L’étude de la microstructure des matériaux métalliques et leur modélisation constituent une thématique de recherche prépondérante pour mieux comprendre le comportement des matériaux à l’échelle micronique.
Alphonse Finel (Département Matériaux et Structures, ONERA et Laboratoire d’Etude des Microstructures, ONERA-CNRS) et Mikael Perrut (Département Matériaux et Structures, ONERA) sont chercheurs à l’ONERA dans le domaine des matériaux et structures. Responsables au sein de ce domaine de la thématique « Physique des comportements : de l’atome à la microstructure », les deux chercheurs développent des modèles de simulation du comportement de matériaux métalliques subissant des contraintes mécaniques et de températures, afin de mieux comprendre la détérioration de leurs propriétés avec le temps. Leur but est de simuler et de modéliser ces phénomènes le plus finement possible, afin de développer des alliages plus performants, et de limiter les expérimentations, au profit de la modélisation, pour mieux connaître le comportement des matériaux sous contraintes.
Alphonse Finel et Mikael Perrut ont expliqué aux Techniques de l’Ingénieur comment ces modélisations sont développées, et ce qu’elles nous apprennent sur le comportement des matériaux métalliques à l’échelle du micron.
Techniques de l’Ingénieur : Présentez-nous les recherches sur lesquelles vous travaillez au sein de l’ONERA ?
Alphonse Finel et Mikael Perrut : Nos recherches portent sur la modélisation, pour comprendre et prédire le comportement de matériaux métalliques qui résistent à suffisamment haute température et avec des contraintes mécaniques importantes.
Le but étant de recréer les conditions d’utilisation de pièces mécaniques, comme celles subies par les matériaux dans les parties les plus chaudes des moteurs d’avions. Nous travaillons donc sur des matériaux métalliques ayant un comportement maîtrisé sous haute température et sous contrainte. Pour maîtriser le vieillissement et le comportement de ces matériaux à haute température, il faut comprendre comment le matériau se comporte à une échelle très réduite, de l’ordre du micron.
Quelle est la structure de ces matériaux, qui sont tous des alliages métalliques ?
Ces matériaux sont multi-constitués (constitués de plusieurs types d’atomes), au minimum de 5 ou 6 métaux différents. Si on prend l’exemple des superalliages à base de nickel, ils sont majoritairement constitués de nickel et contiennent également de l’aluminium ainsi que d’autres métaux, parfois dans des proportions très faibles.
Ces matériaux sont également multiphasés : la distribution locale des différentes espèces atomiques n’est pas homogène. Cela crée une hétérogénéité spatiale, qui est une des composantes principales nous permettant de contrôler les propriétés mécaniques du matériau. C’est cette hétérogénéité que nous cherchons à modéliser, à générer.
Comment vous y prenez-vous ?
Pour illustrer notre démarche, prenons l’exemple d’un superalliage à base de nickel, dont voici ci-dessous l’image obtenue par microscopie électronique, à l’échelle du micron :
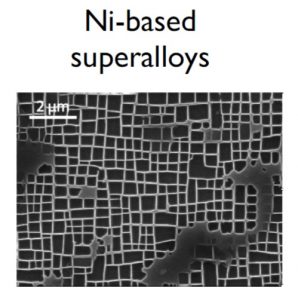
Les zones noires et blanches représentent les hétérogénéités du matériau. Les phases noires sont plus pauvres en nickel et plus riches en aluminium, la phase blanche, visible sous forme de ligne, est quant à elle riche en nickel et pauvre en aluminium.
Que dit cette hétérogénéité quant au comportement du matériau en question ?
Cette hétérogénéité, visible sur l’image, est souhaitée, car elle assure au matériau résistance et ductilité. Le matériau sur cette image est utilisé pour fabriquer des aubes de turbines destinées à équiper des avions. Il est donc soumis à des conditions extrêmes de température et de sollicitations mécaniques lors de son fonctionnement. Sur cette image, le matériau n’a pas encore été soumis à ces conditions.
Ces contraintes déforment les matériaux. Physiquement, cette déformation s’opère par le glissement d’objets qu’on appelle des dislocations. Quand on applique une pression sur un matériau, les dislocations qu’il contient vont se mettre à glisser : c’est ce phénomène qui va déformer le matériau.
