Un véritable « changement de culture ». C’est ainsi que Pierre Bollard décrit le virage opéré en 2019 par l’entreprise qu’il dirige aujourd’hui depuis 20 ans : Spurgin Leonhart. Alors qu’elle misait exclusivement, depuis sa création en 1978 en Alsace, sur le développement de produits en interne, la société familiale spécialiste des produits préfabriqués en béton a en effet décidé cette année-là de se tourner, pour la première fois de son histoire, vers des acteurs de l’innovation situés hors de son giron. Une évolution à laquelle elle s’est résolue après avoir pris conscience de l’importance – et de l’urgence – de décarboner ses activités.
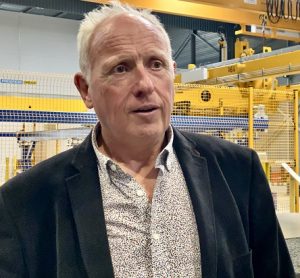
« En 2019, la France a connu un épisode de sécheresse majeur, qui nous a mis face aux conséquences du changement climatique. Au retour des congés d’été, j’ai donc décidé de réunir les équipes de l’entreprise afin que nous trouvions des solutions pour “faire notre part” face à ces bouleversements en cours », se remémore Pierre Bollard.
C’est ainsi tout naturellement vers le ciment bas-carbone – un ciment pouzzolanique CEM IV – que se tourne en premier lieu Spurgin. Un choix qui ne se révèle toutefois pas sans conséquence… Très vite, l’entreprise se trouve en effet confrontée à une conséquence inattendue de l’utilisation de ce ciment sur son outil de production : les éléments de coffrage métalliques utilisés pour donner vie à ses murs en béton préfabriqués – ou « prémurs » – s’oxydent prématurément. Face à cet imprévu, l’entreprise se voit contrainte de mettre en place un roulement entre produits conventionnels et bas-carbone, et limite ainsi la part de sa production faiblement émettrice de CO2 à 12 % environ.
Pour poursuivre malgré tout son parcours de décarbonation, la société familiale se met donc en quête de solutions innovantes développées par d’autres qu’elle-même. Un travail qui aboutit ainsi à la signature d’un premier contrat de partenariat avec un spécialiste des solutions constructives innovantes – Techniwood – et à la création d’un produit bas-carbone baptisé ISO-WOOD, un prémur isolé hybride béton-bois. Séduisante techniquement, la solution pâtit toutefois d’un coût de production relativement élevé, qui amène finalement Spurgin à cesser sa production. « Le produit n’était économiquement pas viable », confie le directeur technique de la société Marc Lenges.
Qu’à cela ne tienne. Entretemps, l’entreprise familiale s’est en effet également rapprochée d’un autre acteur de l’innovation en matière de décarbonation des solutions constructives : Construction Composites Bois, devenue CCB Greentech[1]. Une entreprise née en 2006 en Isère, et qui est à l’origine d’une technologie bas-carbone exclusive et plusieurs fois brevetée : LignoRoc, devenue TimberROC.
Un béton plus « végétal » que minéral
Rebaptisée TimberROC en 2021, la solution permet de donner vie à des murs et des dalles préfabriqués bénéficiant – entre autres atouts techniques et écologiques – d’un bilan carbone particulièrement favorable. Comment ? Grâce à l’utilisation d’une matière première pour le moins inattendue dans le monde minéral du béton : des déchets de bois. Enrichi d’un additif à la composition tenue secrète, ce bois broyé originaire de forêts d’Auvergne-Rhône-Alpes se substitue en effet aux traditionnels granulats qui entrent dans la composition du béton conventionnel, pour donner ainsi naissance à un véritable « béton de bois ». Une formulation d’un nouveau genre, qui confère aux éléments préfabriqués l’avantage d’un bilan carbone négatif, mais aussi une très bonne stabilité dimensionnelle, principal défi qui restait à relever pour pouvoir faire entrer dans le monde du bâtiment ce matériau utilisé jusqu’alors uniquement pour la fabrication de murs antibruit, comme nous l’expliquait en avril 2024 la directrice marketing et du développement commercial de CCB Greentech, Caroline Gérard.
