[Médailles de l’innovation CNRS] Figurant parmi les quatre lauréats 2022 des Médailles de l’innovation décernées par le CNRS, Denis Spitzer a développé deux procédés permettant de produire des particules d’une taille inférieure au micron. Une technologie dont les applications les plus pertinentes se destinent notamment à l’industrie pharmaceutique, mais aussi au secteur de la transition énergétique.
Actuel directeur du laboratoire NS3E (Nanomatériaux pour les systèmes sous sollicitations extrêmes – CNRS/Institut franco-allemand de recherches Saint Louis/Université de Strasbourg), Denis Spitzer est à l’origine de deux procédés baptisés SFE et SFS, pour spray flash evaporation et spray flash synthesis. Permettant respectivement la formation et la synthèse de particules sub-micrométriques, ces approches novatrices se révèlent économiques, sûres et respectueuses de l’environnement. Parallèlement à la mise au point des procédés eux-mêmes, Denis Spitzer et son équipe ont également développé une expertise de pointe en matière d’étude mécanistique du SFE et du SFS, consistant, en substance, à mesurer la taille et de la vitesse des gouttelettes produites. Le chercheur parvient également, grâce à une approche unique combinant techniques de spectroscopie RAMAN et techniques de microscopie à force atomique, à réaliser une caractérisation dite « offline » des particules, c’est-à-dire à en analyser la structure après formation. Autant de percées qui amènent désormais les procédés SFE et SFS sur la voie de l’industrialisation, notamment pour des applications en pharmaceutique et dans le domaine de la transition énergétique. Denis Spitzer nous retrace les grandes étapes qui ont permis la mise au point de ces procédés novateurs. Il nous en révèle également les principes et intérêts majeurs.
Techniques de l’Ingénieur : Comment avez-vous abouti à la mise au point des deux procédés qui vous ont valu cette Médaille de l’innovation ? Quelles ont été les grandes étapes de votre parcours ?
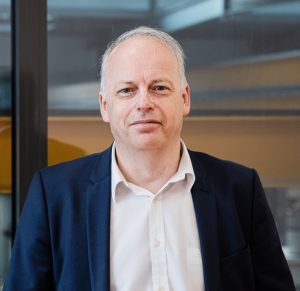
Denis Spitzer : Je suis, au départ, ingénieur chimiste en matériaux. J’ai fait une thèse en physique des explosifs. Je viens en effet du secteur de la défense. L’institut dans lequel j’ai fait ma thèse était déjà celui dans lequel je travaille aujourd’hui : l’Institut franco-allemand de Saint-Louis, dédié notamment à la défense. J’ai quitté l’institut pendant sept ans, pour faire du transfert de technologies : je montais des projets avec des industriels. Je suis retourné à l’Institut de Saint-Louis en 2000. J’ai alors commencé à travailler sur la réduction des tailles de particules, au départ principalement à destination des explosifs. L’intérêt était d’avoir des explosifs moins sensibles, moins dangereux à la manipulation. D’autres découvertes ont ensuite découlé de cette possibilité de faire des particules très fines ; certaines ont d’ailleurs été classifiées, et je ne peux pas en parler.
Je peux toutefois dire qu’il existe un parallèle entre les explosifs et la pharmacie. On a des composés comme la nitroglycérine ou la pentrite qui sont des explosifs très connus et qui sont, au départ, des molécules développées plutôt à des fins médicamentaires, pour faire notamment de la vasodilatation. On s’est rendu compte, souvent accidentellement, qu’utilisées en grandes quantités, ces molécules pouvaient détoner. Les explosifs que l’on utilise aujourd’hui encore dans les missiles ont ainsi, en fait, été découverts par hasard. Mais ces molécules que sont la pentrite ou la nitroglycérine sont encore utilisées dans les médicaments destinés à traiter des pathologies cardiaques. Mes collègues et moi avons commencé, en 2008, à développer des procédés de submicronisation, destinés à produire en continu des particules fines. Nous avons donc commencé avec des explosifs, mais nous nous sommes vite rendu compte que l’on pouvait faire cela également avec des médicaments.
Un premier procédé a ainsi été mis au point : le SFE, pour spray flash evaporation. J’ai ainsi reçu, en 2015, un Grand prix de l’Académie des sciences. Il s’agit d’un procédé de cristallisation de particules de taille très fine. On ne fait toutefois pas de synthèse : les molécules utilisées en entrée du procédé sont simplement obtenues à la sortie sous forme de particules plus fines que dans les procédés classiques.
