La start-up Ananké a décidé de développer la technologie du moteur Ericsson pour récupérer les pertes thermiques sur des sites industriels. Ce procédé permet, entre autres, de produire de l'air comprimé ou de l'électricité. Entretien avec Thibaut Cartigny, directeur et cofondateur de l'entreprise.
Son invention date de la première moitié du XIX siècle et est attribuée à John Ericsson, un ingénieur mécanicien américain d’origine suédoise. Le MACE (Moteur à apport de chaleur externe), également appelé moteur à air chaud, fonctionne à partir d’une source de chaleur externe au moteur par l’intermédiaire d’un échangeur. Au fil du temps, ce procédé a plus ou moins été abandonné au profit du moteur à combustion interne. C’était sans compter Ananké, une start-up installée à Belfort, qui a décidé de reprendre le développement de cette technologie. Son objectif : valoriser la chaleur fatale rejetée sur des sites industriels. Après plusieurs années de recherche et développement, l’entreprise est sur le point d’installer son premier démonstrateur industriel. Rencontre avec Thibaut Cartigny, le directeur et le cofondateur d’Ananké.
Techniques de l’Ingénieur : Comment fonctionne votre technologie pour récupérer la chaleur rejetée sur des sites industriels ?
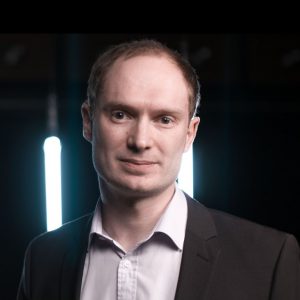
Thibaut Cartigny : Nous avons remis au goût du jour une vieille technologie, celle du moteur Ericsson qui fonctionne avec de l’air, raccordé à une source de chaleur externe au moteur. Concrètement, il s’agit d’un cycle ouvert où l’on va admettre de l’air ambiant dans une enceinte de compression. Il est ensuite comprimé puis envoyé dans un échangeur thermique raccordé aux cheminées d’un site industriel. L’air comprimé va alors se réchauffer puis est envoyé dans un espace de détente qui va permettre de transformer cette énergie thermique en énergie mécanique. Une partie de celle-ci va être réutilisée afin d’entraîner le compresseur, car celui-ci consomme de l’énergie, tandis que l’énergie résiduelle va servir à produire de l’air comprimé supplémentaire ou alors de l’électricité grâce à un alternateur.
Quels ont été les axes de recherche et de développement de ce procédé ?
Le MACE est un procédé relativement simple, auquel nous avons apporté plusieurs développements en nous inspirant des dernières avancées technologiques du secteur automobile. Ainsi, nous avons mis en place un contrôle en temps réel du fonctionnement de la machine, qui correspond au cerveau de ce moteur. Ensuite, sur la partie distribution, nous avons énormément travaillé sur l’ouverture et la fermeture des enceintes de compression et de détente. Mais notre procédé est différent de celui rencontré sur les voitures qui fonctionnent avec des soupapes. Nous avons développé notre propre procédé et l’avons breveté.
Quel est l’avantage de votre technologie ?
