Basée en Nouvelle-Aquitaine, l’entreprise Guyenne Papier a mis au point un procédé d’enduction permettant de conférer au papier des propriétés telles que la thermoscellabilité, la résistance à l’eau, ou encore à la graisse. De quoi offrir une alternative aux plastiques, sans pour autant transiger sur la qualité de l’emballage.
Fruit de quatre ans de travaux de recherche et développement, le procédé d’enduction mis au point par l’entreprise tricentenaire Guyenne Papier fait appel à un ingrédient principal tout à fait naturel : l’eau. L’entreprise a également veillé à exclure toute substance controversée, comme les résines fluorées ou certaines nanoparticules. Déclinée en différents produits aux propriétés ciblées – barrière à l’eau, à la graisse, thermoscellabilité… –, cette gamme contient par exemple « Greenbee », un papier enduit 100 % biosourcé et compostable. Sans le moindre gramme de plastique, « Greenbee » se révèle thermoscellable, mais aussi capable d’arrêter la graisse, et peut ainsi être utilisé pour des applications telles que l’emballage de sachets de thé. Céline Procop, PDG de Guyenne Papier, nous en dit plus sur cette référence ainsi que sur les autres produits de la gamme, et revient également en détail sur leur mise au point.
Techniques de l’Ingénieur : Les origines de Guyenne Papier sont très anciennes. Quelle est l’histoire récente de l’entreprise ?
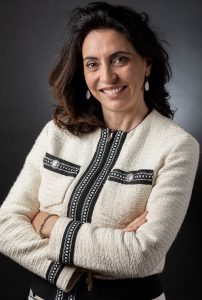
Céline Procop : Les origines du site industriel que nous occupons remontent effectivement à plus de trois cents ans. Nous avons fabriqué du papier jusque dans les années 80, période à laquelle la performance industrielle, l’ouverture des frontières, la capacité des Chinois à faire mieux que nous… nous ont obligés à nous re-concentrer sur un cœur de métier plus stratégique, et à monter en gamme. Nous ne sommes aujourd’hui plus un fabricant de papier, mais ce que l’on appelle un « coucheur-enducteur ». Nous achetons de la matière papier et nous la traitons en surface pour lui donner des propriétés particulières, qui ne peuvent pas être acquises sur une machine à papier directement en ligne de production et qui ne peuvent pas non plus être obtenues par un imprimeur en amont.
Après quatre ans de travail de R&D, vous avez abouti au développement d’un procédé d’enduction permettant de transformer un papier conventionnel en papier d’emballage. Quelles ont été les principales étapes de ce projet ?
L’industrie papetière s’est fait exclure du monde de l’emballage dans les environs des années 1980-90, puisque l’emballage plastique offrait soudainement plein de propriétés intéressantes : à la fois des propriétés de conservation, d’imprimabilité, de résistance ou d’étirement. Du coup, le monde papetier s’est réorienté plutôt vers la communication, l’art graphique. Bien avant cela, le papier faisait pourtant partie du quotidien en matière d’emballage. On se souvient tous des sacs en papier dans les magasins avant qu’ils soient remplacés par du plastique… Guyenne Papier a fabriqué des produits destinés à l’emballage pendant des dizaines d’années. Au fur et à mesure, nous nous sommes aperçus que les clients se faisaient de plus en plus rares.
Avec la loi AGEC¹, la Single use plastic directive², et plus globalement la prise de conscience de l’impact du plastique, qui n’est parfois pas bien recyclé, on a vu arriver un retour du papier pour l’emballage.
Le papier est certes joli et recyclable, mais c’est aussi une matière poreuse, pas thermoscellable… qui n’a donc pas toutes les caractéristiques d’un film plastique. Nous avons ainsi entamé il y a maintenant presque cinq ans un profond travail de R&D pour voir ce que nous pouvions faire, en tant que coucheur-enducteur, pour ajouter au papier un traitement de surface permettant de lui conférer des propriétés qu’il n’a pas au départ. Nous avons réussi à rendre notre matière papier thermoscellante, barrière à la graisse, à l’eau et à l’humidité. Tout cela à un niveau de performance qui, dans certains cas, est identique à celui des films plastiques.
Nous avons réussi à relever ce défi, qui, au départ, ne paraissait pas évident d’un point de vue technologique. D’autant plus que nous avons choisi dès le départ de ne pas aller vers le chemin le plus facile, c’est-à-dire de ne pas utiliser de produits chimiques controversés dans nos sauces d’enduction.
Quels sont ces produits controversés que vous évoquez ?