Nous avons ensuite étendu ce procédé à de la synthèse. Au lieu de ne pas faire interagir les molécules de départ, on les fait réagir les unes sur les autres, afin de faire de nouvelles molécules. On entre ici dans le domaine de ce que nous avons appelé le SFS, pour spray flash synthesis.
Quels sont les principaux intérêts des procédés que vous évoquez, et comment fonctionnent-ils ? Comment sont-ils mis en œuvre, très concrètement ?
En permettant de faire des particules fines, le premier procédé, le SFE, trouve un intérêt particulier dans les médicaments : ils se dissolvent plus facilement, sont davantage biodisponibles et donc plus efficaces à moindre dose. Le SFS quant à lui, qui implique une synthèse, rend possible l’obtention de particules fines, mais permet également de diminuer les températures de synthèse, de réduire le nombre d’étapes, ou encore évite que les particules ne recroissent. Cela permet de produire des particules aussi bien organiques qu’inorganiques, avec ainsi un intérêt majeur pour la transition énergétique. Nous sommes en train d’explorer la synthèse d’oxydes, de céramiques, à destination des cellules solaires, des batteries, des piles à combustible. On ouvre vraiment en ce moment l’étendue des possibilités, ce qui complique bien entendu les choses ! (Rires)
Que ce soit le procédé SFE et SFS, les équipements nécessaires à leur mise en œuvre sont relativement semblables. Leur point commun réside dans le spray flash. Les molécules que l’on ne veut pas modifier dans le SFE, ou les molécules que l’on veut faire réagir pour le SFS, au départ, sont dissoutes dans un solvant. Cette solution est mise sous pression avec de l’azote, à hauteur de 10 à 60 bars. Cette solution est ensuite injectée à travers une buse de spray, dans une chambre d’atomisation qui, elle-même, est maintenue sous vide par une pompe. Pour donner une image, on peut se représenter la lance d’un Kärcher que l’on actionnerait dans une enceinte sous vide.
La chambre d’atomisation est maintenue à environ 5 millibars par les pompes. Comme la solution passe d’une surpression de l’ordre de 40 bars en moyenne à une pression très basse de 5 mbar, on va avoir une détente extrêmement rapide, qui va induire une évaporation du solvant elle aussi très rapide. Le composé dissous va ainsi se solidifier, sous forme amorphe ou cristalline, mais en tout cas sous forme de particules très, très fines. Des procédés concurrents comme le spray drying se déroulent quant à eux dans une chambre à pression atmosphérique, ce qui produit des gouttes d’environ 15 microns. Ce qui se produit avec notre procédé est que les gouttelettes explosent et se fragmentent avant de se solidifier. On atteint ainsi des tailles de gouttelettes, avant évaporation, de l’ordre de 500 nanomètres à 1 micromètre. Comme les gouttelettes avant évaporation sont plus petites, on obtient des particules solides elles aussi plus petites, entre 5 nanomètres et un micron. C’est l’avantage principal du SFE et du SFS.
En ce qui concerne le SFS, la synthèse se fait soit en envoyant des mélanges de molécules devant réagir entre elles par une seule buse, soit en mélangeant deux sprays, via deux buses dont les jets se croisent dans la chambre d’atomisation. Le fait d’avoir des gouttes très petites permet de contrôler les synthèses de manière très fine. La technique permet également l’abaissement des températures de synthèse. Par exemple, certaines céramiques sont obtenues par les techniques classiques à une température de 1 500°C. Avec notre approche, cette température chute à 800 ou 1 000°C.
En matière d’installations, ce que nous avons pour l’instant au laboratoire tient dans une pièce.
On a d’abord de petits réservoirs dans lesquels les solutions sont pressurisées. Ce sont des réservoirs qui font entre 1 et 5 litres. Les chambres d’atomisation font quant à elles de 2 à 100 litres. On a ensuite des filtres permettant de capter les particules, dont le diamètre va de cinq centimètres pour les plus petits, avec une hauteur de quinze centimètres, jusqu’à des filtres d’une quinzaine de centimètres de diamètre pour quatre-vingts centimètres de haut. En amont de cela, on a des pompes, qui sont de plus en plus grandes… Pour augmenter la production, il faut en effet soit augmenter la taille de l’orifice des buses, soit faire du multi-buses. On a alors besoin de pompes capables de maintenir le vide dans la chambre malgré le spray, par exemple, d’un litre et demi de solvant à la minute. Dans l’industrialisation, et c’est ce sur quoi nous travaillons actuellement, les choses seront toutefois un peu différentes de ce que l’on fait en laboratoire : on va condenser davantage le solvant avant les pompes, pour ne pas devoir investir dans des machines trop monstrueuses. Malgré tout, les pompes peuvent ressembler à de véritables stations de pompage.
