La start-up Sintermat a industrialisé un procédé appelé le frittage flash qui permet de concevoir des matériaux augmentés à partir de poudres métalliques, composites et naturelles. L'entreprise vient de boucler une deuxième levée de fonds afin d'accélérer sa croissance. Rencontre avec Foad Naimi, son fondateur.
Créée en 2016, la start-up Sintermat développe une technologie de pointe issue d’un laboratoire de recherche de l’Université de Bourgogne, et peu répandue en Europe : le frittage flash, encore appelé frittage SPS (Spark Plasma Sintering). À partir de tous types de poudres, l’entreprise conçoit des matériaux aux propriétés augmentées ayant une haute résistance, une haute densité, une dureté améliorée, une durée de vie allongée… En 2018, une première levée de fonds lui a permis d’industrialiser son procédé. Il y a quelques semaines, la société a bouclé un second tour de table, d’un montant de 6 millions d’euros, dans le but d’accélérer sa croissance. Entretien avec Foad Naimi, le fondateur, président, et CEO de Sintermat.
Techniques de l’Ingénieur : Comment fonctionne votre technologie ?
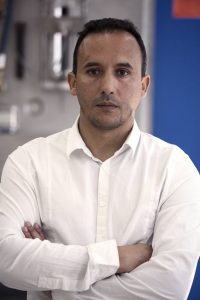
Foad Naimi : Notre procédé consiste à agglomérer des poudres sous l’effet simultané d’une forte impulsion électrique et d’une charge uniaxiale. Concrètement, nous venons encapsuler tous types de poudres dans un outillage qui va donner la forme finale de la pièce. La poudre est placée entre deux pistons et nous lui appliquons une contrainte qui peut aller jusqu’à 320 tonnes. Simultanément, elle est chauffée à la température de frittage du matériau, qui peut atteindre 2 400 degrés, grâce à un courant électrique qui se diffuse par l’intermédiaire du piston de compression et de l’outillage, qui sont tous les deux conducteurs. Lorsque la poudre est conductrice, comme c’est le cas avec les métaux, le courant électrique passe également à travers elle et va alors la chauffer directement.
Quels sont les avantages de votre procédé ?
Comparé aux procédés conventionnels qui fonctionnent avec un four et qui nécessitent d’attendre que l’enceinte atteigne son équilibre thermique, le frittage SPS chauffe au plus près de la poudre, voire à travers la poudre, en un temps court compris entre un quart d’heure et une demi-heure (hors refroidissement). Grâce à cette rapidité de fabrication, nous sommes capables de concevoir des matériaux possédant des microstructures sans grossissement des grains et avec un taux de densification voisin de 100 %. Nous parvenons ainsi à fabriquer des matériaux aux performances et aux propriétés améliorées. Par exemple, nous fabriquons de l’outillage industriel dont la durée de vie peut être multipliée par 3, 4, et parfois jusqu’à 10. Ces performances sont synonymes d’économies en maintenance et donc de coûts en moins. Sur des pièces pour des applications de défense, nous avons démontré que nos matériaux avaient une résistance mécanique multipliée par 3, comparée à ceux conçus de manière traditionnelle, et ceci sans perte importante en allongement. Sur d’autres matériaux, nous obtenons également un meilleur comportement à chaud, une meilleure tenue aux températures, ou à l’électricité.
Comparé aux procédés conventionnels, le frittage SPS nous permet également d’obtenir un gain énergétique très important dans la fabrication des pièces compris entre un facteur 3 et 5.
Cette technologie n’est pas nouvelle, qu’est-ce qui vous différencie de vos concurrents ?
Le procédé existe depuis très longtemps puisque les premières machines datent des années 1960, mais il est seulement arrivé en Europe un peu avant l’an 2000. Depuis, des entreprises ont repris cette technologie et sont capables de produire de grands volumes, mais elles se sont spécialisées dans la fabrication de pièces en céramique pour le secteur de la défense et du médical.
En 2016, nous avons fait le pari de l’industrialiser de façon plus large. Nous travaillons sur tous types de matériaux : métaux, alliages, intermétallique, carbures, céramiques, borures, siliciures… et même tous types de mélange et d’alliage imaginable, à condition bien sûr que la thermodynamique et la loi du mélange soient compatibles.
En termes d’application, nous visons par exemple le secteur de l’aéronautique, qui recherche des matériaux possédant de meilleures propriétés en fluage, la défense qui recherche des pièces capables de résister à des impacts grâce à des propriétés de blindages. Nous ciblons aussi le luxe et fabriquons pour ce secteur des matériaux possédants certaines qualités, notamment antirayure.
Nous créons aussi de nouveaux matériaux dont les formulations ne sont pas possibles avec les procédés traditionnels. Par exemple, nous sommes partis d’un composite céramique et l’avons complètement reformulé, afin d’obtenir une dureté supérieure à celles du saphir, et une apparence qui ressemble à celle d’un matériau métallique, pour le secteur de l’horlogerie.
À quel stade de développement se trouve votre projet ?
