Figurant parmi les leaders européens des systèmes de canalisation en fonte ductile, Saint-Gobain PAM est aussi, en conséquence, un important émetteur de gaz à effet de serre… Une situation à laquelle l’entreprise – qui fêtera son cent soixante-dixième anniversaire l’an prochain – est toutefois en passe de remédier, grâce à la mise en place progressive d’une ambitieuse stratégie de décarbonation de ses installations de production, essentiellement basée sur leur électrification.
Après avoir mis en service en 2022, sur son site de Pont-à-Mousson, le plus grand four électrique d’Europe pour la production de fonte ductile – Thor – l’entreprise planche aujourd’hui, notamment, sur la transposition de l’opération à un autre de ses sites de production : celui de Foug, près de Toul, en Meurthe-et-Moselle. Baptisé Vulcain, ce four à induction devrait permettre d’éviter l’émission d’environ 22 400 tonnes de CO2 par an, soit un peu plus de 65 % des émissions totales du site. Après avoir posé la première pierre de cette future installation au printemps dernier, PAM vise désormais une mise en service à la rentrée 2025. Neill McDonald, directeur adjoint R&D, innovation, développement durable et directeur de projet électrification, nous livre les détails de ce projet aussi ambitieux que vertueux.
Techniques de l’Ingénieur : Avant toute chose, pouvez-vous, en quelques mots, nous présenter Saint-Gobain PAM ?
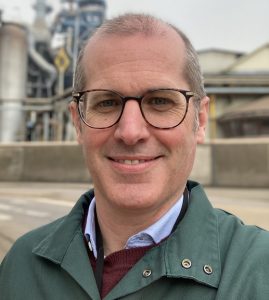
Neill McDonald : Saint-Gobain PAM a été créée en 1856 à Pont-à-Mousson – d’où le « PAM » – sous le nom de Société anonyme des hauts fourneaux et fonderies de Pont-à-Mousson. Depuis ses débuts, l’entreprise produit essentiellement des pièces en fonte, destinées notamment au secteur de l’eau. Nous proposons aujourd’hui des systèmes complets de canalisations en fonte ductile, destinés à l’eau sous toutes ses formes : potable, industrielle, d’assainissement…
Nos clients directs sont principalement des entreprises de travaux publics, qui mettent en œuvre ces systèmes de canalisation pour le compte de collectivités, ou, dans une moindre mesure, d’industriels.
En quoi votre procédé de production consiste-t-il, dans les grandes lignes ?
Nous achetons tout d’abord des ferrailles, ainsi que du minerai de fer et du coke. Nous faisons ensuite fondre ces matières, soit dans un haut fourneau comme à Pont-à-Mousson, soit dans un cubilot, ce qui est notamment le cas sur notre site de Foug. Cela nous permet d’obtenir une fonte liquide qui, après une série d’étapes de traitement, nous permet de couler des pièces. Cela peut se faire à plat, notamment pour nos célèbres plaques d’égout, mais aussi par centrifugation, pour nos tuyaux. Cette seconde option consiste, en substance, à couler le métal liquide dans une machine en rotation, contre les parois de laquelle la matière en fusion vient alors se plaquer pour, finalement, obtenir un tuyau cylindrique en fonte, qui bénéficie enfin de diverses étapes de traitement, anticorrosion notamment.
Une fonte, qui a certes de nombreux intérêts, mais aussi, revers de la médaille, une forte empreinte carbone…
Effectivement. La fonte permet, tout d’abord, d’assurer à la fois la qualité de l’eau transitant par les canalisations, et la longévité des réseaux, avec des tuyaux qui peuvent durer jusqu’à une centaine d’années, voire plus, en minimisant les fuites.
Dans le contexte de changement climatique que nous connaissons actuellement, a toutefois fini par émerger la question de l’empreinte carbone de nos produits. Cela est d’ailleurs progressivement devenu un critère de sélection dans les marchés publics, d’abord dans les pays scandinaves, et plus récemment aussi ici, en France, et dans le sud de l’Europe.