Nous avons aujourd’hui atteint des capacités de production en laboratoire de cinq cents grammes par heure. L’industrie étudie quant à elle la possibilité d’atteindre deux à dix kilogrammes par heure.
Quel chemin reste-t-il à parcourir pour industrialiser ces procédés ? Sur quelles étapes travaillez-vous actuellement ?
Nous sommes en train de travailler sur deux aspects en laboratoire. Nous tentons de lever des verrous d’industrialisation. Nous travaillons par exemple sur la filtration : filtrer des particules de cette taille n’est pas simple… Nous travaillons aussi sur l’aspect lié aux réservoirs pressurisés. Quand nous avons commencé à travailler sur l’industrialisation du procédé, nous nous sommes rendu compte que l’on ne pouvait pas, lorsque l’on veut faire du continu, se limiter à de très gros réservoirs pressurisés. Deux aspects posent en effet problème : les gros réservoirs pressurisés sont très onéreux, mais ont aussi une contenance finie et ne permettent donc pas de travailler en continu. Il faut les remplir régulièrement. Nous avons trouvé l’astuce en alimentant le réservoir pressurisé par une pompe de gavage, un peu comme celle que l’on peut trouver dans un moteur diesel pour alimenter le système d’injection. Cette pompe de gavage alimente le réservoir pressurisé en pompant la solution qui se trouve à pression atmosphérique. On peut ainsi alimenter en continu le dispositif.
Un autre aspect sur lequel nous travaillons au laboratoire est celui de l’étude mécanistique du SFE et du SFS. Nous mesurons les tailles et les vitesses des gouttes par diffusion dynamique par laser. Nous étudions également une quinzaine de solvants différents, afin d’être en mesure, pour un composé que l’on souhaite sub-microniser, de choisir le bon solvant permettant d’obtenir exactement la taille de particule souhaitée. Nous mesurons également la taille des particules au moment où elles naissent dans le système.
À ces mesures en direct s’ajoute tout un aspect de caractérisation offline, qui consiste à analyser la structure des matériaux une fois qu’ils sont synthétisés ou élaborés par SFE. Nous avons pour cela monté des techniques de spectroscopie RAMAN couplées à des techniques de microscopie à force atomique qui sont tout à fait uniques.
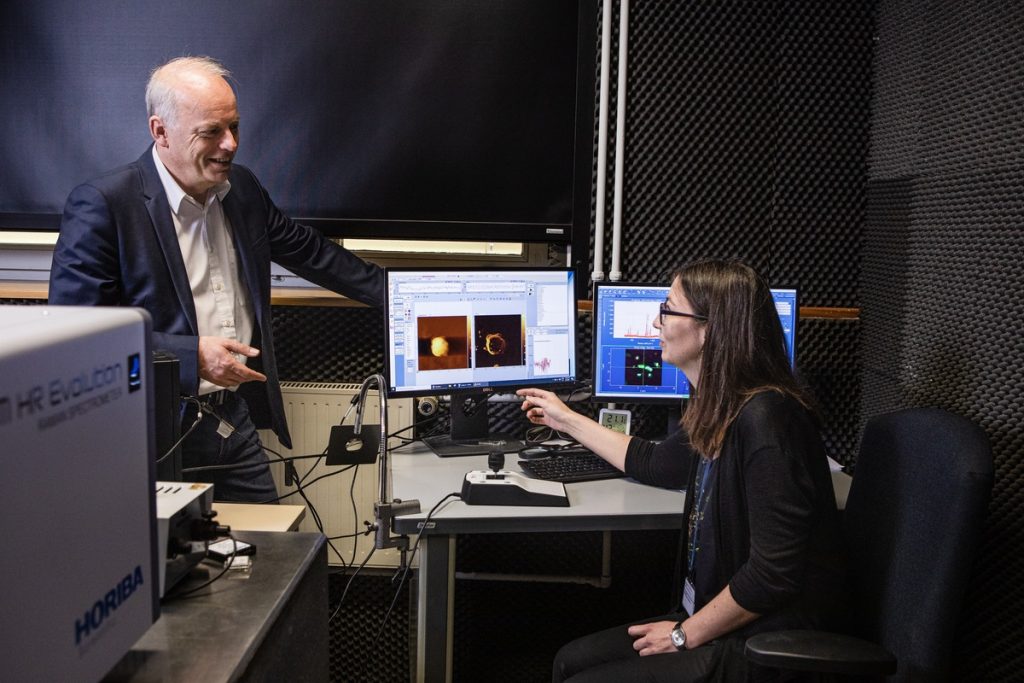
Quelles sont les perspectives d’application des procédés que vous avez développés ?
