Inventés dans les années 1960, les métaux amorphes présentent une structure atomique modifiée, leur permettant d’acquérir des propriétés bien spécifiques. Aujourd’hui, ils sont principalement utilisés pour fabriquer de fines bandelettes (rubans) possédant des propriétés magnétiques et que l’on retrouve dans des transformateurs électriques. Fondée en 2017, la start-up Vulkam a développé une technologie pour concevoir des petites pièces en métaux amorphes. Son procédé est le fruit de plus de 30 ans de recherche sur les alliages métalliques amorphes au sein du laboratoire SIMAP (Science et Ingénierie de Matériaux et Procédés) à Grenoble. Après avoir travaillé 15 ans dans ce laboratoire, Sébastien Gravier a cofondé Vulkam. Il en est aujourd’hui le président et il nous présente le procédé développé par son entreprise, ses applications et ses perspectives.
Techniques de l’Ingénieur : Décrivez-nous ce que sont les métaux amorphes et quels sont leurs principaux intérêts ?
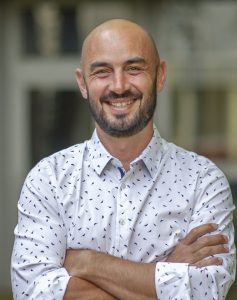
Sébastien Gravier : Ce sont des alliages métalliques qui possèdent une structure atomique désorganisée, à l’inverse de tous les métaux industriels, dont la structure est cristalline avec des atomes positionnés de manière organisée et structurée. Ce positionnement aléatoire des atomes présente deux intérêts. Sur le plan des procédés de fabrication, la structure amorphe permet de mouler des pièces dont la géométrie peut être très complexe, et avec une très grande précision. Lorsque l’on sort les pièces du moule, elles sont totalement terminées et sont utilisables directement, ce qui n’est pas le cas avec le moulage traditionnel des métaux. Ensuite, les propriétés mécaniques de ces métaux amorphes sont multipliées par deux ou trois comparées aux métaux traditionnels, que ce soit sur le plan de la résistance pure, de la capacité de déformation et de l’élasticité, de la dureté,… Les propriétés physiques et chimiques se trouvent également fortement impactées par cette nouvelle structure atomique.
Quel est le savoir-faire développé par Vulkam autour des métaux amorphes ?
Sur le plan scientifique, nous développons et optimisons une large gamme de métaux amorphes ; chacune ayant des propriétés bien spécifiques qui répondent aux demandes de nos clients.
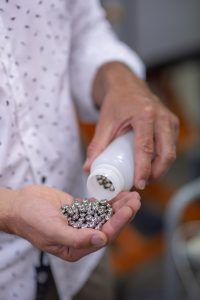
Nous avons développé une première machine capable de fabriquer l’alliage primaire qui se présente sous la forme de petites billes. Dans cette machine, les différents métaux utilisés sont montés en température, jusqu’à la fusion, et mélangés dans un environnement ultra-propre. Nous utilisons des alliages à base de niobium, de zirconium, de cuivre, de nickel, de palladium… Chacun représente l’élément principal auquel nous ajoutons quatre ou cinq constituants supplémentaires, en fonction des propriétés recherchées par nos clients, mais je ne peux pas vous dévoiler la recette exacte.
Les pièces finales sont fabriquées à l’aide d’une seconde machine de thermomoulage qui fonctionne intégralement sous vide secondaire. Ce dernier permet de limiter les défauts dans la matière étant donné que l’oxygène est présent en très petite quantité. Nous fabriquons ainsi des pièces de très bonne qualité, sans perte de matière, ce qui est très important, indépendamment de l’aspect économique, pour la sauvegarde des ressources naturelles. Les billes sont fondues à environ 1 000 degrés puis sont injectées dans un moule métallique. La structure amorphe est obtenue grâce au refroidissement par le contact du métal liquide avec le moule métallique. Le passage rapide de l’état liquide à l’état solide se déroule à une vitesse d’environ 100 degrés par seconde, et permet aux atomes de ne pas s’organiser. Les caractéristiques des métaux amorphes permettent d’obtenir directement des pièces finies et de haute précision sans traitement ultérieur.
Quelles sont les applications de votre technologie ?
Dans l’horlogerie, nous avons développé une gamme de matériaux qui servent à fabriquer l’habillage de montres. Ces matériaux sont trois fois plus résistants à la rayure que les aciers inoxydables actuels, et plus résistants à la corrosion. Nous fabriquons également des pièces de mouvement horloger extrêmement petites, puisqu’elles ne mesurent que quelques millimètres de diamètre et dixièmes de millimètre d’épaisseur. En sortie de moule, nous parvenons à obtenir une précision de plus ou moins trois microns. Elles sont trois fois plus résistantes à l’usure liée aux frottements et aux aspects de tribologie ainsi que deux fois plus flexibles, dans le cas de mécanismes déformables.
Dans le domaine médical, nous fabriquons entre autres des pinces utilisées pour la chirurgie optique. Ici, l’un des intérêts se situe au niveau de notre procédé de fabrication. Actuellement, ces pièces sont fabriquées en Asie, car elles nécessitent de nombreuses étapes manuelles. Le fait d’être capable de sortir ces pièces directement du moule, permet de réduire le coût de la main-d’œuvre et d’être suffisamment compétitif pour relocaliser leur fabrication en Europe.
Dans le spatial, plusieurs applications sont en cours de développement, et l’une d’elles concerne la cryogénie. Nous développons un matériau ultra-isolant sur le plan thermique, capable de limiter les pertes de froid, et donc de limiter les besoins énergétiques et la taille des systèmes de refroidissement pour la gestion des basses températures. Nous gagnons un facteur 4 sur cet aspect isolant.
À quel stade se trouve le développement de votre projet ?
Nous travaillons déjà avec de nombreux clients. Dans le domaine de l’horlogerie par exemple, nous collaborons avec environ 80 % des horlogers présents dans le monde. Mais pour l’instant, nous fabriquons uniquement des pré-séries et des prototypes de quelques dizaines à quelques centaines de pièces. Nous sommes dans une phase d’industrialisation et avons lancé une campagne de levée de fonds, pour nous permettre de construire notre usine et produire de gros volumes. Elle devrait être opérationnelle en fin d’année 2024, et notre première ligne de production devrait arriver à saturation en 2025 et produire plus d’un million de pièces par an. En 2026, nous devrions entamer la parallélisation de cette ligne de production afin d’augmenter les volumes, grâce à une extension de notre bâtiment déjà programmée. Notre entreprise compte environ 25 personnes, et nous comptons doubler nos effectifs d’ici 2025, puis atteindre rapidement 100 personnes.
Il existe dans le monde quatre ou cinq start-up qui travaillent à la conception de pièces en métaux amorphes. Nous faisons partie de celles qui sont les plus avancées dans la maîtrise de cette technologie, car nous sommes capables d’utiliser une large gamme de matières premières afin d’optimiser les propriétés des pièces recherchées par les clients. Les autres entreprises ont tendance à se restreindre à une gamme limitée de matériaux. Cet avantage est lié à notre process de fabrication que nous avons breveté.
Dans l'actualité
- Des impulsions laser pour traiter des matériaux contaminés au tritium
- « Le recyclage des matériaux constituant les batteries est un enjeu immédiat »
- Quels matériaux pour les batteries du futur ?
- « Il faut adapter les matériaux pour des usages à température ambiante » pour stocker l’hydrogène
- Un nouveau matériau pour la production d’hydrogène vert à grande échelle
- Les ressources en matériaux, talon d’Achille de l’Europe des batteries ?