« Début 2020, nous avons donc signé un accord de licence avec CCB Greentech, et nous sommes ainsi devenus les deuxièmes licenciés de l’entreprise iséroise », retrace Pierre Bollard.
Fin 2021, Spurgin se lance alors dans une phase de production préindustrielle[2] au sein de l’une de ses huit usines – réparties sur cinq sites industriels implantés tout à travers l’Hexagone –, celle de La Roque-d’Anthéron, dans les Bouches-du-Rhône.
Une première étape suivie par l’inauguration, au mois de juin 2024, d’une toute nouvelle unité industrielle implantée à Mignières, à quelques kilomètres de Chartres, aux côtés d’une usine préexistante[3] dédiée à la préfabrication de produits en béton minéral conventionnel et bas-carbone.
Fruit d’un investissement de 13 M€, cette nouvelle unité entièrement tournée vers le béton de bois devrait à terme assurer une production annuelle de pas moins de 300 000 m2 de murs préfabriqués à partir de ce matériau vertueux. Ceci, grâce des outils de production automatisés installés sur une surface couverte de 5 000 m2, que Pierre Bollard et Marc Lenges, accompagnés de Fabien Panel, responsable de l’activité Béton de bois de Spurgin, nous invitent tous trois à découvrir au lendemain de son inauguration officielle.
Un procédé de préfabrication largement automatisé
Quelques jours avant sa mise en service, l’usine est encore figée. On peut toutefois d’ores et déjà y découvrir l’intégralité des équipements qui entreront en action d’ici peu, sous la houlette d’une quinzaine de salariés, pour l’heure, et d’une quarantaine à terme, lorsque l’usine fonctionnera en « 3×8 ».
À l’extérieur, une centrale à béton assure tout d’abord la préparation du mélange eau-ciment-granulats de bois. Des granulats que CCB Greentech fournit à Spurgin déjà additivés. Le mélange est ensuite acheminé jusqu’au « carrousel » qui siège au sein du hall couvert de l’usine.
Là, le premier maillon de cette chaîne de fabrication largement automatisée est incarné par un robot de coffrage. « Les plans des pièces établis par l’architecte et notre bureau d’étude sont transférés à la machine, qui va alors disposer sur une table, de manière entièrement automatique, les éléments de coffrage périphériques en métal », décrit Pierre Bollard. Pour les murs comportant des ouvertures, un « mannequin » en bois est également ajouté à l’ensemble, manuellement cette fois. Une fois prête, cette table est alors déplacée vers un poste de bétonnage, où le mélange de béton de bois est réparti au sein du coffrage. « Ce béton est foisonné, il est donc nécessaire de le tasser », souligne Pierre Bollard. Après un arasage de la matière à deux centimètres au-dessus des bords du coffrage, une compacteuse se charge de l’opération, réalisée en deux passes, comme le précise Fabien Panel.
Une fois compacté, puis contrôlé, l’élément en béton de bois est immédiatement décoffré. « Ainsi tassé, le béton de bois tient en effet tout seul, comme un château de sable », illustre le DG de Spurgin. Pour qu’elle se solidifie définitivement, la pièce est toutefois acheminée vers une étuve, où elle est maintenue à une température de 30 °C pendant 24 heures.
À l’issue de ce séjour, les éléments achèvent leur parcours sur une deuxième partie de la ligne de production, où ils sont tout d’abord retournés, avant que ne soient réalisés des renforts en béton – conventionnel cette fois – au sein de réservations préalablement ferraillées. « Ces chaînages servent de renfort pour ces murs porteurs préfabriqués, comme cela serait le cas pour une maçonnerie traditionnelle », explique Pierre Bollard.
