Dans le cadre des Rencontres Industrielles NextMove organisées le 3 octobre dernier à Louviers, dans l’Eure, nous sommes partis à la rencontre de trois industriels normands qui contribuent, chacun à leur façon, à rendre les plastiques automobiles plus vertueux, et qui sont ainsi soutenus par le pôle de compétitivité. Attachez vos ceintures, Techniques de l’Ingénieur vous emmène pour un road trip industriel made in Normandie !
Du pare-chocs au tableau de bord, en passant par les ceintures de sécurité, les phares ou encore les garnitures de portières : les matières plastiques sont aujourd’hui omniprésentes au sein de nos véhicules. D’après l’Ademe, ce ne sont ainsi pas moins de 750 pièces en plastique que compte, en moyenne, une voiture récente. Un chiffre qui est même certainement sous-évalué, à en croire l’association européenne des producteurs de matières plastiques, PlasticsEurope, citant des données fournies par l’Association Française de Mécanique (AFM) : « Une voiture moderne moyenne pesant 1 500 kg contient entre 12 et 15 % de matières plastiques. Cela équivaut à plus de 2 000 pièces en plastique de toutes formes et de toutes tailles ».
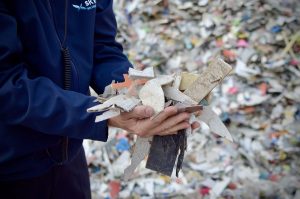
Quel qu’en soit le nombre exact de pièces, cette abondance place ainsi les plastiques au deuxième rang des familles de matériaux les plus utilisées dans la fabrication automobile, juste derrière les métaux. Problème : si cette utilisation des matériaux plastiques dans les véhicules a évidemment de multiples vertus – à commencer par leur allègement – elle ne va pas sans soulever un certain nombre de questions sur le plan environnemental.
Recyclage : le secteur automobile peut (et devra) mieux faire
Encore très largement pétrosourcés, avec une part de seulement 11,2 % de matière issue du recyclage ou biosourcée en 2022, les plastiques automobiles – situés au troisième rang des usages, avec une part d’un peu plus de 8 % de la demande en Europe en 2022, soit 4,5 millions de tonnes environ – ne sont, en outre, que relativement peu recyclés une fois la voiture arrivée en fin de vie… Une situation encore loin d’être optimale, donc, mais qui pourrait bien changer à la faveur, notamment, de l’évolution de la réglementation.
À l’été 2023, la Commission européenne a en effet proposé une série de mesures visant à renforcer la circularité des matières dans le secteur automobile ; l’une d’elles indiquant notamment que « 25 % du plastique utilisé pour la construction d’un nouveau véhicule devront provenir du recyclage, dont 25 % devront être issus de véhicules hors d’usage ». Une « ambition forte », telle que la qualifie Plastics Europe, qui la considère pour autant tout à fait atteignable, tout en pointant, dans un argumentaire daté de novembre 2023, les conditions nécessaires à ses yeux pour y parvenir. « Atteindre ces ambitions nécessitera des investissements importants dans la gestion des déchets, la collecte, le tri, mais aussi l’augmentation des capacités de recyclage », note ainsi notamment l’association européenne des producteurs de plastiques, qui souligne aussi, par ailleurs, l’importance que revêt « l’utilisation de matières premières innovantes et alternatives », et notamment de plastiques biosourcés…
Autant d’enjeux dont s’est justement saisis celui qui accompagne dans leurs démarches d’innovation, de développement, d’industrialisation ou encore d’accélération les acteurs de la filière automobile : le pôle de compétitivité NextMove.
Créé en 2006, ce bras armé de la PFA[1] est implanté sur un territoire concentrant à lui seul 25 % des activités de la filière automobile & mobilité française : l’Île-de-France bien sûr, mais aussi l’une de ses voisines, la Normandie. C’est là, et plus précisément dans le département de l’Eure, que NextMove nous a invités à venir découvrir quelques illustrations concrètes de ses actions d’accompagnement en faveur des acteurs de l’économie circulaire et décarbonée des plastiques automobiles.
