40 tonnes. C’est, d’après l’ADEME, la quantité de CO2 émise par la production d’une tonne de fibre de carbone vierge. Un matériau synthétique à la base de composites – les polymères renforcés de fibres de carbone, ou PRFC – très appréciés des secteurs aéronautique, automobile ou encore éolien pour leur légèreté et leur résistance mécanique. Si bien que la demande mondiale de fibres ne cesse de croître : passant de 33 à 95,5 kilotonnes par an entre 2010 et 2020, elle devrait atteindre un pic estimé à 117 kilotonnes en 2022, selon l’étude de marché publiée chaque année par la Fédération allemande des plastiques renforcés (AVK). La demande de PRFC devrait ainsi suivre la même tendance et culminer à 199 kilotonnes l’an prochain.
Outre l’empreinte carbone liée à la production de ces matériaux composites, la question de leur recyclabilité se pose ainsi. On estime en effet à 20 kilotonnes la quantité de déchets issus de PRFC qui sera produite chaque année à l’horizon 2025. « Il existe des voies de recyclages de ces composites : la pyrolyse notamment, ou encore une technique adaptée aux thermoplastiques qui consiste, schématiquement, à les broyer puis à les refondre », expose ainsi Frédéric Goettmann, co-fondateur et Président d’Extracthive, PME française créée en 2015 et spécialisée dans le recyclage de déchets industriels. Des approches qui ne sont cependant pas exemptes de défauts : empreinte carbone élevée, coût, ou encore dégradation des fibres au cours du processus de recyclage. Grâce à une autre approche, basée sur la solvolyse, Extracthive entend toutefois pallier ces inconvénients.
PHYre®, un procédé de recyclage plus propre et qui ne dégrade pas les fibres
Baptisée PHYre®, cette technologie développée depuis 2016 et aujourd’hui brevetée repose sur un principe de base comparable à celui… d’un autocuiseur ! « On met les composites à recycler dans un panier, on place un mélange de solvants et de catalyseurs en dessous, et ce sont les vapeurs de ces substances portées à 175°C qui font le travail », décrit Frédéric Goettmann.
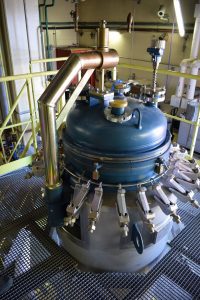
Le procédé permet ainsi de récupérer des fibres de carbone dont les propriétés mécaniques sont équivalentes à celles de fibres vierges, comme le souligne le co-fondateur de la PME : « PHYre® permet de conserver des fibres les plus longues possibles, ce qui autorise des mises en œuvre dans des applications de niche, à haute valeur ajoutée. Et, d’autre part, cela permet d’abîmer le moins possible la surface de la fibre, parce que l’on sait que cette surface est déterminante dans les propriétés mécaniques de la fibre et donc du composite ».
Permettant de travailler à des températures moins élevées que des techniques comme la pyrolyse ou la vapo-thermolyse, la solvolyse se révèle d’autant plus avantageuse que les solvants sont réutilisés tout au long de la réaction : leurs vapeurs sont recondensées, et le liquide formé coule de nouveau sur le composite à dégrader, emportant avec lui les résines. « Cela permet, en plus d’une meilleure efficacité du procédé, de limiter les quantités de solvants mis en œuvre. Notre objectif est de dépasser les 90 % de réutilisation de solvants », explique Frédéric Goettmann. « Cela fonctionne en laboratoire, mais il reste à le vérifier à grande échelle », ajoute le Président d’Extracthive, qui indique également travailler à des solutions de recyclage des résidus de résines éliminées.
Un démonstrateur industriel en préparation
Alors qu’elle vient de finaliser une levée de fonds de 4,6 M€, l’entreprise a désormais pour objectif de construire et de mettre en service d’ici début 2023 un démonstrateur industriel d’une capacité de 500 à 700 kg de composite par essai, contre une cinquantaine de kilos pour le dispositif pilote dont elle dispose pour l’heure. « Si l’on parvenait à faire tourner cette unité en continu, on pourrait aller jusqu’à traiter 450 tonnes de composites par an », estime Frédéric Goettmann.
À terme, l’entreprise prévoit de doubler cette capacité en créant des unités industrielles composées de deux réacteurs identiques partageant une « colonne vertébrale » commune dédiée à la réception des acides, aux équipements de sécurité et à la régénération des solvants. « L’idée serait d’avoir une unité de référence qui traiterait environ 900 tonnes de composites par an, et de multiplier ensuite ce type d’unité à différents endroits en Europe et dans le monde », entrevoit Frédéric Goettmann. Une approche qui permettrait en effet de traiter les composites localement, réduisant ainsi les coûts et les conséquences environnementales du transport de ces matières peu denses. « Nous avons déjà des lettres d’intention de la part d’entreprises concernant le recyclage de 1 600 tonnes par an de chutes de fabrication », dévoile finalement le Président d’Extracthive. Une perspective tout à fait concrète pour l’entreprise, qui envisage également de se lancer dans le recyclage de déchets industriels contenant du lithium – projet pour lequel Extracthive a déjà développé un pilote – ou encore du zinc, grâce à un procédé dont le brevet est en cours. « On n’a pas un profil de start-up classique, au sens “une société – une techno”. Nous voulons rester assez “couteau suisse” », conclut le co-fondateur d’Extracthive.
Benoît Crépin
Dans l'actualité
- Un nouveau matériau composite thermoplastique pour renforcer les bétons
- Une membrane nanocomposite capable d’éliminer la pollution aux phosphates
- Récupérer les fibres de carbone des matériaux composites grâce aux puissances pulsées
- Recycler les fibres de carbone des matériaux composites
- Les initiatives industrielles en matière de recyclage chimique des plastiques se multiplient
- STRAP : un nouveau procédé de recyclage des polymères multicouches
- Une nouvelle filière de matériaux thermoplastiques en développement
- Une chaussure de football entièrement recyclable et composée de matière recyclée
- Cycl-Add produit des matières plastiques à partir de déchets considérés comme non recyclables
- L’art pour comprendre le vieillissement des écomatériaux
- Le Falcon 10X, un jet d’affaires « augmenté »
- Un procédé de recyclage chimique rapide des polycarbonates et polyesters
- Recyclage chimique des plastiques : une filière mondiale en phase de test
- Interview DEMETA : un Poly-DCPD sans odeur pour l’industrie automobile
- Une norme internationale pour encadrer l’intégration des données environnementales dans le BIM
- Quels matériaux pour l’impression composite 3D ?
- Le recyclage des VHU bouleversé par la loi AGEC ?
- Que devient un véhicule hors d’usage ?