Le procédé permet ainsi de donner naissance à des murs porteurs[4] d’une dimension maximale d’un peu plus de 3,6 m de haut, pour 8 m de long et 24 ou 30 cm d’épaisseur. Des éléments préfabriqués que Spurgin est pour l’heure en mesure de livrer en l’espace de huit semaines à partir de l’envoi des plans par l’architecte.
L’espoir d’une montée en puissance
Cet outil industriel désormais prêt à produire en masse ces murs préfabriqués en béton de bois, reste désormais à Spurgin à faire connaître cette solution constructive vertueuse… « La prescription est quelque chose qui prend beaucoup, beaucoup de temps », confie le DG de Spurgin. Pierre Bollard qui compte toutefois, notamment, sur la mise en place de la RE2020 et de ses objectifs en matière de décarbonation, pour pousser l’adoption de cette solution constructive vertueuse auprès des architectes et autres maîtres d’œuvre. « Sortis d’usine, ces murs en béton de bois sont certes plus chers, mais présentent bien d’autres avantages : déphasage et résistance thermique, isolation phonique, mais aussi bien sûr, stockage de carbone », fait valoir le dirigeant.
Autant d’atouts qui ont d’ailleurs déjà séduit de premiers clients, comme en témoignent notamment les deux gros chantiers sur lesquels la solution constructive sera prochainement mise en œuvre : celui de la Cité Scolaire de Sartrouville, ainsi que celui du Nouvel Hôpital Psychiatrique de Tours (NHP). Deux projets pour lesquels un total de près de 15 000 m2 de murs préfabriqués en béton de bois sortiront ainsi, dans les semaines à venir, de cette toute jeune unité de production lancée par Spurgin sur son site de Mignières. Un frémissement qui augure peut-être, comme l’espère en tout cas Pierre Bollard, d’une croissance exponentielle de la demande.
En matière d’innovation bas-carbone, Spurgin a plus d’un tour dans son sac…
Signe que l’entreprise a résolument adopté la voie de l’innovation externe, Spurgin a profité de l’inauguration de sa toute nouvelle unité de production de murs porteurs en béton de bois pour en faire l’écrin d’autres principes constructifs vertueux sur lesquels elle mise désormais. Outre son prémur à galettes, nous avons en effet pu découvrir une série d’innovations développées par d’autres qu’elle, et notamment un mur préfabriqué en bois-paille distribué pour l’heure par l’entreprise bourbonnaise Activ Home. Un acteur de l’innovation que Spurgin compte d’ailleurs bientôt faire entrer dans son giron, comme nous l’a révélé Pierre Bollard.
Autre exemple de ce « changement de culture » qu’évoquait son dirigeant, l’entreprise a également investi il y a peu dans la start-up Terrio, séduite par ses blocs en pisé (terre crue) préfabriqués.
Spurgin n’en délaisse pour autant pas complètement l’innovation interne, et a pour cela décidé d’adosser à sa toute nouvelle unité de production de murs en béton de bois de Mignières un laboratoire de R&D qui sera animé par une équipe de trois personnes à plein temps[5] dès septembre prochain.
[1] CCB pour Carbon Capture Buildings.
[2] Avec une capacité de production annuelle d’éléments en béton de bois de l’ordre de 30 000 m2.
[3] Ouverte en 2011 par Spurgin.
[4] Jusqu’en R+3.
[5] Dont une ex-chercheuse du Centre d’études et de recherches de l’industrie du béton (Cerib).
Dans l'actualité
- CCB Greentech : et le bois devient béton
- XtreeE développe l’impression 3D béton renforcée par des fibres longues
- Une solution modulaire pour adapter les camions-toupies à la livraison de béton en petit volume
- Un supercondensateur à base de ciment, d’eau et de carbone pour stocker l’électricité dans les structures en béton
- Vers des quotas d’acier vert dans l’industrie automobile européenne ?
- La première maison entièrement construite en matériaux composites