Après une thèse sur la fabrication de bioplastiques à base de farine de maïs au laboratoire IMP (Ingénierie des matériaux polymères) à Saint-Étienne, Fanny Deleage exerce son premier emploi dans l’industrie agroalimentaire. Elle a pour mission de concevoir de la « fausse viande » à partir de protéines végétales. À la suite de ses deux expériences, elle a l’idée de combiner ses deux savoir-faire pour reconstituer la structure moléculaire du cuir à l’aide de produits 100 % biosourcés. Elle retourne dans son laboratoire d’origine et convainc son ancien directeur de thèse, Yvan Chalamet, de développer son idée avec elle. Tous les deux parviennent à la preuve de concept d’un nouveau matériau et créent, en août 2020, une start-up. Rencontre avec Fanny Deleage, la cofondatrice de La tannerie végétale.
Techniques de l’Ingénieur : Comment avez-vous réussi à reconstituer la texture du cuir à partir de matières biosourcées ?
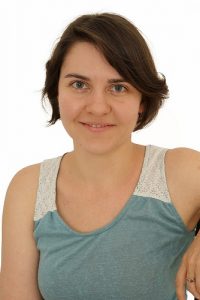
Fanny Deleage : L’idée de départ est de reprendre le même procédé que celui utilisé pour fabriquer des cuirs, qui consiste à associer des protéines animales à des tannins minéraux, métalliques ou végétaux, en les remplaçant par des protéines végétales et des tannins uniquement végétaux. Au final, cela donne un matériau thermoplastique malléable, aux propriétés mécaniques similaires au cuir, et que l’on peut mettre en forme comme du plastique. Cette idée n’avait jamais été utilisée pour concevoir un nouveau matériau.
Notre travail de recherche a consisté à trouver le bon procédé de mélange pour fusionner les protéines végétales et les tannins ainsi que les bons additifs afin que la rhéologie (étude de la déformation et de l’écoulement, NDLR) du matériau soit correcte et qu’il soit capable de se mettre en forme sans défaut. Le produit fini obtenu ressemble à une feuille, que l’on assemble en rouleau.
Quels protéines végétales et tannins utilisez-vous ?
Notre technologie peut s’adapter à toutes les protéines végétales, mais pour l’instant, nous avons choisi d’utiliser le gluten de blé. Il est en effet très abondant, car il est boudé en alimentation humaine et principalement valorisé en alimentation animale. C’est aussi une démarche éthique de notre part de le valoriser autrement. Il présente aussi l’avantage d’être bien documenté dans la littérature scientifique. Quant aux tannins, comme toutes les tanneries, nous devons garder notre savoir-faire secret.
Quels sont les avantages de ce nouveau matériau ?
Contrairement aux cuirs et aux similis, qui consomment beaucoup de produits chimiques et toxiques, notre matériau en est totalement dépourvu. Dans notre formulation, nous sélectionnons toujours, lorsque cela est possible, des produits biosourcés et utilisons le moins possible de produits issus du pétrole. Ensuite, notre procédé de mélange ne fait pas appel à de la chimie et ne consomme pas d’eau, à l’opposé des tanneries qui s’installent presque toutes à proximité de rivières. Notre matériau est donc entièrement biodégradable et recyclable. Nous avons réalisé une première estimation de son bilan carbone et son impact est inférieur à 4 kg de CO2 équivalent par m², alors que les similis sont autour de 12 à 15 et les cuirs jusqu’à 40.
Son aspect et sa texture sont-ils identiques aux cuirs et aux similis ?
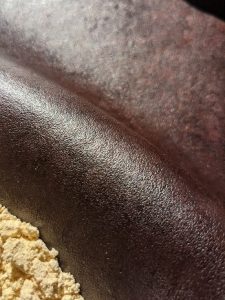
Une personne n’ayant pas d’expertise du cuir ne verra pas la différence. Un œil affiné s’apercevra qu’en dessous, il ne possède pas la texture fibreuse sur le côté chair du cuir, mais c’est un aspect que l’on cherche à développer.
Quant au dessus, le cuir est souvent retravaillé par les industriels qui ne laissent pas sa texture naturelle. Une autre texture est ajoutée par-dessus, grâce à la technique d’embossage, qui consiste à créer des formes en relief à la surface. Nous pouvons procéder à la même technique à l’aide d’un gros laminoir, ce qui permet à notre matériau d’avoir un aspect et une texture similaire au cuir sur cette face.
À quel stade de développement se trouve votre projet ?
Nous sommes financés par la SATT (Société d’Accélération du Transfert de Technologies) Pulsalys, qui nous a permis de faire maturer notre technologie pendant un an. Nous poursuivons ce travail pendant quelques mois pour atteindre 100 % du cahier des charges des cuirs et des similis traditionnels, afin que nos clients, les entreprises de la maroquinerie, n’aient aucun compromis à faire sur la technique, en ayant un produit aussi résistant, mais écoresponsable.
Pour l’instant, nous fabriquons des feuilles de 15 cm de large, mais cette taille est limitante pour fabriquer par exemple un sac à main. Grâce à un financement de Bpifrance obtenu via le concours d’innovation i-Lab, nous allons nous équiper d’une machine capable de fabriquer des feuilles de 50 cm de large. À la fin de l’année, notre objectif est de nous installer dans notre atelier pour produire de grandes quantités et assumer nos commandes.
En parallèle, nous évaluons la « travaillabilité », c’est-à-dire la manière dont notre matériau se comporte avec les machines à coudre, les fils, et tout le processus de fabrication d’un objet. Notre entreprise va produire et vendre ce nouveau matériau sous la forme de rouleaux aux acteurs de la maroquinerie tout en les accompagnant dans ce changement.
Dans l'actualité
- Les premières bouteilles PET 100% biosourcées sortent d’usine
- Produire en France une fibre de carbone économique et biosourcée
- Innovantes #7 : Evaluer la toxicité de produits sans passer par l’animal
- Fabriquer des bioplastiques grâce à la culture de microalgues
- Techniques de l’Ingénieur est partenaire de FIP – France Innovation Plastiques
- Matériaux métalliques : quelles propriétés pour quelles applications ?
- De futures constructions en pâte de mycélium
Dans les ressources documentaires