Issue de travaux de deux laboratoires de recherche, la start-up Cilkoa développe un procédé consistant à déposer une couche nanométrique de céramique sur une feuille de cellulose. Le nouveau matériau obtenu possède des propriétés barrières similaires à celles des plastiques, tout en étant totalement biodégradable et recyclable. Rencontre avec les cofondateurs de l'entreprise.
Emballages, bouteilles, étiquettes… les plastiques à usage unique sont très présents dans notre quotidien. Ils sont pointés du doigt en raison de leur effet néfaste sur l’environnement, car ils ne se désagrègent pas après usage, mais se décomposent en microparticules que l’on retrouve un peu partout, notamment les océans. Réduire ces déchets est donc un enjeu environnemental majeur. À Grenoble, des chercheurs ont développé un matériau qui présente la flexibilité et la biodégradabilité du papier, tout en possédant les propriétés barrières du plastique, c’est-à-dire qu’il résiste à l’eau et est imperméable aux gaz. Leur recette ? Ils ont déposé une couche nanométrique de céramique sur une feuille de cellulose. Ce procédé est le fruit du travail de recherche de deux laboratoires, qui ont su combiner leur expertise, chacun dans leur domaine : le SIMAP (Science et ingénierie des matériaux et procédés) spécialisé dans les matériaux céramiques, et le LGP2 (laboratoire Génie des procédés papetiers) qui, comme son nom l’indique, est spécialisé dans le domaine papetier. Une start-up vient d’être créée afin de valoriser cette nouvelle technologie. Entretien avec Frédéric Mercier et Erwan Gicquel, deux des quatre cofondateurs de Cilkoa. Le premier est aussi chercheur CNRS au SIMAP et le second, un ancien doctorant du LGP2.
Techniques de l’Ingénieur : Comment parvenez-vous à déposer une fine couche de céramique sur de la cellulose ?
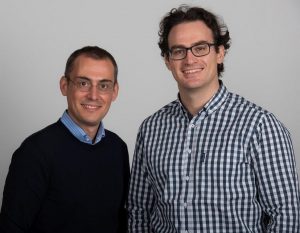
Frédéric Mercier : Les matériaux cellulosiques possèdent des liaisons chimiques intéressantes à leur surface, appelées des groupements OH (ou groupements hydroxyles), qui sont capables de réagir avec un composé organométallique, lequel a la particularité d’être un précurseur de la céramique. Il se présente sous la forme d’un gaz et va interagir avec les liaisons OH, pour former un revêtement de céramique très fin (inférieur à 50 nanomètres) sur toute la surface du papier. Quelques atomes de céramique vont ainsi venir se greffer sur chaque fibre de cellulose. C’est comme si on plaçait une coquille de céramique autour de chaque fibre.
Quelles difficultés avez-vous dû surmonter pour mettre au point ce procédé ?
Erwan Gicquel : Habituellement, ce procédé, appelé ALD (Atomic layer deposition), est utilisé en salle blanche, avec des matériaux lisses, non rugueux, et dans un environnement sans poussière. Il est notamment employé dans le domaine de la microélectronique. Cette technologie est donc à des années-lumière de l’univers papetier, où il y a de la poussière partout, les matériaux sont rugueux, massifs…
Ce procédé de dépôt d’une couche nanométrique de céramique sur de la cellulose existait déjà dans la littérature, mais était uniquement adapté à des surfaces de quelques cm². Tout notre travail de recherche, démarré en 2018, a consisté à le rendre compatible avec les volumes de l’industrie de l’emballage, dont les besoins se chiffrent à plusieurs centaines de millions de m². Nous avons réalisé de nombreuses expérimentations afin de tester différents points de fonctionnement, sur différentes feuilles de papier. Nous avons couplé ce travail à de la simulation, pour comprendre comment ce gaz s’introduit dans chaque fibre de cellulose. Nous avons aussi développé des méthodes pour caractériser très précisément la présence de ces quelques nanomètres de céramique sur toute la surface des papiers.
Quelles sont les performances de votre nouveau matériau ?
F.M : La cellulose possède de nombreuses propriétés intéressantes, mais ne supporte pas l’eau. Dès la moindre trace d’humidité, elle se désagrège et il n’y a plus aucune tenue mécanique sur ce support. Grâce au dépôt d’une couche nanométrique de céramique, la cellulose devient inerte à la vapeur d’eau, aux liquides, ainsi qu’aux gaz. Il est par exemple possible de fabriquer un papier hydrophobe ou possédant un effet de barrière aux gaz. Ces propriétés sont uniquement obtenues grâce aux quelques nanomètres de céramique greffés à la surface de chaque fibre de cellulose ; il ne s’agit pas d’un enduit ou d’un vernis qui risqueraient de bouger ou de s’écailler. Ces liaisons chimiques sont intimement liées à la surface de la fibre.
Au final, on obtient un matériau dont les propriétés barrières sont similaires à celles des plastiques et composé à plus de 99,9 % de cellulose et de quelques atomes de céramique. Ce revêtement est totalement transparent et imprimable ; on ne voit pas la différence entre un papier traité ou non traité. Et, bonne nouvelle, ce matériau se dégrade comme du papier, en condition de compostage ou de recyclage. C’est une innovation sans équivalent sur le marché.
Quelles applications ciblez-vous ?
E.G : Nous ciblons tous les emballages à usage unique au sens large, qui ne peuvent pas être recyclés actuellement, qu’ils soient alimentaires ou cosmétiques. Nous avons bâti une stratégie pour atteindre le marché étape par étape. Nous allons commencer par les emballages de produits secs, puis aller progressivement vers ceux contenant des produits liquides, comme les pots de yaourt. Dans ce cadre, nous proposons également une alternative aux emballages aujourd’hui complexes, comme les paquets de chips qui contiennent plusieurs couches, dont une métallisée.
À quel stade de développement se trouve votre projet ?
F.M : Nous venons de créer une start-up au 1er juin. D’un point de vue technologie et industrialisation, nous allons devoir réaliser un changement d’échelle, afin de rendre compatible notre procédé avec les demandes des clients. Nous sommes déjà en contact avec des industriels de l’agroalimentaire, qui ont manifesté leur intérêt pour notre produit.
Notre business model, au moins dans un premier temps, sera celui de la prestation de service, afin de transformer le matériau cellulosique de nos clients. Ils vont nous apporter leurs matériaux cellulosiques et notre rôle sera d’y apposer notre revêtement en céramique. Nous allons aussi les conseiller sur des matériaux.
Notre objectif est de mettre en service notre première usine en 2024/2025, mais en attendant, nous travaillons avec nos clients pour qualifier les matériaux et revêtements sur des applications concrètes. Avec nos réacteurs pilotes, situés dans le laboratoire SIMAP avec qui nous collaborons, nous sommes même capables de répondre à des besoins en production pour de petites séries.
Nous sommes dans le bon « timing » pour répondre aux besoins des industriels qui sont confrontés à l’échéance de 2025 ; une date à partir de laquelle la majeure partie des plastiques devront avoir disparu des emballages à usage unique. Nous avons déjà validé notre modèle économique, c’est-à-dire que nous allons pouvoir offrir un matériau d’emballage doté de fonctions barrières, totalement biodégradable et recyclable, pour un coût cohérent avec le marché.
Réagissez à cet article
Vous avez déjà un compte ? Connectez-vous et retrouvez plus tard tous vos commentaires dans votre espace personnel.
Inscrivez-vous !
Vous n'avez pas encore de compte ?
CRÉER UN COMPTE