Officiellement créée en octobre 2020, 3Deus Dynamics est le fruit de travaux de recherche menés quelques années auparavant par le Dr Christophe Marquette et le Dr Edwin-Joffrey Courtial, co-fondateurs de la start-up aux côtés de son PDG Julien Barthès. C’est en effet fin 2017 que les deux chercheurs CNRS de l’Institut de Chimie et Biochimie Moléculaires et Supramoléculaires[1] (ICBMS) ont développé, au sein de la plateforme technologique innovante 3d.FAB, un procédé d’impression 3D particulièrement innovant, résolvant les problématiques de l’impression de matériaux viscoélastiques tels que le silicone en matière d’effondrement de structure. Le procédé repose sur l’utilisation, en guise de moule, d’une poudre capable de s’adapter dynamiquement à la forme de l’objet en cours d’impression. Une approche ainsi baptisée « Moulage Dynamique ».
Flairant son potentiel en matière d’applications industrielles, les pères de la technologie se lancent alors en 2018 dans un programme de maturation financé par la SATT[2] lyonnaise Pulsalys. Tant technologique qu’entrepreneuriale, cette phase de développement se révèle « un franc succès », comme s’en félicite le Dr Edwin-Joffrey Courtial, actuel directeur technique de la jeune pousse. Une réussite qui aboutit, fin 2020, à la création de 3Deus Dynamics, à la faveur d’un transfert de technologie réalisée par l’Université de Lyon, détentrice des deux brevets internationaux protégeant le procédé.
Six mois à peine après sa naissance, la jeune pousse lyonnaise réalise une première levée de fonds et devient lauréate du concours d’innovation français i-Lab. Un premier succès pour l’entreprise, confirmé en 2022 par l’obtention d’une subvention de plus de deux millions et demi d’euros dans le cadre du concours européen d’innovation EIC Accelerator.
Actuellement en phase de certification ISO 13485[3], 3Deus Dynamics compte ainsi mettre à profit ces fonds pour accélérer son développement sur un marché prioritaire : celui des dispositifs médicaux. Cofondateur et actuel directeur technique de la jeune pousse, le Dr Edwin-Joffrey Courtial nous dévoile quelques-uns des secrets de la technologie qu’il a contribué à mettre au point, et nous livre les perspectives qu’elle ouvre en matière d’applications industrielles.
Techniques de l’Ingénieur : Comment fonctionne le procédé que vous avez mis au point ? Quel rôle la poudre joue-t-elle dans cette technologie ?
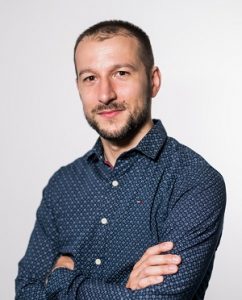
Edwin-Joffrey Courtial : Le Moulage Dynamique est un procédé freeform, c’est-à-dire sans limite de géométrie, dans lequel la poudre joue le rôle de moule dynamique. Cela signifie tout d’abord qu’elle permet de lutter contre la gravité. Sans la poudre, le fluide s’effondrerait sous l’effet de son propre poids, et perdrait ainsi la forme qu’on lui a conférée lors de l’impression. La poudre peut aussi jouer le rôle de charge : en fonction de leur nature, les fluides peuvent avoir tendance, ou non, à faire corps avec la poudre, à la faveur de phénomènes d’imbibition. Nous avons donc développé une profonde connaissance des couples qui peuvent engendrer un mariage intime entre fluide et poudre, ou au contraire pas du tout. On peut ensuite faire appel à des étapes de post-traitement pour retirer l’un ou l’autre. On peut choisir de ne garder que la poudre. On se rapproche alors de ce qui se fait en binder jetting[4] : on ne conserve que l’objet fait de poudre fusionnée. Par ailleurs, l’utilisation de la poudre en tant que moule permet de n’utiliser aucune structure support et donc de réduire considérablement la quantité de déchets industriels.
C’est une approche extrêmement versatile, qui permet de travailler avec de nombreux matériaux autres que le silicone : plastiques, métal, matériaux inorganiques, céramiques… et ce sans aucune reformation chimique. On peut aussi imprimer dans des poudres sacrificielles, que l’on va retirer post-impression. Notre procédé est donc très complet. Ses multiples variantes font qu’il s’adresse à un très grand nombre d’applications.