Nous avons donc, face à cela, entamé une réflexion portant sur la décarbonation de notre production. Pour des raisons environnementales et financières, mais aussi, tout simplement, pour répondre à la demande de nos clients, pour qui la question des émissions indirectes représente aujourd’hui un enjeu de plus en plus important.
Avant de procéder à des investissements, nous avons commencé par étudier nos sources d’émissions, en réalisant une analyse de cycle de vie (ACV) complète de nos activités, en prenant en compte la production, bien entendu, mais aussi les achats, les matières premières, le transport… Nous avons ainsi assez rapidement identifié que, au sein de notre chaîne de valeur, les moyens de fusion du métal représentaient la majeure partie – plus de 80 % – de nos émissions de gaz à effet de serre. Ceci, notamment parce qu’ils utilisent du coke : pour chauffer la matière dans le cas du cubilot, mais aussi, en plus, pour réaliser des réactions chimiques de réduction dans le cas du haut fourneau.
Problématique en soi, cette part très importante de nos émissions directes nous est aussi apparue, finalement, comme un puissant levier à actionner pour agir et décarboner notre production. Cela nous a pour ainsi dire paru « rassurant » de constater que nous avions les moyens de réduire drastiquement nos émissions.
Cela s’est ainsi naturellement traduit par la mise en œuvre de projets visant à remplacer, sur chacun de nos sites, ces moyens de production carbonés, par de nouveaux outils moins émetteurs.
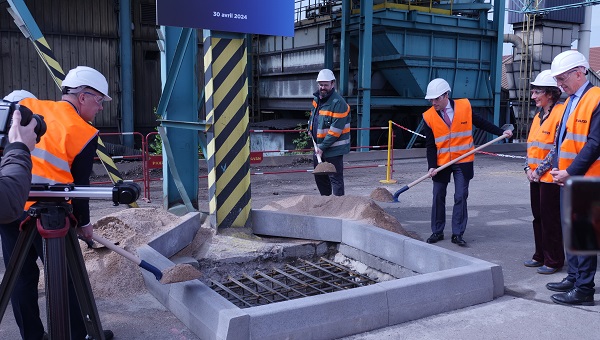
Quelle est justement la voie que vous avez choisi d’emprunter, pour réaliser cette transformation « verte » de vos moyens de production ?
Nous avons rapidement choisi de nous tourner vers des solutions d’électrification technologiquement matures. Ceci, afin de décarboner rapidement, sans pour autant prendre de risques inconsidérés avec des solutions pas encore éprouvées. Nous nous sommes donc tournés vers deux technologies de fusion bien connues, que sont le four à induction, et le four à arc électrique. Cette deuxième option, que nous avons choisie pour notre haut fourneau de Pont-à-Mousson, reste pour l’heure au stade de projet, et devrait être mise en œuvre à l’horizon 2030. C’est en revanche déjà le cas pour la technologie de four à induction que j’évoquais… En 2022, nous avons en effet mis en service sur notre site de Pont-à-Mousson, le plus grand four électrique d’Europe pour la production de fonte ductile : Thor. Ce projet, sur lequel nous planchions depuis le début de la pandémie, nous a ainsi permis de compléter nos outils de production, tout en nous permettant de commencer à réduire nos émissions.
Ce four nous permet en effet d’avoir moins recours à nos hauts fourneaux, en n’en utilisant qu’un sur deux, par exemple. Au-delà des émissions directes, cela nous permet aussi de réduire nos émissions indirectes en utilisant davantage de ferrailles – ce que nous ne pouvions pas faire avec nos hauts fourneaux – provenant à la fois de boucles de recyclage internes et externes. Cet outil nous permet ainsi d’éviter l’émission d’environ 30 000 tonnes de CO2 par an – voire jusqu’à 50 000 tonnes en cas d’utilisation intensive – sur un total d’environ 350 000 tonnes pour ce site de Pont-à-Mousson.
