La technologie des réservoirs composites thermoplastiques est née il y a 20 ans, au sein d’un centre de R&D belge : COVESS. Convaincus de l’avenir de cette technologie, trois jeunes entrepreneurs français se sont lancé un défi : industrialiser et commercialiser dans toute l’Europe des réservoirs d’un nouveau genre à partir de celle-ci.
Nous avons interrogé Sébastien Goudalle, ancien ingénieur d’Air Liquide et co-fondateur de COMPOSE IT, afin qu’il nous présente les nombreux avantages apportés par cette technologie unique.
Créée en 2018, la startup lauréate du réseau Entreprendre et membre de La France Water Team, conçoit des réservoirs très résistants, recyclables, et aussi faciles à installer qu’à maintenir.
Techniques de l’Ingénieur : Les réservoirs COMPOSE IT sont basés sur une technologie de mise en œuvre innovante. Pouvez-vous expliquer le fonctionnement de cette technologie ?
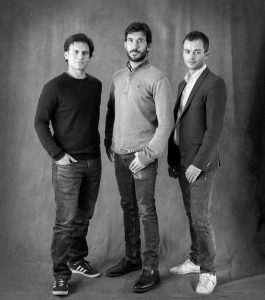
Sébastien Goudalle : Les réservoirs que nous fabriquons sont mis en forme et fonctionnalisés par des empilements successifs de films de matière. Ils sont composés de 2 couches. La couche externe, qui apporte la structure mécanique, est constituée de bandes en fibre de verre enrobées de polypropylène thermoplastique. Contrairement aux procédés classiques, nous n’utilisons pas de liner pour la couche interne. Dans notre procédé, celui-ci est remplacé par un empilement de films de polybutène thermoplastique.
La mise en œuvre entièrement robotisée nous permet d’obtenir de manière reproductible des réservoirs à la structure monolithique, capables de résister jusqu’à 16 bars, voire plus, et conçus dans des matériaux extrêmement durables.
Quels sont les avantages par rapport à des réservoirs en composite thermodurcissable ?
À l’heure actuelle, 100 % des réservoirs composites du marché sont constitués de polymères thermodurcissables et COMPOSE IT est l’unique entreprise française à développer des réservoirs thermoplastiques.
Les polymères thermoplastiques ont d’énormes avantages. D’une part, ce sont des polymères recyclables, ce qui n’est pas le cas des thermodurcissables. D’autre part, les thermoplastiques ne perdent pas leurs propriétés mécaniques en vieillissant, alors que la résistance à la pression des thermodurcissables diminue avec le temps.
La technologie de mise en forme brevetée dont nous détenons la licence exclusive pour la France et l’Allemagne nous permet ainsi de fabriquer des réservoirs d’eau froide pour la surpression et le traitement des eaux, dont la durée de vie est de 50 ans.
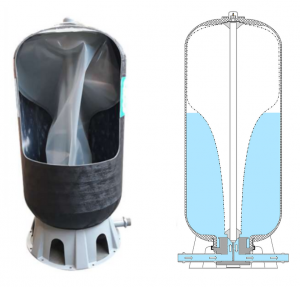
En parallèle, nous sommes par ailleurs en train de développer 2 autres gammes de produits : des réservoirs à air comprimé pour l’industrie ainsi que des réservoirs d’eau chaude sanitaire pour les particuliers.
D’un point de vue technique, quel est l’intérêt d’utiliser un ballon d’eau chaude en composite thermoplastique plutôt qu’un réservoir en acier ?
Actuellement la durée de vie des chauffe-eaux est limitée par la corrosion ainsi que par la formation de calcaire, qui a tendance à se développer sur les aspérités en surface de l’acier. Avec un chauffe-eau en composite thermoplastique, on élimine donc ces deux problèmes, car la paroi interne est extrêmement lisse, ce qui empêche la formation du tartre. Ceci se traduit par la suppression de l’anode sacrificielle et élimine toute intervention de maintenance.
Dans certaines régions où l’eau est particulièrement calcaire, il arrive que la durée de vie d’un chauffe-eau électrique ne dépasse pas trois ans, ce qui engendre des coûts non négligeables. Nous serons bientôt en mesure de commercialiser des ballons d’eau chaude dont la durée de vie avoisinera 50 ans, ce qui est révolutionnaire !
La recyclabilité des réservoirs est-elle d’ores et déjà prouvée ?
Une fois broyés, nos réservoirs sont compatibles avec la technologie Thermosaïc développée par le CETIM-CERMAT et d’autres partenaires. Ce procédé actuellement en phase de pilote industriel permet de produire en continu des panneaux structurels à partir de déchets de composites thermoplastiques. En revanche, il n’est pas possible de recréer un réservoir à partir de ces déchets composites.
Durée de vie longue, recyclabilité… ce type de réservoir présente de nombreux atouts d’un point de vue environnemental. Y en a-t-il d’autres ?
En effet, nos produits sont conçus pour avoir un faible impact environnemental. En plus de la durée de vie longue et de la recyclabilité, cela se traduit par une fabrication locale et un sourcing européen des matières premières. Par ailleurs, ce procédé présente une autre particularité : il ne crée pas de déchets, car les résidus de bandes sont réutilisés en interne pour former de nouvelles bobines. Ainsi, 100 % de la matière première qui rentre est utilisée, ce qui est également un avantage économique, ces matériaux étant très techniques, donc assez coûteux.
Nous avons encore des pistes pour réduire notre impact environnemental, comme utiliser de l’électricité décarbonée pour le process, des polymères biosourcés ou encore des fibres de verre recyclées.
Comment envisagez-vous votre développement futur ?
Cette technologie a beau être mature, nous disposons encore d’une forte marge de progression, principalement au niveau de la pression et des volumes admissibles. Nous développons actuellement des réservoirs de plus de 1 000 litres et nous sommes confiants sur notre capacité à intégrer ce marché. Par ailleurs, nous sommes en recherche active de partenaires industriels pour développer de nouveaux produits plus adaptés techniquement et économiquement à leurs besoins.
Enfin, si nos réservoirs sont actuellement produits en Belgique, nous avons pour objectif d’ouvrir notre première usine française en 2021.
Réagissez à cet article
Vous avez déjà un compte ? Connectez-vous et retrouvez plus tard tous vos commentaires dans votre espace personnel.
Inscrivez-vous !
Vous n'avez pas encore de compte ?
CRÉER UN COMPTE