Pour limiter la déformation, il va falloir mettre des obstacles sur le chemin que prend cette dislocation au sein du matériau. Ces obstacles sont les interfaces entre les différentes phases du matériau, en noir et blanc sur l’image. Ces dislocations, qui vont pour l’essentiel passer par les zones blanches visibles sur l’image, ont donc un potentiel de propagation réduit, du fait de la proéminence des zones noires. Ces nombreux obstacles aux dislocations rendent donc le matériau plus résistant mécaniquement, il se déforme moins.
Pourquoi dans ce cas ne pas développer des matériaux constitués uniquement de cette phase noire ?
Le matériau résultant serait fragile. Bloquer l’ensemble des dislocations revient à créer très rapidement des fissures dans le matériau. Ici, la présence de deux phases, dont l’une ductile, permet de moduler la ductilité globale, les interfaces entre les phases permettant de limiter le glissement des dislocations. La ductilité est en fait une propriété qu’il faut maîtriser, car un matériau trop ductile, qui se déforme trop, ne conviendrait pas non plus pour l’usage industriel que l’on en fait. Il est nécessaire de trouver un compromis, un équilibre, entre résistance et ductilité.
Comment va évoluer la microstructure de ce matériau sous contraintes ?
Sous l’action des températures et de la contrainte, les atomes composant la structure du matériau vue dans l’image ci-dessus – composant l’aube de turbine d’un avion – vont bouger.
La microstructure (image n°1) que nous voyons à l’image, qui est celle souhaitée pour résister aux contraintes, va changer et être dégradée. Et si on laisse cette structure se dégrader suffisamment, le matériau va acquérir la structure que l’on peut observer sur cette autre image obtenue (image ,°2, ci-dessous) par microscopie électronique : la distribution des phases a complètement changé. Et les propriétés mécaniques du matériau également.
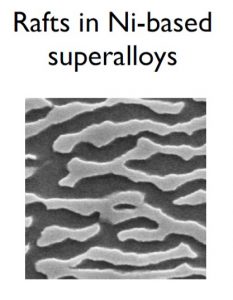
Cette évolution de la microstructure du matériau est en soi inévitable et irréversible, au vu des contraintes qu’il subit. Ce qui est possible par contre, c’est de ralentir ce processus, de la freiner. Pour faire cela, il nous faut donc comprendre quels sont les mécanismes et les forces motrices qui font passer la microstructure du matériau de la première à la seconde image.
C’est cette évolution que vous cherchez à modéliser ?
Exactement. La démarche de l’ONERA est d’essayer de décrire les équations cinétiques que les atomes suivent quand la température est haute et que l’on impose des contraintes au matériau. Le problème qui se pose alors est la quantité astronomique d’atomes en jeu. Il est impossible de modéliser cela. C’est pour cela que nous avons décidé de travailler directement à l’échelle du micron (c’est l’échelle utilisée pour les images illustrant cet article), en oubliant les atomes et les équations qui les gèrent. Il nous faut donc inventer de nouvelles équations, les développer ; c’est la finalité des recherches que nous menons sur ce thème.
Pour faire cela, nous allons prendre en compte non pas des atomes de manière individuelle mais par paquets, en étudiant des champs de concentration de chacune des espèces atomiques, et d’autres champs, qui décrivent comment les atomes sont rangés les uns par rapports aux autres, mais sans pour autant considérer explicitement ces atomes. Notre but va être de développer des méthodes pour trouver les équations décrivant le comportement de ces champs, directement à l’échelle mésoscopique.
Quel est l’aboutissement de ce travail ?
Nous avons mis au point une modélisation, appelée PFM (Phase Field Method, méthode des champs de phase). C’est l’un des outils que nous développons à l’Onera.
La modélisation en 3D représentée ci-dessous est celle du matériau que l’on peut observer sur l’image 1. Ce matériau, constituant l’aube de turbine, est ici modélisé avant l’application des contraintes :
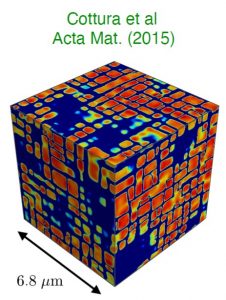
Les deux grands ingrédients de la physique utilisés pour cette modélisation sont la thermodynamique – réversible et irréversible -, et les phénomènes de déformations élastiques. Cette déformation élastique est due aux variations spatiales des champs de concentration qui, associées aux différences de volume atomique, vont déformer la matrice du matériau sur une très longue portée. Aussi la déformation est anisotrope, l’amplitude de la déformation va donc être différente selon la direction ou elle se propage.