Les vaches rousses, blanches et noires… et des plastiques recyclés made in Normandie !
Notre parcours normand débute au Val-d’Hazey, une commune nouvelle située à une trentaine de kilomètres au nord-est d’Évreux. C’est là, en effet, que Skytech — PME industrielle française spécialiste du recyclage de matières plastiques, nous y reviendrons – a inauguré, en octobre 2022, son nouveau siège social et sa nouvelle usine, au prix d’un investissement de plus de 17 millions d’euros. Des locaux flambant neufs, ou presque.
Bordant la Seine, ils sont en effet le fruit de la reconversion d’un site qui fait partie du patrimoine industriel local, laissé en friche depuis 2014 et la cessation de la dernière activité en date — la fabrication de câbles électriques. Un héritage composé notamment de bâtiments érigés dans les années 30, reconnaissables à leur structure métallique en treillis si caractéristique, que Skytech a pris le parti de sauvegarder, dans un esprit finalement pas si éloigné de son cœur de métier : le recyclage.
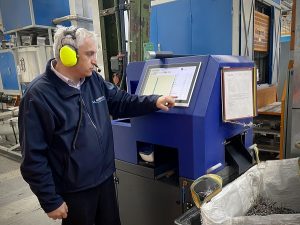
La PME s’attelle en effet à la régénération de polymères plastiques – ABS[2], polystyrène (PS) et polypropylène (PP) – via un procédé de séparation électrostatique qu’elle a elle-même mis au point à l’issue de pas moins de dix ans de travail de R&D. « Ce procédé de “triboélectrisation”, protégé par quatre brevets, repose sur le même principe que le bâton d’ébonite que l’on frotte avec de la laine », illustre Frédéric Delaval, directeur général de Skytech. « Notre approche nous permet de séparer avec une grande efficacité l’ABS, le PP et PS, pour obtenir finalement un produit pur à plus de 99 %, et ce, avec une empreinte carbone cinq fois et demie moins importante qu’un équivalent vierge[3] », fait valoir le dirigeant de la PME normande.
Skytech, dont le savoir-faire repose aussi en partie sur ses capacités à formuler, à partir de ces matières plastiques issues du recyclage, des résines régénérées répondant parfaitement aux cahiers des charges de ses clients industriels. Des clients qui œuvrent notamment dans le secteur de la fabrication d’appareils électroménagers, à l’image de Krups, Seb, ou encore Rowenta, mais qui représentent aussi, pour une part croissante d’entre eux, le secteur de l’automobile, comme l’explique Frédéric Delaval : « Nous travaillons depuis peu avec les industriels qui démantèlent les véhicules hors d’usage (VHU). Nous récupérons ainsi les matières plastiques issues des pare-chocs, des calandres ou encore des arrières d’optiques de ces voitures en fin de vie. L’idée, ensuite, est de régénérer ces plastiques, pour les rediriger, in fine, vers la filière de production de pièces automobiles en plastique ». Une boucle d’économie circulaire prometteuse, dont Skytech est d’ailleurs d’ores et déjà l’un des maillons, avec une production de quelques centaines de tonnes déjà réalisée cette année…
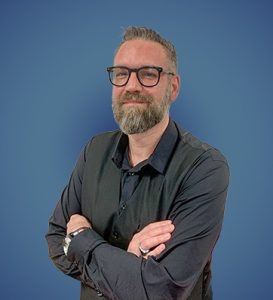
« Skytech est un acteur qui s’inscrit résolument dans l’air du temps, et va à n’en pas douter devenir un acteur incontournable du secteur », assure ainsi Johann Carpentier, Directeur Industrialisation & Excellence opérationnelle chez NextMove. « J’ai le plaisir d’accompagner Skytech depuis plusieurs mois, dans sa structuration et son développement industriel. Cela se traduit notamment par un accompagnement à la montée en compétences de ses équipes », explique-t-il. Un aspect qui est d’ailleurs loin d’être le seul sur lequel le pôle de compétitivité est en mesure d’accompagner ses adhérents, comme l’illustre un autre exemple qu’il nous a été permis de découvrir lors de cette escapade normande : celui d’EPH.