Il existe aujourd’hui des produits chimiques qui permettent d’arriver à des niveaux de performance intéressants, mais qui sont controversés. Nous évitons donc la résine fluorée, les procédés de type PVdC qui peuvent se révéler perturbateurs endocriniens, mais aussi les PVA, des nanoparticules qui peuvent se retrouver dans les rivières et les océans, ainsi que le polyéthylène, qui ferait que nos produits ne seraient pas mono-matériaux.
Nous n’avons donc pas choisi la route la plus simple, au contraire… C’est pour cela que nous avons eu besoin de temps. Mais aujourd’hui nous avons mis au point des produits qui ont des performances et des propriétés de barrière et de thermoscellabilité très diverses, pour différentes applications, et qui peuvent ainsi constituer des alternatives réelles et concrètes aux emballages plastiques.
Sans révéler de secret industriel, comment êtes-vous justement parvenus à donner au papier toutes ces propriétés ?
L’industrie a plein de ressorts et de capacités… En revanche, la pression du marché et les réalités économiques font que les industriels ne mettent pas forcément en avant leurs meilleurs produits, ou ceux qui sont le plus respectueux de l’environnement. Ça n’était en tout cas pas le cas à l’époque où nous avons lancé ce projet. Nous avons donc fait un gros travail de partenariat avec nos fournisseurs – fournisseurs de matière, fournisseurs de produits chimiques – pour qu’ils se donnent eux-mêmes du mal et ressortent de leurs tiroirs des produits qu’ils avaient inventés par le passé, mais qu’ils n’avaient pas voulu mettre en avant pour des problématiques de coût, de volume minimum etc. Nous avons donc pris le parti de réaliser une grande part du travail en partenariat avec nos fournisseurs. Il s’agissait de recherche appliquée en amont.
Concrètement, comment le procédé est-il mis en œuvre ?
J’ai tendance à donner cet exemple trivial, mais qui est très parlant : c’est comme étaler de la confiture sur une tartine… Nous achetons « le pain », c’est-à-dire le papier, et nous avons une grosse machine qui va venir étaler la « confiture » sur ce « pain ». Notre ingrédient de base est l’eau. Tous nos produits sont des mélanges de produits chimiques de natures diverses mélangés avec de l’eau, qui est le composant principal.
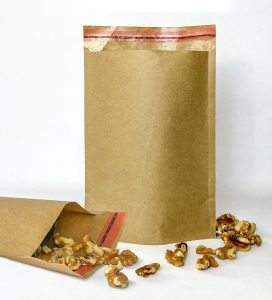
Quels produits avez-vous développés sur la base de procédé ? À quelles applications se destinent-ils ?
Le plastique est une matière fantastique… Pour arriver à être aussi bon que le plastique, c’est donc très compliqué. Il est en train de se passer quelque chose d’assez révolutionnaire en matière de consommation. Nous avons été habitués, en tant que consommateurs, à des produits avec un cahier des charges surqualitatif. Les biscuits, par exemple, n’étaient auparavant pas emballés dans des films plastiques. Si on ne les mangeait pas rapidement, ils ramollissaient… Aujourd’hui, si l’on achète des biscuits, non seulement ils sont contenus dans une boîte en carton, mais en plus ils sont emballés dans un film plastique, qui permet des DLC [dates limites de consommation, n.d.r.] de plusieurs mois. Cette dynamique est, dans certains cas, surqualitative. Nous avons donc découpé notre gamme de produits [baptisée Sunibarrier, n.d.r] pour cibler certaines propriétés d’importance. Dans certains cas, il faut une barrière à l’humidité très importante. C’est ce qu’offre notre produit appelé « Ladybee », qui permet des DLC importantes. Il a aussi une propriété intéressante : sa thermoscellabilité est très importante. Cela est très avantageux pour les industriels sur les lignes d’emballages, car cela permet le maintien des cadences.
Un autre produit de notre gamme, « Universalbee », permet quant à lui d’emballer des matières liquides ou humides et même du gras : barquettes de salade, de carottes râpées, gobelets… Ce que « Ladybee » n’est pas capable de faire.
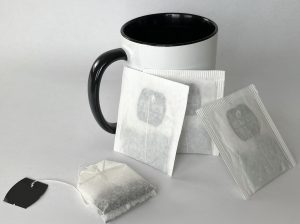
Enfin, le produit « Greenbee » bénéficie quant à lui d’un traitement de surface basé sur une molécule que l’on retrouve telle quelle dans la nature. Ce produit 100 % biosourcé est ainsi parfaitement biodégradable et possède des propriétés de barrière à la graisse et de thermoscellabilité. Il est adapté à des utilisations courtes ou immédiates, par exemple le papier d’emballage de charcuterie ou de sachets de thé. Il se jette dans le bac jaune et peut même être composté.