D’un point de vue très concret, imprimer dans la poudre consiste à utiliser une tête de dépose qui se meut au sein même de ce milieu granulaire. Cela implique donc que la poudre doit se réparer rapidement après le passage de cette tête, afin d’éliminer les crevasses qui se forment. Imaginez, par exemple, imprimer dans de la Maïzena… Cela ne serait pas du tout évident ! Le choix de la poudre repose donc essentiellement sur des questions d’écoulements, de paramètres rhéologiques. Nous savons aujourd’hui définir très rapidement si une poudre peut faire office ou non de moule dynamique, et quels seront les matériaux que l’on pourra imprimer à l’intérieur. Sans en dire trop pour des questions de protection de propriété intellectuelle, je peux simplement indiquer que ces poudres peuvent être de nature organique ou inorganique.
Votre procédé n’implique aucune limite en matière de géométrie… Qu’en est-il des dimensions de l’objet à imprimer ?
C’est effectivement une question très importante, sur laquelle nous nous sommes penchés. En sondant le monde économique, nous avons identifié une forte demande en matière de scalabilité[5] de l’impression 3D. Les industriels ont besoin de pouvoir réaliser en impression 3D des objets de plus en plus grands, mais aussi de petits objets très détaillés… Voire un mélange des deux : de très grands objets avec certaines parties très finement imprimées. De manière assez surprenante, notre procédé se révèle capable de répondre à ces besoins. Nous sommes tout d’abord en mesure d’imprimer des objets avec une résolution inférieure à 50 microns. Cela équivaut à ce qui se fait de mieux sur le marché, avec des technologies sur lit de poudre notamment. Mais nous sommes aussi capables d’imprimer de grands objets, qui tiennent dans un moule dynamique de plus d’un mètre cube.
Il s’agit d’un volume d’impression considérable, avec, en plus, des vitesses d’impression qui sont importantes : on peut atteindre des vitesses linéaires de l’ordre de 500 mm/s, là où les autres approches se cantonnent généralement à des vitesses d’environ 10 à 20 mm/s, voire une cinquantaine pour les plus performantes.
Cela est rendu possible par les propriétés rhéologiques des poudres que nous sélectionnons : elles sont capables de se réparer vite, donc de contenir rapidement le fluide d’impression, et de reprendre leur état statique tout aussi rapidement.
Nous sommes aussi capables – et cela a été l’objet de notre deuxième brevet – de rajouter de la poudre au cours de l’impression. Cela permet donc d’imprimer de très grands volumes, sans les remplir entièrement de poudre dès le départ.
Et nous avons encore plein de cartes à jouer : aller plus loin sur le plan de la résolution, imprimer des multi-matériaux… Nous avons de nombreux projets en cours, qui devraient aboutir à de grandes innovations dans les années à venir. Elles devraient ainsi contribuer à faire du Moulage Dynamique l’une des grandes technologies d’impression 3D.
Quels marchés visez-vous ?
Nous avons défini trois marchés prioritaires : santé, aéronautique et défense. Parmi eux, il en est un que nous avons choisi d’adresser en premier : celui de la santé. Les fondateurs de 3Deus Dynamics sont en effet très impliqués dans cette communauté ; ils disposent d’un important réseau et d’une reconnaissance dans ce domaine.
Le financement que nous avons obtenu dans le cadre du concours européen EIC Accelerator va donc être mis à profit pour concevoir et fabriquer une ligne de production dédiée à ce secteur de la santé. Elle fonctionnera en environnement propre et permettra de réaliser des dispositifs médicaux conformément à la norme ISO 13485 et au règlement européen 2017/745.
Que représente, concrètement, une telle ligne de production, en matière d’équipements et d’infrastructures ?