EPH : la décarbonation servie sur un plateau
Notre parcours se poursuit à St-Aubin-Sur-Gaillon, une petite commune de l’Eure située à cinq kilomètres à peine du Val-d’Hazey, qu’a en effet choisie pour y implanter, en 2018, ses locaux flambants neufs, la société EPH (Emballages Plastiques D’Heudreville). Une PME créée il y a plus de cinquante ans à Heudreville-sur-Eure et acquise en 2011 par le groupe alsacien CTCI.
Spécialisée dans la fabrication de solution de conditionnement et de pièces thermoformées sur mesure, l’entreprise normande imagine et produit des solutions optimisées pour l’emballage, la manutention et le transport de produits d’une large palette d’industriels : des fabricants de produits cosmétiques aux entreprises agroalimentaires, en passant – donc – par les acteurs de la filière automobile. « Nous leur fournissons notamment des plateaux de manutention alvéolés, qui permettent de transporter de manière optimale des pièces automobiles depuis l’usine qui les produit jusqu’à celle qui se charge de les assembler », explique David Leleu, président du groupe CTCI. « Ces plateaux, fabriqués à partir de divers plastiques thermoformés, permettent de gagner de la place, de garantir la qualité des produits transportés, voire de robotiser leur assemblage », fait valoir le dirigeant.
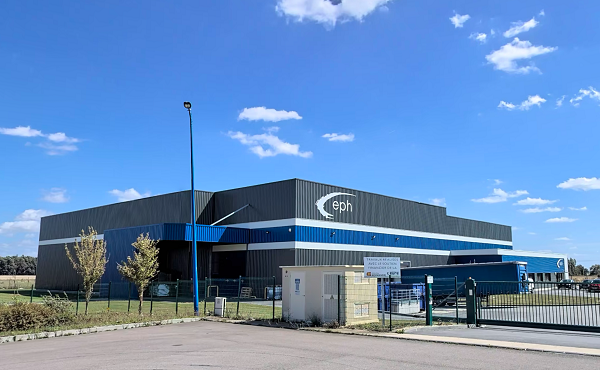
Seule ombre au tableau : ces plateaux étaient, au départ, à usage unique. « Une fois transportés de l’usine A à l’usine B, ils finissaient tout simplement jetés parmi les autres DIB[4] », se remémore David Leleu, employant l’imparfait à dessein. Face à ce constat, EPH a en effet décidé, en 2016, de développer une approche plus vertueuse de récupération, broyage et re-fabrication de plateaux. Une première avancée incarnée par cette solution de recyclage, à laquelle s’est ensuite ajoutée une seconde option : la réutilisation.
« Nous avons en effet développé, au départ pour les besoins d’un grand fabricant de produits cosmétiques, une solution de réemploi des plateaux de manutention », dévoile David Leleu. Une approche qui a naturellement fini par séduire, elle aussi, l’industrie automobile, comme le note le président du groupe CTCI : « Nous avons notamment mis en place ce système au sein du groupe Renault, sur quelques références de plateaux ».
À la clé : un gain économique – de l’ordre de 50 % selon David Leleu – mais aussi et surtout écologique, avec une empreinte carbone réduite d’environ 40 %. « Les plateaux peuvent en effet être réutilisés entre cent et cent cinquante fois selon leur usage, ce qui permet ainsi de couvrir un cycle complet de production d’un même modèle de véhicule, étalé en général sur six ans », note M. Leleu.