Quid, justement, de la recyclabilité de ces différents produits ?
Aujourd’hui, tous les papiers complexés avec du polyéthylène – c’est globalement 90 % de ce que l’on trouve quand on a un emballage papier – sont des perturbateurs de tri. Ils sont aussi gênants pour les fabricants de papier recyclé, qui se retrouvent en effet avec des chaînes longues de polymères qui perturbent leurs procédés de broyage de fibres. Même si les papiers complexés avec du polyéthylène sont dits recyclables, ce ne sont quand même pas des produits très bien accueillis par les recycleurs.
Nos produits, à l’inverse, sont tout simplement entièrement solubles dans l’eau. Contrairement au polyéthylène, nos chaînes de polymères sont très courtes, leur dégradation dans l’eau est donc immédiate. Les particules sont récupérables dans des filtres : on est au-dessus de la nanoparticule, ce qui évite leur disparition dans les eaux des stations d’épuration, mais on est bien en-dessous des chaînes de polymères de polyéthylène.
En matière de coût, où vos produits se situent-ils ?
C’est forcément beaucoup plus cher… Indiscutablement. Nous offrons une solution alternative qui, à ce jour, ne pourra pas remplacer d’office tous les volumes d’emballage réalisés à partir de plastique. Il me semble toutefois y avoir une remise en question à faire, à plein d’égards, sur la manière dont on fabrique et dont on emballe aujourd’hui les produits. C’est un travail collaboratif à mener à la fois avec les transformateurs et les emballeurs finaux. Il y a en effet certainement des optimisations à faire en matière d’emballage. C’est-à-dire que là où aujourd’hui deux types d’emballages se cumulent, nos produits peuvent peut-être permettre de se passer de l’un des deux.
Au-delà de ce projet aujourd’hui abouti, avez-vous prévu d’autres travaux de R&D ?
Oui, bien sûr ! On n’en est aujourd’hui qu’au début de ce que l’on peut découvrir. On a certes des produits qui sont au point, qui sont commercialisés et qui font l’affaire. Au fur et à mesure de l’avancée des choses, nous sommes toutefois confrontés à de nouvelles exigences qui nous permettent de réfléchir à de nouveaux produits.
Nous sommes par exemple en train de sortir une quatrième sous-gamme, un papier « Thermobee », dont la seule ambition est d’être thermoscellant avec une petite barrière à l’eau et qui justement est un produit de volume, dont le modèle économique est plus favorable encore et qui est parfait pour remplacer le papier complexé avec du polyéthylène.
Au-delà du travail de développement et de mise sur le marché de vos produits, vous vous consacrez également à certains engagements… Pouvez-vous nous en dire plus à ce sujet ?
Nous avons un engagement très fort notamment en faveur de l’industrie dans sa globalité. C’est en effet grâce à l’industrie, en France, que l’on peut envisager une certaine autonomie, grâce à des produits qui peuvent faire une vraie différence. Je suis une grande amoureuse de l’industrie pour toutes ces raisons. Je suis donc ravie que l’industrie soit en passe de retrouver ses lettres de noblesse.
Nous avons ainsi des engagements à plusieurs niveaux. Je pars tout d’abord du principe qu’une entreprise doit être poreuse à son environnement immédiat, dans la ville ou le village où elle est située. Nous faisons donc beaucoup de choses en collaboration avec des artistes locaux, des associations…
Plus globalement, nous soutenons des associations telles que Globice et Chelonia, qui se consacrent à la protection de l’environnement, et plus particulièrement à celle des baleines et des tortues. Ces espèces sont en effet directement touchées par la problématique du plastique. Je tiens toutefois à ne pas le décrier, à ne pas opposer les choses, car je pense que le plastique aura toujours sa place parmi nous, mais dans des proportions peut-être plus raisonnables.
Il nous semble en tout cas important de montrer qu’il peut y avoir des produits alternatifs.
[1] Loi anti-gaspillage pour une économie circulaire
[2] Directive sur les plastiques à usage unique : depuis juillet 2021, une directive européenne interdit de mettre sur le marché des pailles, des assiettes ou encore des couverts en plastique à usage unique au sein de l’UE.
Réagissez à cet article
Vous avez déjà un compte ? Connectez-vous et retrouvez plus tard tous vos commentaires dans votre espace personnel.
Inscrivez-vous !
Vous n'avez pas encore de compte ?
CRÉER UN COMPTE