive sert sur plusieurs étapes des projets »
- « Différents secteurs industriels se mettent petit à petit à la fabrication additive »
- Un hydrogel photosensible imprimable en 3D à l'étude
- Reformer les récifs coralliens en utilisant l’impression 3D
- La production industrielle d'hydrogène vert a besoin de nouveaux matériaux
- Un nouveau matériau pour la production d'hydrogène vert à grande échelle
- Quels matériaux pour un stockage de l'hydrogène plus performant et accessible ?
- « Il faut adapter les matériaux pour des usages à température ambiante » pour stocker l'hydrogène
- Le béton : un matériau technologique faisant l'objet d'une intense R&D
- Trois alternatives durables au béton
- Le végétal dans la construction en forte augmentation ces dernières années
- Ciment sans clinker : la solution d’avenir ?
- XtreeE développe l’impression 3D béton renforcée par des fibres longues
- Produire en France une fibre de carbone économique et biosourcée
- Des composés à base de nitrure de carbone pouvant rivaliser avec les diamants
- Créer des matériaux de la transition à partir de liqueurs noires
- Réduire les coûts d'utilisation des matériaux composites dans le secteur naval
- De nombreuses solutions offertes aux industriels pour remplacer les phtalates
Dans l'actualité
- Un supercondensateur à base de ciment, d’eau et de carbone pour stocker l’électricité dans les structures en béton
- Relocaliser et réparer grâce à l’impression 3D
- 3Deus Dynamics : l’impression 3D sans limites
- Ciment sans clinker : la solution d’avenir ?
- Améliorer la modélisation des matériaux quasi-fragiles grâce à l’étude du papier
- EcoTechnilin : des solutions à base de fibres naturelles au service de l’industrie
- Le verre recyclé : de multiples applications en fabrication additive
- Des composites cimentaires construits selon l’arrangement brique-et-mortier de la nacre
- Béton de bois : Spurgin Leonhart inaugure une usine entièrement dédiée à ce matériau vertueux
- 10 articles à lire à l’occasion de la Semaine de l’industrie 2024