Dans le but, notamment, de faire connaître ses solutions vertueuses aux industriels du secteur, EPH a ainsi rejoint NextMove en avril dernier. « Nous tâchons, depuis lors, de donner de la visibilité à l’entreprise au travers de notre réseau et des évènements que nous organisons régulièrement », explique le Directeur Industrialisation & Excellence opérationnelle chez NextMove, Johann Carpentier. « En parallèle, nous accompagnons aussi EPH dans la modernisation de sa ligne de production », ajoute-t-il. Deux autres illustrations de la palette de services proposés par NextMove à ses adhérents, auxquelles on peut ajouter un ultime exemple : celui de l’entreprise EcoTechnilin, troisième et dernière halte de nos pérégrinations normandes.
EcoTechnilin : la fibre de la décarbonation
Depuis les locaux d’EPH de St-Aubin-Sur-Gaillon, nous mettons cette fois le cap au nord-ouest, pour rejoindre l’un des quatre sites de production d’EcoTechnilin : Valliquerville, commune de Seine-Maritime située à quelques kilomètres d’Yvetot. C’est là, en effet, que la PME, filiale la coopérative agricole NatUp, fabrique notamment des non-tissés à base de fibres naturelles : lin, chanvre, ou encore kénaf, comme nous l’évoquions en mai dernier à l’occasion d’un échange avec son directeur commercial Arnaud Lievre.
« Nous sommes convaincus que les fibres naturelles, au travers de leurs propriétés différenciantes, mais aussi de leur faible impact environnemental et climatique, sont un vrai atout pour réduire l’empreinte écologique de la fabrication automobile », expose à son tour Karim Behlouli, directeur de NatUp Fibres, division regroupant EcoTechnilin, La French Filature et Lemaitre Demeestere.
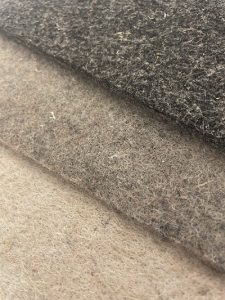
« Nous souhaitons ainsi réinventer l’intérieur des véhicules, en retirant toutes les fioritures qui cachent nos matériaux naturels de renfort : faux cuirs, mousses et autres tissus synthétiques… qui contribuent en effet à l’augmentation du poids, mais aussi du coût et de l’empreinte carbone des véhicules », poursuit le dirigeant.
Une ambition qui s’est ainsi traduite par le lancement d’UpGreen, un projet à 3,6 M€ présenté par EcoTechnilin dans le cadre de l’appel à projets France 2030 « Invest Auto ». « Notre dossier de candidature, pour lequel NextMove nous a apporté un regard extérieur et de précieux conseils, a été approuvé par Bpifrance fin 2023 », se félicite Karim Behlouli, avant de nous donner rendez-vous en 2026, date butoir du projet. « Nous allons bien entendu mener d’ici là des travaux de R&D et de montée en échelle, mais aussi poursuivre les discussions que nous avons d’ores et déjà entamées avec les constructeurs, afin qu’ils soient les plus nombreux possible à adopter nos solutions », confie finalement le dirigeant. Karim Behlouli qui se dit aussi prêt à collaborer avec les équipementiers pour impulser ce changement. Un appel que NextMove ne manquera sans doute pas de relayer aux quelque 550 établissements qui composent son réseau d’adhérents.
[1] La Plateforme automobile, association qui réunit les quelque 4 000 entreprises du secteur automobile national – constructeurs, équipementiers, sous-traitants et autres acteurs de la mobilité – et qui définit la stratégie de la filière en matière d’innovation, de compétitivité, d’emploi et compétences.
[2] Acrylonitrile butadiène styrène.
[3] Comme l’a révélé un bilan carbone réalisé à la demande de l’entreprise, et dont les résultats ont été dévoilés le 3 octobre dernier.
[4] Déchets industriels banals.
Réagissez à cet article
Vous avez déjà un compte ? Connectez-vous et retrouvez plus tard tous vos commentaires dans votre espace personnel.
Inscrivez-vous !
Vous n'avez pas encore de compte ?
CRÉER UN COMPTE