Réputée pour le prototypage et la production de pièces personnalisées ou complexes en petite et moyenne série, la fabrication additive se voit au fil du temps accorder un nouveau mérite : la confection de pièces de rechange, à des fins de remplacement de pièces défectueuses ou usées, empêchant le bon fonctionnement de mécanismes ou d’appareils complets. L’impression 3D deviendrait un facilitateur de la réparation, «maillon essentiel de l’économie circulaire» selon le rapport de l’Ademe publié en juin 2017 sur le thème. Car réparer, c’est allonger la durée d’usage des produits et réduire leurs impacts environnementaux, écrit-on dans ce même rapport.
Les deux initiatives les plus importantes en France sont à mettre au crédit du distributeur Boulanger et de l’industriel Seb, spécialiste de l’électroménager. La plateforme web Happy 3D de Boulanger, née le 1er juin 2016, a pour objectif de centraliser des fichiers 3D de pièces détachées et de les rendre accessible à tous. «Notre base contient aujourd’hui environ 500 modèles, de marque propre (EssentielB, Listo et Miogo, NDLR) ou internationale, détaille François Longin, chef de projet Happy 3D chez Boulanger. Il s’agit de pièces de type électrodomestique : poignée de réfrigérateur, trappe de télécommande… Elles sont imprimées exclusivement en plastique et peuvent être changées par l’utilisateur lui-même, sans qu’il ait à ouvrir l’appareil, car ce sont uniquement des pièces externes, non prévues pour le contact alimentaire.»
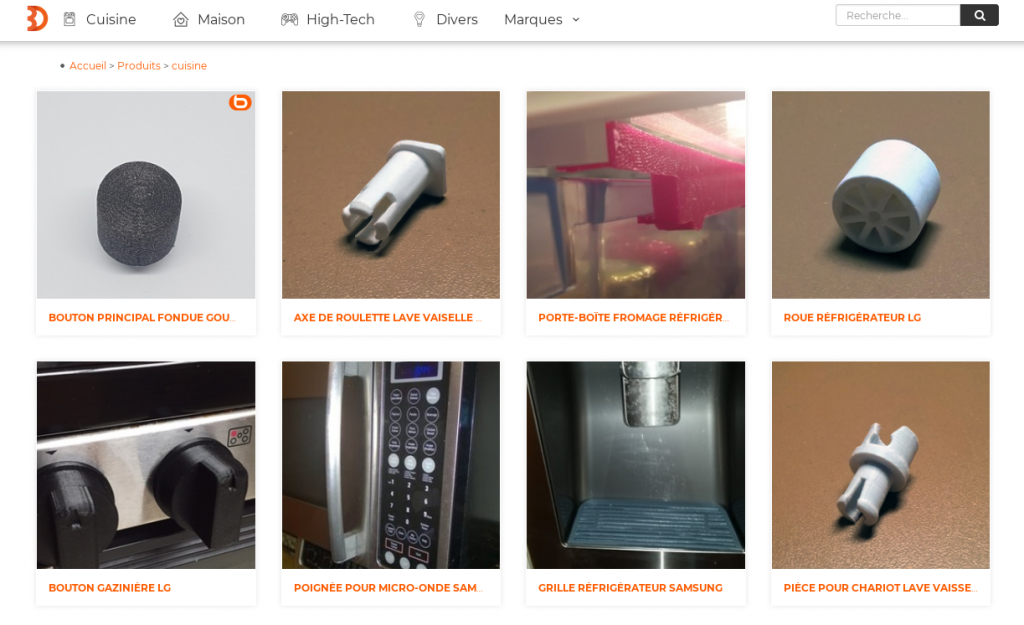
Puisqu’il est question d’autoréparation, le service après-vente de Boulanger n’est pas impliqué. La fabrication de la pièce est confiée à l’utilisateur lui-même, s’il détient une imprimante 3D, ou à Freelabster, le partenaire de Boulanger. Le distributeur joue l’intermédiaire entre les particuliers et la communauté des «makers», qui compte 2000 personnes. Les fichiers sont distribués en open source et Boulanger n’engrange aucune recette, s’engageant même à modéliser gratuitement les pièces de ses propres marques absentes de la base. «Il n’y avait pas d’enjeu économique» ajoute François Longin. Ce projet est d’abord l’occasion pour l’entreprise de promouvoir une étiquette éco-responsable auprès de clients actuels ou potentiels.
Remplacer des pièces qui n’existent plus
Un nombre croissant de consommateurs sont en effet sensibilisés à la sauvegarde de la planète. D’autres, plus pragmatiques, sont soucieux avant tout de préserver leur porte-monnaie et de prolonger l’usage de leurs équipements autant que possible. Le contexte législatif est de surcroît propice, en témoigne dernièrement la loi «Hamon» de 2014, votée pour favoriser la réparation. Ce sont autant d’opportunités pour le groupe Seb, qui a inauguré le label «Produit réparable 10 ans» en septembre 2016. L’impression 3D, déjà employée sur de nombreux sites internationaux pour le prototypage, est mise à contribution au début de l’année 2017 pour la production de pièces de rechange.