Face à ces résultats pour le moins encourageants, nous avons décidé de répliquer ce four électrique sur un autre de nos sites de Meurthe-et-Moselle : celui de Foug, près de Toul. Notre objectif, cette fois, et de venir purement et simplement remplacer le moyen de fusion carboné dont dispose pour l’heure l’usine : un cubilot. Baptisé Vulcain, ce nouveau four sera identique sur le plan de sa capacité à Thor – 30 tonnes, pour 18 MW de puissance – à la différence près qu’il disposera de deux creusets, afin d’en accroître la productivité.
Qu’implique, techniquement, ce passage du cubilot au four électrique ? Quel est le niveau de complexité d’un tel projet ?
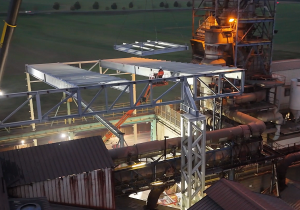
Il s’agit véritablement d’une opération de rupture, d’une grande complexité, et ce à plusieurs niveaux. Notre voulions tout d’abord éviter que cela n’affecte les procédés avals à la fusion, notamment les étapes de centrifugation. Ceci bien entendu pour des questions de coûts et de qualité – nos produits étant très normés – mais aussi de compétences. Nous nous sommes aussi fixé l’objectif de produire, grâce à ce futur four Vulcain, une fonte de même qualité que celle du cubilot actuel. Cela implique donc d’adapter au mieux notre approvisionnement en matières premières, notamment en ferrailles. Celles que nous utilisons aujourd’hui dans notre cubilot ne se prêtent en effet pas à une fusion dans un four électrique à induction. Nous avons donc commencé par qualifier nos futures matières premières, en utilisant notamment notre four Thor comme outil de tests.
D’autre part, contrairement au cubilot, un four électrique n’utilise pas de coke… Or, ce coke permet aussi de charger le métal en carbone au cours de la fusion. Nous allons donc, en plus du changement de type de ferrailles que j’évoquais, devoir « re-carburer » la charge contenue dans le creuset. C’est une opération que d’autres acteurs dans le monde réalisent déjà, mais qui constitue une nouveauté pour nous.
Ensuite, faire tourner ce four à induction n’implique pas les mêmes compétences que celles nécessaires pour gérer un cubilot. Nous allons donc mettre en place un accompagnement visant à former notre personnel, notamment à de nouvelles compétences autour de l’électricité haute tension.
Enfin, un autre point capital est celui de l’organisation du chantier de construction du four à proprement parler, mais aussi des opérations de mise en place d’une ligne électrique dédiée à son alimentation. Le tout, en toute sécurité, et sans interrompre le fonctionnement du site…
Quel est le coût d’un tel projet ? Comment avez-vous prévu de le financer ?
Ce projet de four électrique Vulcain représente un investissement de l’ordre de 20 M€. C’est peu et beaucoup à la fois… Peu face à d’autres projets de décarbonation industrielle, qui peuvent parfois, en effet, se chiffrer en centaines de millions d’euros… Mais aussi beaucoup pour une entreprise telle que PAM, d’autant que l’intérêt de l’opération ne tient pas tant à de potentiels gains de productivité qu’aux émissions de CO2 qu’elle permettra d’éviter.
Pour financer ce projet, nous avons notamment d’ores et déjà obtenu un financement de l’Ademe d’un peu plus de 5,5 M€. Nous espérons aussi une aide de la région pour la partie R&D du projet, et éventuellement un soutien de l’Agence de l’eau. Le projet vise en effet également à réduire de 80 % les prélèvements d’eau du site, grâce à la mise en place d’un circuit de refroidissement en boucle fermée. C’est aussi un aspect très important pour nous, qui permet en effet à la fois de préserver la ressource et de prévenir tout arrêt d’activité lié à un épisode de sécheresse.
Réagissez à cet article
Vous avez déjà un compte ? Connectez-vous et retrouvez plus tard tous vos commentaires dans votre espace personnel.
Inscrivez-vous !
Vous n'avez pas encore de compte ?
CRÉER UN COMPTE