La fabrication additive par arc-fil ou WAAM est une technologie dérivée du soudage qui fait appel aux équipements standards du soudage à l’arc. Elle est donc théoriquement accessible à toute entreprise disposant d’un robot de soudage industriel ! Voici un rapide tour d’horizon du procédé WAAM.
Dans un précédent article consacré au soudage et à la cobotique, nous avions évoqué l’analogie entre cobotique et fabrication additive (FA), car à l’instar de la cobotique, la FA sort peu à peu du laboratoire pour rentrer dans l’industrie, ce qui est en particulier le cas de la technologie WAAM.
Qu’est-ce que le procédé WAAM ?
Le procédé WAAM est un procédé de fabrication additive métallique directement dérivé du soudage, qui consiste à générer un arc électrique entre un substrat et un fil métallique pour former un cordon.
Il y a peu de différences entre soudage robotisé et WAAM, puisqu’on retrouve les torches de soudage traditionnelles que l’on utilise dans l’industrie pour l’assemblage de pièces. Néanmoins, des améliorations technologiques développées pour le soudage permettent d’optimiser le procédé.
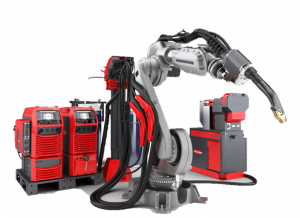
C’est notamment le cas de la technologie CMT, développée par Fronius. Nous avons demandé à Guillain Hardy, ingénieur-soudeur et chargé d’affaires chez Fronius International, de nous en expliquer le fonctionnement :
« En WAAM, Fronius se distingue avec une technologie appelée CMT, pour Cold Metal Transfer. Cela consiste à générer un arc électrique très stable de façon à produire moins de projections lors de la phase de dépose et à limiter la quantité d’énergie apportée à la pièce. En CMT le fil avance et se rétracte mécaniquement environ 120 fois par seconde, ce qui coupe l’arc électrique et limite l’apport de chaleur au fur et à mesure que le dépôt se forme. »
Pour en savoir plus au sujet de la technologie CMT, nous vous invitons à visionner cette vidéo.
La fabrication additive WAAM a de nombreuses applications industrielles
La fabrication additive métallique est de plus en plus utilisée pour le reengineering et la reproduction de pièces qui n’existent plus. Ces technologies permettent ainsi de continuer à faire fonctionner des machines anciennes, en reproduisant des pièces traditionnellement réalisées en fonderie ou par d’autres procédés, avec des délais et coûts de fabrication réduits pour des pièces unitaires ou en petite série.
Par ailleurs, comme tout procédé de fabrication additive, son point fort est la flexibilité et il devient possible de fabriquer des pièces possédant des designs non accessibles par fonderie.
Pour gagner en productivité, il est également possible d’utiliser deux sources de courant et deux fils de soudage sur une même torche. C’est le cas du mode Twin de la technologie CMT, qui double la cadence de production et permet d’atteindre des taux de déposition de l’ordre de 10 kg/h.
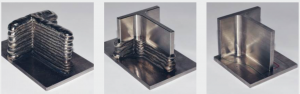
En revanche, comme pour tout procédé de fabrication additive, une fois les pièces réalisées, un post-traitement par usinage reste nécessaire afin d’obtenir des pièces aux cotes voulues. Cet usinage robotisé peut être réalisé directement après l’étape de fabrication, en utilisant un second robot, ou dans certains cas, il peut même être envisagé de le mettre en œuvre directement lors du WAAM.
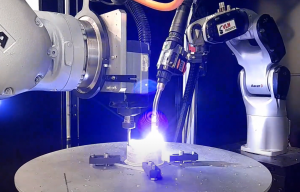
Voici un exemple d’une cellule bi-robots qui combine fabrication additive et usinage in-process. La torche de soudage, fixée à un robot, dépose la matière sur une table rotative et en parallèle, un autre robot est utilisé pour usiner la face extérieure.
L’exemple de Naval Group
L’application industrielle qui fait actuellement le plus parler d’elle concerne la production d’hélices de sous-marin et de bâtiments de surface, notamment par Naval Group.
Pour la réalisation d’hélices, la fabrication WAAM a ainsi de nombreux avantages par rapport au moulage :
- une bonne compacité de la matière ;
- pas de problèmes de criques[1] ;
- pas de retassures ou de particules de sable résiduelles provenant du moule ;
- une réduction des coûts et des délais de production, par rapport à la fonderie.
Par ailleurs, Naval Group semble croire en cette technologie et continue ses travaux d’innovation en l’adaptant à d’autres matériaux métalliques. Un projet européen concernant le développement de WAAM multimatériaux est d’ailleurs en cours, le projet GRADE2XL, ayant pour objectif de développer le changement du métal d’apport en cours de production afin d’apporter localement des propriétés spécifiques (mécaniques, anticorrosion, résistance au frottement…). Cela permettrait ainsi de réserver les matériaux « nobles », donc plus chers à certaines zones spécifiques, et donc de réduire les coûts de fabrication.
Applications en plasturgie : réalisation de moules
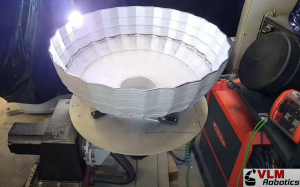
Le WAAM est particulièrement adapté à la fabrication de pièces complexes de grande dimension et notamment de moules pour le rotomoulage de pièces plastiques.
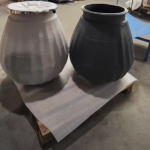
Fronius a par exemple travaillé avec VLM Robotics sur un projet de fabrication de cuves à vin par rotomoulage. Ce type de pièce étant difficile à mettre en œuvre en chaudronnerie, notamment à cause de la présence de nervures sur la pièce, la fabrication WAAM apparaissait comme une solution idéale, surtout que l’usinage n’était pas nécessaire pour cette application.
Une technologie qui a de l’avenir !
Selon Guillain Hardy, « il est très difficile de faire réaliser des pièces forgées et matricées en Europe, car il reste peu de fournisseurs et le savoir-faire s’est perdu. Développer des cellules de fabrication additive WAAM pour réaliser des pièces de quelques grammes à plusieurs tonnes permet ainsi de trouver une alternative compétitive sur le sol européen. »
Compte tenu de ses avantages, la technologie WAAM devrait donc continuer de s’imposer dans l’industrie, bien que la fabrication en grande série ne soit pas encore d’actualité : « Pour le moment, le WAAM n’est pas encore au stade de la production en série et sert surtout à la réalisation de prototypes. De grands groupes comme Naval Group, SNCF, ALSTOM et EDF travaillent activement sur le sujet ainsi que de nombreuses universités et écoles d’ingénieurs. La formation se développe également, tout comme les aspects, certification et normalisation. »
[1] Fissure superficielle dans une pièce métallique
Réagissez à cet article
Vous avez déjà un compte ? Connectez-vous et retrouvez plus tard tous vos commentaires dans votre espace personnel.
Inscrivez-vous !
Vous n'avez pas encore de compte ?
CRÉER UN COMPTE