Un exemple d’application est celui des cellules solaires. On nous demande actuellement de faire des particules d’une taille de 800 nanomètres, à plus ou moins 100 nanomètres près. Les producteurs de cellules solaires cherchent en effet à en augmenter le rendement de conversion, qui plafonne à 25 %. Quand le soleil atteint les cellules, des séparations de charge se produisent sur les particules qui composent ces cellules. Les fabricants se sont rendu compte que pour éviter une recombinaison des charges trop rapide, il faut des particules d’environ 700 à 800 nanomètres. La taille actuelle des particules explique ce plafonnement du rendement aux alentours de 25 %.
La force du SFE et du SFS est leur polyvalence, leur versatilité. On peut donc avoir bien d’autres applications, dans la pharmacie, la transition énergétique… mais nous devons choisir des priorités. Nous sommes aujourd’hui très sollicités par des spécialistes de la transition énergétique. J’ai des sollicitations quasiment tous les jours dans le domaine des batteries, des piles à combustible… Il faut donc arriver à suivre !
Les phases de prématuration permises par le CNRS nous ont justement permis de comprendre que le domaine pharmaceutique était le plus porteur pour le SFE, et qu’il ne fallait pas se lancer dans l’agroalimentaire ou la cosmétique par exemple, faute de valeur ajoutée. La rupture technologique que l’on pouvait apporter n’était pas aussi intéressante.
Actuellement, nous avons un deuxième projet de prématuration pour étudier l’intérêt du SFS. Nous commençons à sélectionner les objectifs les plus stratégiques à traiter.
Nous avons aussi, en quelque sorte, bouclé la boucle, en trouvant des applications possibles du SFE et du SFS dans le domaine de la défense. Nos technologies sont d’ailleurs fortement poussées par la DGA¹ et le ministère des Armées, ne serait-ce que par les capacités de métrologie rapide que l’on développe. S’ajoutent à cela les oxydes et les céramiques, qui peuvent être intéressants d’un point de vue défense pour des aspects liés à la protection, au blindage, mais aussi, à nouveau, à l’énergie. Nous travaillons ainsi sur des compositions pyrotechniques – des nanothermites – qui sont des mélanges d’oxydes et de métaux brûlant extrêmement vite. Ils brûlent d’autant plus vite que les particules sont fines. Cette dualité entre défense et civil m’intéresse beaucoup. C’est souvent comme cela : les choses avancent aux frontières des domaines, et la pluridisciplinarité que nous avons à l’Institut de Saint-Louis, qui regroupe des chimistes, des aérodynamiciens, des mathématiciens… permet vraiment de faire avancer la recherche. Nous travaillons aussi avec une quinzaine de laboratoires extérieurs pour réaliser des tests de batteries, de cellules solaires, ou encore des tests autour de la photocatalyse. On ne peut pas tout faire tout seul, le développement des collaborations est important.
Quand on essaye de valoriser, il faut à la fois se laisser de la liberté pour faire de la recherche, continuer à faire des choses qui a priori n’intéressent personne… Si l’on veut valoriser, il faut tout de même structurer un moment donné. Comme je l’évoquais tout à l’heure, j’ai eu, après ma thèse, l’opportunité de faire du transfert de technologie. Je montais donc des projets pour des industriels. Ce qui me frustrait un peu était toutefois de ne pas pouvoir mener moi-même les projets. J’ai ainsi gardé, inconsciemment sans doute, le souci que la recherche serve un jour. Cela peut faire débat, mais pour moi, toute recherche fondamentale sert un jour. Je suis toujours surpris des possibilités de valorisation de la recherche, et cela me conforte dans ma position. Je trouve cela fantastique. J’ai d’ailleurs beaucoup appris en échangeant avec les autres lauréats de ces médailles de l’innovation du CNRS.
¹ Direction générale de l’Armement
Réagissez à cet article
Vous avez déjà un compte ? Connectez-vous et retrouvez plus tard tous vos commentaires dans votre espace personnel.
Inscrivez-vous !
Vous n'avez pas encore de compte ?
CRÉER UN COMPTE