Nous avons ajouté dans notre modèle cette déformation, qui permet d’obtenir l’image 3D présentée ici.
Les deux avantages de cette modélisation sont tout d’abord la possibilité de voir l’évolution de la structure au cours du temps, ce qui n’était pas possible auparavant. Second avantage, la possibilité d’ajouter ou d’enlever certaines forces motrices à notre simulation, pour voir quels sont leurs effets relatifs sur la structure du matériau et sa déformation.
Qu’est ce qui fait que la microstructure est aussi perturbée sur le long terme, et que l’on passe d’un quadrillage régulier à une structure totalement différente ?
Ce que l’on constate, c’est que l’une des forces motrices importantes opérant sur la microstructure des matériaux, à haute température, est le déplacement des dislocations. Ces dislocations vont avoir un mouvement limité – grâce à la structure en quadrillage – qui va entraîner une redistribution des atomes dans la structure. Nous avons ajouté à notre modèle cette plasticité, qui nous a permis d’aboutir à ce type de modélisation, figurant la structure du matériau après contraintes :
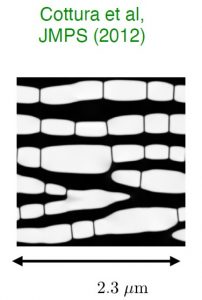
En comparant à l’image obtenue par microscopie électronique (image 2), on voit que les forces que nous avons prises en compte sont bien celles qui déforment la structure. Bien que ce modèle doit être encore amélioré, il montre que les phénomènes qui gouvernent le vieillissement des matériaux sont aujourd’hui identifiés.
Une des applications qui découlerait de ces modèles est la prédiction de la composition exacte des alliages à développer pour obtenir le comportement attendu du matériau en question, en remplaçant, en partie, l’expérience par la modélisation.
Cela dit, il n’est pas question de substituer l’expérimentation par la modélisation. Notre objectif, à l’ONERA, est de diviser par 2 ou 3 le temps de développement de nouveaux matériaux, en diminuant le nombre d’expérimentations grâce aux simulations. Sans oublier que la validation expérimentale reste une étape fondamentale de la recherche.
Quelle est votre stratégie pour améliorer encore ces modélisations ?
Aujourd’hui, nous développons d’autres démarches, en utilisant des bases de données et du machine learning, pour ajouter les possibilités offertes par les techniques d’intelligence artificielle (IA) à nos modèles. Cela permettra d’alimenter et d’accélérer le développement de nos modèles.
L’IA nous permet d’accélérer de plusieurs ordres de grandeurs nos calculs, mais aussi de coupler les échelles. C’est un point fondamental, puisque le modèle que nous venons de présenter s’applique à une échelle qui reste très petite par rapport à la taille des pièces industrielles dont nous voulons connaître le comportement. Les développements actuels extrêmement rapides de l’IA et du machine learning vont nous permettre de faire nos simulations à différents endroits de la pièce mécanique que nous voulons étudier. C’est ce changement d’échelle – de l’échelle micronique à l’échelle centimétrique – que les techniques d’IA vont nous permettre d’opérer, dans les années qui viennent, et permettre ainsi d’opérer une rupture dans nos capacités de prédiction à l’échelle des pièces industrielles utilisées dans les avions ou les hélicoptères.
Propos recueillis par Pierre Thouverez
Source des illustrations utilisées dans cet article :
- Gaubert, Modélisation des effets de l’évolution microstructurale sur le comportement mécanique du superalliage monocristallin AM1. Ph.D. Thesis, Mines ParisTech (2009).
- M. Cottura, Y. Le Bouar, A. Finel, B. Appolaire, K. Ammar, S. Forest, A phase field model incorporating strain gradient viscoplasticity: Application to rafting in Ni-base superalloys, J. Mech. Phys. Solids, 60 (2012).
Crédit image de une : ONERA
(1) Échelle de grandeurs entre l’échelle mascroscopique et l’échelle nanométrique
Réagissez à cet article
Vous avez déjà un compte ? Connectez-vous et retrouvez plus tard tous vos commentaires dans votre espace personnel.
Inscrivez-vous !
Vous n'avez pas encore de compte ?
CRÉER UN COMPTE