Comparé à d’autres technologies déjà présentes sur le marché, notre procédé est particulièrement adapté pour valoriser la chaleur fatale [aussi dite chaleur de récupération, c’est la chaleur générée par un procédé industriel, et qui n’en est pas la première finalité, NDLR] sur des sites industriels de petite taille ; nous ciblons ceux qui rejettent moins de 1 MW (mégawatt) de chaleur par an. Seule condition : la température des fumées doit être supérieure à 450 degrés. Afin que nos clients aient un temps de retour sur investissement rapide, nous avons développé une machine de puissance standard de 40 kW (kilowatt). Et pour l’alimenter, une énergie thermique disponible d’au minimum 200 kW est nécessaire. Bien sûr, il est possible d’installer plusieurs modules de 40 kW sur un site si les rejets sont supérieurs. Notre technologie est d’autant plus intéressante que les petits sites industriels paient leur électricité à un tarif plus élevé que ceux de plus grande taille.
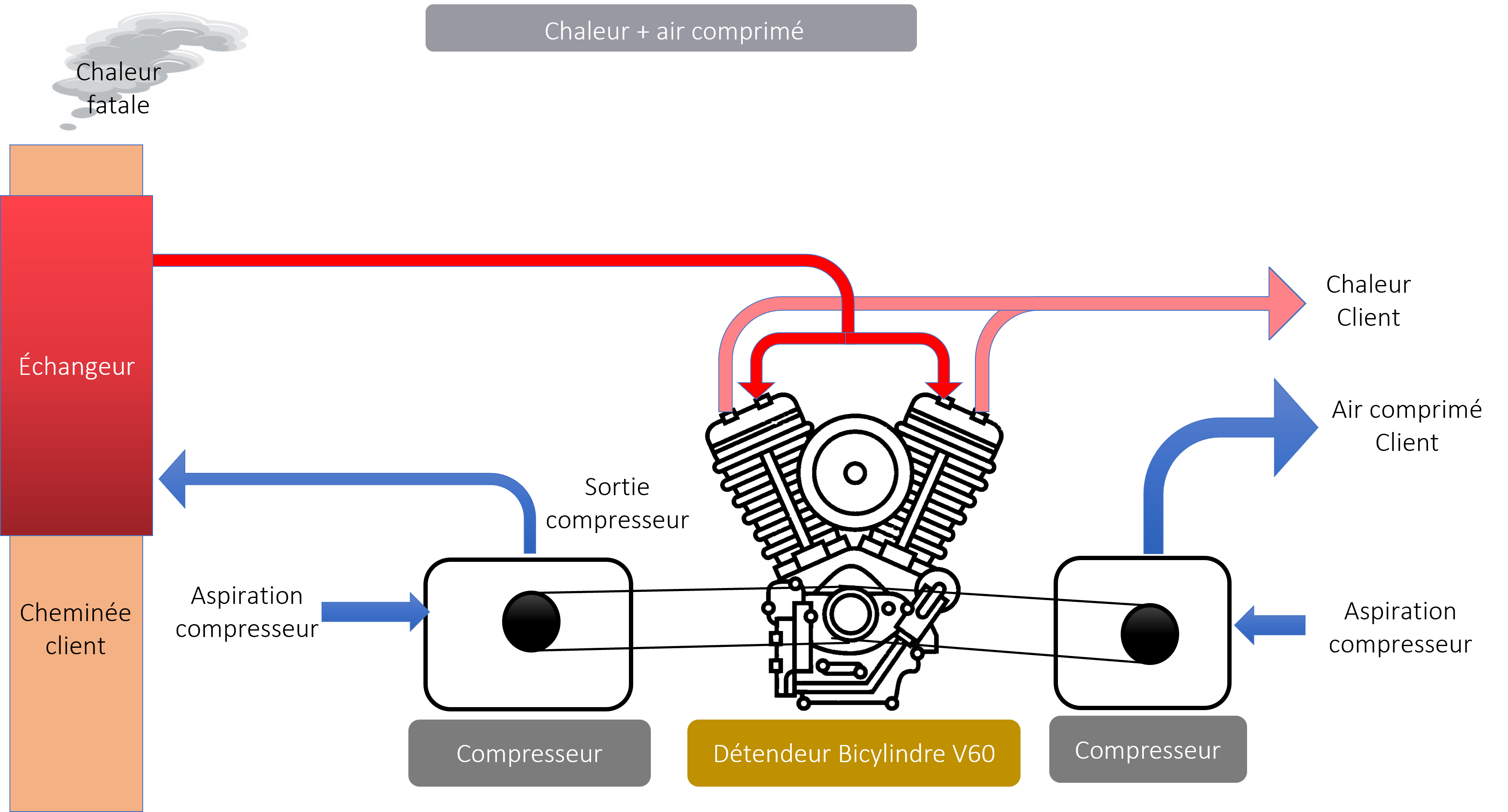
Nous avons également développé un outil capable de mesurer en temps réel les fumées rejetées, car un grand nombre d’industriels ont une méconnaissance des quantités disponibles. Nous sommes ainsi capables de savoir si nous pouvons les valoriser grâce à notre technologie.
Quel est le rendement de votre moteur ?
Il est compris entre 10 % lorsque les températures s’élèvent à 450 degrés et peut grimper jusqu’à 28 % lorsqu’elles dépassent 700 degrés. En plus de cette énergie mécanique disponible, notre procédé produit aussi de l’énergie thermique utile sous la forme d’air propre et chaud, car il s’agit d’une cogénération. Cet air chaud représente 2 à 3 fois la quantité d’énergie mécanique disponible et peut être valorisé de différentes façons par nos clients. Par exemple, pour assurer les besoins en chauffage des bâtiments, de séchage de process industriels, ou alors être renvoyé à l’entrée d’un four afin que l’air soit plus chaud à l’intérieur et ainsi réduire les quantités de gaz consommés pour faire des économies.
À quel stade de développement se trouve votre technologie ?
Nous avons développé cinq prototypes au sein du laboratoire FEMTO-ST à Belfort dans lequel notre entreprise est installée. En début d’année prochaine, nous allons mettre en service un premier démonstrateur industriel sur le site de Cristel, à Fesches-le-Châtel. Cette entreprise fabrique des ustensiles de cuisine de luxe, et fournit notamment l’émission culinaire Top Chef sur M6. Cristel possède un four de traitement thermique afin de poser des revêtements de surface sur du matériel de cuisine, comme des casseroles. En sortie de ce four, de la chaleur fatale est disponible à une température de l’ordre de 500 degrés. Grâce à notre procédé, nous allons pouvoir la récupérer afin de produire de l’air comprimé qui sera réutilisé par l’entreprise pour ses process.
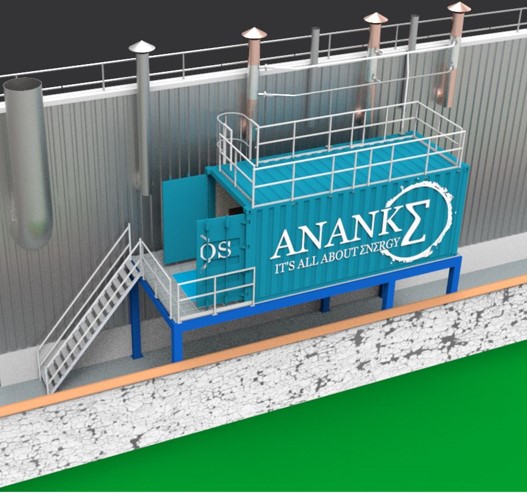
Nous avons rencontré de nombreux clients et une majorité d’entre eux ont d’importants besoins en air comprimé. Il est donc plus intéressant de produire directement de l’air comprimé avec notre technologie plutôt que de l’électricité qui viendra ensuite alimenter un compresseur. D’autant plus que ce besoin en air comprimé correspond au moment où la chaleur est disponible et valorisable. Il y a ainsi une parfaite adéquation entre sa production et son utilisation, sans besoin de stockage. Notre objectif pour l’année 2022 est donc de rentrer dans une phase de préindustrialisation, en vue d’une commercialisation de notre procédé en 2023.
Réagissez à cet article
Vous avez déjà un compte ? Connectez-vous et retrouvez plus tard tous vos commentaires dans votre espace personnel.
Inscrivez-vous !
Vous n'avez pas encore de compte ?
CRÉER UN COMPTE