«Nous avons réalisé deux investissements pour le service après-vente sur notre site logistique de Faucogney-et-la-Mer (Haute-Saône), précise Nathalie Pécoul, chef de projet fabrication additive pour le groupe Seb. Ce site stocke l’ensemble des pièces détachées pour les marques du groupe (Calor, Moulinex, etc. ndlr), soit plus de 30000 références. Avec notre engagement de réparation pendant dix ans, des situations de sous-stock peuvent affecter des produits très anciens. Ces deux imprimantes 3D exploitant un procédé polymère assurent l’approvisionnement quand les pièces conventionnelles et leur moule ne sont plus disponibles.»
(((légende Seb imprimante 3D))))
Le projet n’est pas encore entré dans une phase industrielle. «Pour le moment, nous testons l’impression 3D auprès de nos consommateurs, au travers de notre réseau de réparateurs agréés, poursuit Nathalie Pécoul. Nous limitons cette expérimentation à la France pour le moment, afin d’obtenir un meilleur suivi des consommateurs. La pièce de rechange n’a pas toujours le même aspect que l’objet original, par exemple. Elle est toutefois systématiquement validée par nos équipes d’ingénieurs.»
Quelques entreprises locales, semblables à des réparateurs de proximité, avaient anticipé la tendance. Micro-entrepreneur dans les Côtes d’Armor et ancien prestataire de service dans le petit bricolage, Sébastien Rannou monte son affaire, Rannou 3D, dès 2015. Equipé aujourd’hui de quatre imprimantes 3D, il modélise et produit des pièces en plastique à destination des particuliers et des professionnels. Il insiste sur l’équation économique : «Je réalise de moins en moins de pièces pour le petit électroménager car ce n’est pas assez rentable. Ce sont des petits appareils qui cassent beaucoup et qui n’ont aucune valeur marchande.» Il est vrai que dans les catégories de biens à petit prix, le coût de l’opération et de la pièce n’incite pas à la réparation, mais plutôt au remplacement à neuf.
Beaucoup de freins à lever
Les commandes des professionnels ou sortant de l’ordinaire ont l’avantage d’être plus lucratives. «J’ai par exemple imprimé un petit engrenage que j’ai facturé une centaine d’euros. Cette pièce de rechange a évité le remplacement complet d’un système valant de 3000 à 4000 euros, poursuit-il. Pour le particulier, les pièces de piscine sont également intéressantes car très chères.» Il se refuse cependant à imprimer tout et n’importe quoi. «Une pièce imprimée en 3D est 25% moins résistante qu’une pièce moulée par injection, estime-t-il. Je ne travaille pas pour l’aéronautique ou l’automobile, à moins que ce ne soit un simple support de gaine. Grâce à mon passé dans l’automatisme industriel, j’ai acquis de bonnes connaissances mécaniques pour évaluer la faisabilité une pièce.»
Redoute-il des poursuites pour contrefaçon ? «Le client a le droit de réaliser la copie d’une pièce au titre de la réparation» rappelle Sébastien Rannou. C’est l’une des craintes exprimées par le secteur de la réparation et rapportée par l’Ademe. L’agence indique cependant que, pour la plupart, «les pièces détachées ne sont ni protégées ni protégeables par les droits de propriété intellectuelle» entre autres arguments en faveur de la réparation. D’autres freins plus significatifs sont relevés, dont le manque de compétitivité (prix de la matière, temps de fabrication…) et l’inadaptation de la technologie (propriétés mécaniques ou thermiques inférieures, etc). De gros progrès techniques sont à attendre avant que l’impression 3D ne devienne un outil de réparation omnipotent et omniprésent.
Frédéric Monflier
Réparation à haute précision pour moteur d’avion
Dans les filières industrielles à haute valeur ajoutée, les réparations, souvent critiques et onéreuses, n’en restent pas moins profitables car l’appareil ou l’équipement coûte lui aussi très cher. L’industrie aéronautique est un bon exemple : le spécialiste de la réparation de moteur, Chromalloy, se sert de la fabrication additive pour réparer des pièces de turbine Pratt&Whitney. Mieux encore, au bout de quatre cycles de réparation, la durée de vie des pièces (des joints) passe de 10000 à 50000 heures. La technique mise en œuvre fait appel à la déposition de métal par laser, inventée par l’entreprise française Beam.
Cet article se trouve dans le dossier :
Modéliser la microstructure des métaux pour en améliorer les performances
- Matériaux métalliques : quelles propriétés pour quelles applications ?
- La diversité des alliages métalliques : l'exemple des aciers
- « Diviser par 3 le temps de développement de nouveaux matériaux en remplaçant des expériences par des simulations »
- Les usages de l'acier dans l'industrie
- « Les approches classique et quantique sont complémentaires »
- La France structure le secteur de l’impression 3D Métal
- L'impression de pièces détachées cherche son modèle
- Les secrets structurels sous la loupe du numérique
- Les thèses du mois : Modélisation des microstructures et structures des matériaux
- Modéliser la microstructure des métaux pour en améliorer les performances
Dans l'actualité
- Quels matériaux pour quelles applications ?
- L’impression 3D est-elle écologique ?
- L’éco-conception au service de l’impression 3D
- L’impression 3D s’invite dans tous les secteurs
- Zero Standby Energy réduit à zéro la consommation des appareils en veille
- Une plateforme de vente pour les stocks dormants de pièces de maintenance industrielle
Dans les ressources documentaires