Nous sommes tout simplement sur le point de déménager… Nous étions en effet pour l’heure hébergés au sein d’Axel’One Campus de l’Université Lyon 1, aux côtés de la plateforme 3d.FAB. Les mètres carrés y sont limités : nous avions jusqu’à présent à disposition une soixantaine de mètres carrés, sans salle propre. Nous allons donc, dans les trois mois qui viennent, déménager dans des locaux de plus de 1 500 m², dont 500 à 600 m² seront dédiés à la santé. Nous aurons des salles propres, dans lesquelles la ligne de production pourra être intégrée.
D’autre part, le concours i-Lab nous a permis de concevoir et de fabriquer notre première imprimante 3D industrielle adaptée à notre procédé de Moulage Dynamique. Il s’agit de la Deus Light. Cette machine tourne déjà dans notre laboratoire. Elle est donc éprouvée, et nous permettra de répondre à des besoins de prototypage ou de petite série, pour des applications dans l’aéronautique et la défense. Cette machine pourra par ailleurs tout à fait être mise à l’échelle pour être utilisée dans des productions industrielles de plus grande série. Nous sommes pour cela accompagnés par un partenaire de longue date, expert de la machine spéciale.
Quel modèle économique comptez-vous mettre en place, à terme ?
Nous avons avant tout vocation à être un apporteur de solutions. Nous développons des produits à très haute valeur ajoutée pour tous les marchés porteurs. Nous n’écartons toutefois pas la possibilité de déployer notre outil de production industrielle directement chez le client avec accord de sous-licences et location d’instruments.
Quelles sont vos perspectives en matière de poursuite de la R&D ?
La R&D de 3Deus Dynamics provient, au départ, de l’université, du CNRS et de sa plateforme 3d.FAB. Ce lien se verra renforcer par la création d’un laboratoire commun de recherche et permettra d’accélérer le transfert des grandes innovations qui feront le Moulage Dynamique de demain.
Pour conclure, je dois dire que je suis moi-même impressionné par l’atteinte, en l’espace de 3 ans seulement, de la phase d’industrialisation de notre procédé. Cela n’a pas été de tout repos, mais le chemin parcouru a été passionnant !
[1] UMR5246, Université Claude Bernard Lyon1, INSA Lyon, CPE Lyon et CNRS
[2] Société d’accélération du transfert de technologies
[3] La norme ISO 13485 est un référentiel de certification volontaire de la démarche qualité développé pour le secteur des dispositifs (Source : AFNOR Certification)
[4] Projection de liant sur lit de poudre.
[5] Possibilité de monter en échelle
Cet article se trouve dans le dossier :
Les matériaux composites boostent la fabrication additive
- Quels matériaux pour l'impression composite 3D ?
- « Valoriser la liberté de conception offerte par la fabrication additive »
- « La fabrication additive sert sur plusieurs étapes des projets »
- « Différents secteurs industriels se mettent petit à petit à la fabrication additive »
- 3Deus Dynamics : l’impression 3D sans limites
- Produire en France une fibre de carbone économique et biosourcée
- Un hydrogel photosensible imprimable en 3D à l'étude
- Reformer les récifs coralliens en utilisant l’impression 3D
- Relocaliser et réparer grâce à l'impression 3D
- Les thèses du mois : "Les matériaux composites boostent la fabrication additive"
Dans l'actualité
- Une solution d’impression 3D métal à 2 lasers qui décuple la productivité et permet de produire des pièces ultra-fiables
- Reformer les récifs coralliens en utilisant l’impression 3D
- Microlight3D : des pièces imprimées en 3D avec une résolution inférieure au micromètre
- G-Éco : l’«imprimerie 3D» engagée
- Relocaliser et réparer grâce à l’impression 3D
- « La fabrication additive sert sur plusieurs étapes des projets »
- Un nouveau procédé de synthèse de silicones sans résidus toxiques
- XtreeE développe l’impression 3D béton renforcée par des fibres longues
- Des hologrammes facilement créés avec un appareil photo
- Stockage sur verre : l’archivage écolo et inaltérable
Dans les ressources documentaires
- Impression 3D dans la simulation en santé - Enjeux en centre de simulation universitaire
- Apport de la fabrication additive à l’intensification des procédés
- L'impression 3D dans une perspective de développement durable
- Impression 3D/4D de matériaux composites thermoplastiques
- Frittage : aspects physico-chimiques - Partie 1 : frittage en phase solide