Depuis 2018, grâce à une première levée de fonds, nous avons commencé à créer un outil industriel qui permet de concevoir des pièces jusqu’à 350 mm de diamètre, pour des hauteurs avoisinant 100 mm. Nous l’avons automatisé et robotisé, ainsi que travaillé sur l’augmentation de productivité pour que la solution technico-économique proposée par Sintermat soit viable sur le marché. En parallèle, nous avons protégé la propriété intellectuelle de notre technologie en déposant 10 brevets.
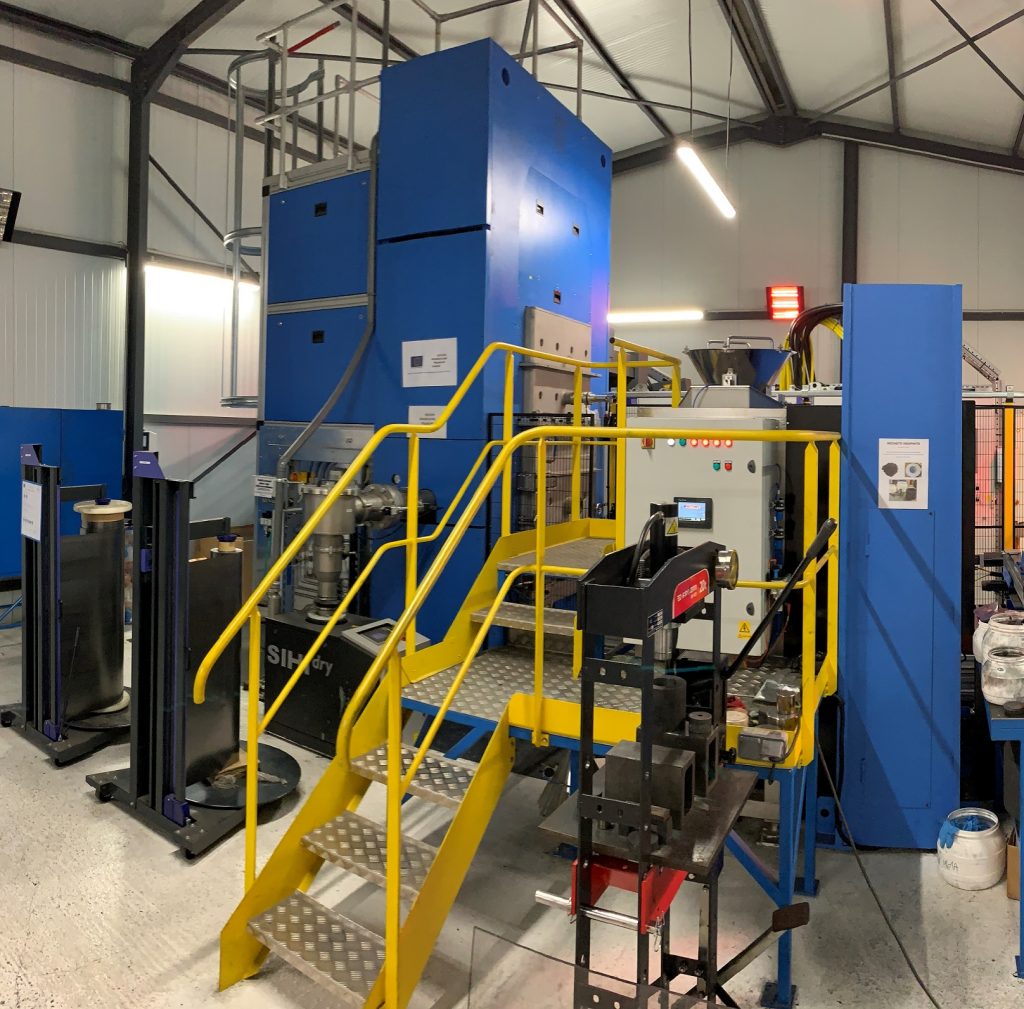
Grâce à notre deuxième levée de fonds, nous allons accélérer notre industrialisation en déménageant dans un hall industriel à Venarey-les-Laumes, à côté de Dijon. Nous aurons plus d’espace et nous allons pouvoir avoir notre propre laboratoire de contrôle, et ainsi assurer en interne le suivi de nos premières pièces en série à destination de nos clients. Nous souhaitons aussi acheter une deuxième machine afin d’augmenter nos capacités de réponse à nos clients, ainsi que renforcer notre équipe commerciale.
Nous sommes dans une phase d’augmentation de nos volumes de production et nous avons aussi des prototypes en test à l’échelle 1 chez des clients qui donnent d’excellents résultats ; l’un d’eux concerne la conception de pions de tête de forage.
Nous avons dupliqué notre procédé pour fritter des produits biosourcés comme des coquilles d’huîtres broyées, des sarments de vigne, du chanvre, du lin et de la nacre. À partir de ces matériaux naturels, nous sommes par exemple capables de remplacer les bouchons en plastique utilisés sur les flacons de parfum ou les bouteilles de vin. Nous sommes actuellement en discussion pour produire ces objets en très gros volumes dès l’année prochaine.
Réagissez à cet article
Vous avez déjà un compte ? Connectez-vous et retrouvez plus tard tous vos commentaires dans votre espace personnel.
Inscrivez-vous !
Vous n'avez pas encore de compte ?
CRÉER UN COMPTE